
A lo largo de los años los procesos productivos en Drummond Ltd., han tenido varios cambios e innovaciones, con la construcción de la idea de actualizar el sistema del cargue directo, trajo consigo la ampliación y modernización de los sistemas de transporte de carbón con las bandas transportadoras ya que permitía el incremento en los flujos y volúmenes de producto a ofrecerle a los clientes.
La compañía optó por la construcción de nuevas bandas transportadoras, las cuales no solo eran más grandes de las existentes inicialmente pasando de de bandas de 72” a bandas de 84”, estas mejoras en proceso productivo de la compañía traen consigo cambios en tecnología, maquinas o equipos que a su vez requieren nuevas herramientas, procedimientos, controles y la identificación adecuada de los nuevos peligros inmersos en la tarea.
La detección de nuevos riesgos potenciales de accidentes, en el caso de la realización de la tarea de cambio de rodillos de retorno de las bandas transportadoras que anteriormente eran de un peso de 25 kilogramos para una banda de 72” pasaron a ser dos rodillos de una dimensión de 1,20 m Con un peso cada uno de 63 kg Para una banda de 84”; A primera vista presento una diferencia considerable en volumen y peso de los rodillos existentes y estos a su vez aumentaba la exposición al riesgo biomecánico de los trabajadores, razón por la cual se inició con la revisión de las matrices de riesgo, procedimientos de seguridad, procesos y métodos de controles que permitieron identificar adecuadamente la jerarquía de los controles resultado la investigación de los accidentes y del análisis causal de los accidentes de trabajo, logrando de esta manera la disminución de los accidentes de trabajo para la realización de la tarea de cambio de rodillo de las bandas transportadoras.
Justificación:
La preocupación por la ocurrencia de los accidentes de trabajo y de mejorar las condiciones de salud de los trabajadores que realizaban la tarea de cambio de rodillo de retorno de las bandas transportadoras fue la motivación principal para pensar en la construcción de una herramienta que nos permita realizar de una forma más adecuada la tarea, controlando los peligros y minimizando los riesgos identificados.
El último accidente realizando este trabajo de mantenimiento ocurrió el 29 de septiembre de 2017, donde un soldador cuando intentaba cambiar el rodillo de retorno, sufre un atrapamiento y golpe en su mano izquierda.
A raíz de este accidente en el proceso de investigación se decidió realizar la revisión del análisis de causas de los diferentes accidentes ocurridos en esta área de trabajo y otros similares en las operaciones del Departamento de Transporte, donde se evidenció que se podrían controlar de manera más efectiva los riesgos si la acción correctiva se enfocará a realizar un control de ingeniería, ya que los controles establecidos hasta esa fecha no estaban permitiendo una gestión efectiva del riesgo.
Objetivo:
Reducir la posibilidad de ocurrencia de accidentes durante la maniobra de cambio de rodillos de retorno, facilitando la ejecución de la tarea, realizando una adecuada identificación de peligros y control de los riesgos inherentes a la tarea.
FASE DE IDENTIFICACIÓN
Una vez presentado el accidente como producto de la metodología de la investigación la causa raíz apunta a procedimientos y herramientas entre otros factores, que originan que se haga necesario la implementación de acciones correctivas que deben estar direccionadas a controles de barreras duras como lo son los controles de ingeniería.
Estos controles deberían ser barreras diferentes ya que las condiciones para la realización de la tarea de cambio de rodillo de retornos habían cambiado significativamente ya que estos habían pasado de ser rodillos con un peso de 25 Kg, a pesar cada uno 63 Kg y unas dimensiones de 120 cm de largo, 25 centímetros de diámetro y un espigo de soporte de 1y 1/2 pulgadas.
Preocupados porque un evento de estos no volviera a ocurrir y trabajar en el bienestar y conservación de la salud y la seguridad de nuestros compañeros de trabajo, los integrantes del departamento de Seguridad Industrial ideamos un mecanismo o herramienta que permitiera el transporte de los rodillos y que además facilitaría el desacople e instalación de los mismos, sin que hubiera exposición a los riesgos antes mencionados; para el desarrollo de esta herramienta se realizaron diferentes bosquejos, sobre los cuales se pudo construir un prototipo que se ha ido mejorando y que fue puesto a prueba, resultando en una mejora del tiempo de trabajo, menor exposición de los trabajadores a los riesgo de atrapamiento y biomecánicos
FASE DE DISEÑO Y ELABORACIÓN DE LA HERRAMIENTA
En primera instancia se procedió a construir un modelo a escala de lo que podría ser la herramienta para realizar el desacople, cargue e instalación de los rodillos, que también fueron representados en hierro y en formato miniatura con un peso proporcional a la estructura; en esta fase se procedió a realizar varios bosquejos producto de intervenciones grupales del equipo de seguridad Industrial, donde además se establece que no existe una herramienta adecuada para realizar la tarea en el mercado y que se hace necesario la fabricación de una herramienta para dicho propósito.
Esta propuesta sencilla se basa en el uso de una palanca simple que sostenga el rodillo y permita desacoplarlo y acoplarlo, posteriormente se piensa en la forma de desplazarlo hasta el lugar de trabajo lo que nos permite idear que debe estar provisto de un sistema de ruedas. Una carretilla es el principio base de la herramienta diseñada y se procede a elaborar una herramienta a escala.
Se procede a la construcción a escala real del prototipo tomando como base una carretilla de transporte de cilindros de Agente extintor que se encuentra en desuso, y adecuándola a los requerimientos de alturas, longitud y resistencias.
Una vez la escala permitió establecer las ventajas y utilidad que podría brindar a primera vista el modelo, se procedió a seleccionar los primeros materiales para iniciar la construcción del prototipo.
Paralelo a esto se construye un modelo de soporte del rodillo de retorno con las dimensiones reales, cercano al taller de construcción de la herramienta que permite hacer las pruebas que se requieran sin afectar la operatividad de las bandas transportadoras y garantizando situaciones controladas, que no representen riesgo para el desarrollo del proyecto
Para garantizar los resultados de las pruebas anteriores se lleva la primera herramienta construida para que sea utilizada en una parada de mantenimiento a uno de los conveyors (21) para realizar pruebas con el personal de mantenimiento a cargo al que se le imparte instrucciones básicas sobre el uso de la herramienta y se les pide cambiar uno de los rodillos, instrucción que se cumple de manera satisfactoria; En esta prueba inicial de campo contamos con el apoyo de la gerencia de la compañía y a este ensayo asiste el gerente de mantenimiento en compañía del superintendente asistente y supervisor líder, a los que se les socializa el uso de la herramienta por parte de los autores.
La presencia del personal de mantenimiento en esta fase del proyecto fue fundamental, Luego de este ensayo, se analizan nuevamente en análisis de los riesgos y se decide realizar unas mejoras en la herramienta para lograr de manera eficaz que este apoyo fuera efectivo en todos los aspectos de la tarea.
Evaluación final: una vez se realizaron varias pruebas se pudo comprobar la facilidad de uso de la herramienta, identificando que las instrucciones requeridas eran muy básicas y dando como resultado una reducción del tiempo de intervención en un 50% aproximadamente, con un esfuerzo menor y la participación de solo dos trabajadores para realizar la labor.
Conseguido el objetivo e identificado el punto de equilibrio de la carga (de 63 kg de peso), se procede a la fabricación de las piezas necesarias para la construcción de la nueva herramienta, que incluyen:
Se construye un segmento metálico con dos “brazos” inicialmente cuadrados y cadenas de amarre, con soporte perforado e inclinación fija, que a su vez lleva adherido con cadena un pasador metálico que permitiera ajustar la altura de la herramienta de acuerdo a la necesidad del procedimiento.
Se validan los dos prototipos de la pieza de los brazos de la herramienta, con la intención de identificar cuál de estos brinda mejor agarre en el procedimiento de desmonte, cargue e instalación. Se selecciona el número dos, con brazos curvos y cadenas de amarre.
Se realiza un nuevo prototipo o brazo de agarre (del rodillo), pero en esta oportunidad a los brazos de agarre se les da una curvatura, para que estos permitan mejor agarre del dispositivo con el gancho de seguridad de la cadena al desmontar.
Un segundo pasador aparece en el proyecto y es usado para permitir al vértice que sostiene los brazos de agarre, un ajuste al ángulo de la inclinación del brazo. El pasador metálico que antes estaba adherido con cadena a esta parte de la herramienta, se procede a ser soldado a la tubería soportada sobre la lámina de alfajor que yace sobre la palanca, para de igual forma permitir ajustar la altura de la herramienta de acuerdo a la necesidad del procedimiento
Se validan los dos brazos de la herramienta, con la intención de identificar cuál de estos brinda mejor agarre en el procedimiento de desmonte, cargue e instalación. Se selecciona el de brazos curvos y cadenas de amarre.
Se añade a la estructura de la herramienta un manubrio a la palanca para facilitar la aplicación de fuerza por parte del trabajador durante el enganche del dispositivo y una lámina en la parte superior de la misma palanca, sobre la que se añade una tercera llanta ecualizable que facilitó “acostar” la estructura sobre el piso y su desplazamiento, una vez desmontado el rodillo.
De igual forma se sumó a la palanca de cargue, una tubería curvada de refuerzo o tipo pie de amigo, para soportar el peso, haciendo la herramienta mucho más segura.
Se realiza la validación final de la herramienta y se verifica que funciona perfectamente.
Gestión del cambio: Luego de la aprobación para implementación de la herramienta, se procede a realizar la gestión del cambio, socializando en los tres turnos de trabajo y específicamente a los encargados del trabajo de mantenimiento a los conveyors de 80” sobre el cambio de procedimiento, la presentación de la herramienta y las instrucciones de uso, apoyados con videos de demostración. (Ver Anexo1)
Se realiza el entrenamiento del personal en el uso de la herramienta, este proceso se desarrolla con los grupos objetivo (personal de trabajadores directos y contratistas de mantenimiento de bandas)
Desde el 2014 año de la implementación del cargue directo Al 29 de septiembre de 2017 se han presentado 6 casos en las bandas transportadoras, de los cuales uno corresponde al rodillo de retorno de las bandas de 80 “ocurrido el 29 de Septiembre de 2017.
Una vez implementada la herramienta, y tomados los correctivos de procedimiento a la fecha Mayo de 2018 no se ha vuelto a presentar ningún accidente ni tampoco se reportaron molestias generadas por posiciones ergonómicas no adecuadas, este indicador muestra los beneficios generados por el uso de la herramienta
El tiempo requerido para cambiar un rodillo en la forma como se desarrollaba anteriormente tomaba aproximadamente entre 40 a 50 minutos, con la implementación de la herramienta se redujo a 15 a 20 minutos, esta mejora operacional está asociada además con menor tiempo de exposición del trabajador en la tarea específica.
La herramienta facilita la labor obteniendo como resultado hacer un menor esfuerzo en el levantamiento de carga, que por efecto de la palanca se ve reducido considerablemente.
La implementación de este procedimiento con la herramienta nueva eliminó en parte el uso de las herramientas utilizadas en la forma anterior, en la que se utilizaban cuatro diferenciales, dos tubos, palancas manuales y mazos de diferente peso.
Con el procedimiento actual se requiere solamente la participación de dos personas, comparado con el procedimiento anterior en el que se necesitaba por lo menos de 3 a 4
El desarrollo e implementación de la herramienta para el acople y desacople de los rodillos de retorno de manera segura evidenció una mejora en la prevención de riesgos teniendo en cuenta los siguientes aspectos:
- Disminuye la manipulación del rodillo evitando al exposición a atrapamiento, golpes y machucones
- Disminuye la fuerza requerida por el trabador para el cambio de rodillo
- Mejora la posición del trabajador evitando posiciones no ergonómicas
- Se requiere menor número de personas para el proceso
- Además de lo anterior se mejoran los tiempos de intervención en el equipo.
Agradecemos a la familia del Departamento de Seguridad Industrial por todas sus ideas y aportes en el desarrollo de esta valiosa herramienta, en aras de prevenir los accidentes, contribuir a la mejora continua de los procesos y propender por un trabajo seguro.
Resolución 1401 de 2007, por la cual se reglamenta la investigación de incidentes y accidentes de trabajo.
Papers relacionados
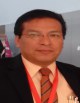
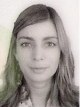
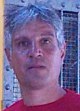

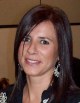
