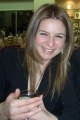
Introduction
The concept of safety climate was defined and operationalized by Zohar [1] in an original work. According the author, safety climate concept “implies that production workers indeed have a unified set of cognitions regarding the safety aspects of their organization”. Accordingly, safety climate concept is used to describe shared perceptions/attitudes of workers in relation to the way as safety management is being operationalized in their workplace [2].
The Zohar’ work give rise to a large discussion about safety climate. Over the years several studies proposing new instruments [3] and showing that safety climate is a predictor of safety-related outcomes as risk perception, safety management systems, accident rates and safety behaviors [3-12] were developed. However, despite the large number of studies about safety climate, it is important to note that some issues are not yet well clarified.
According Brondino et al. [13] theoretical and methodological issues on safety climate are still open. From a theoretical point of view there is still no consensus about safety climate measures, i.e., about the factors that must be considered and the items that are need to be included [10, 12]. From a methodological point of view the discussions are related to the multilevel approach. In most of previous studies the different organizational levels are all mixed, i.e., organizational, group and individual levels are all analyzed at the same level. This practice, according to Zohar [14] must be discontinued in order to avoid the discrepancy errors in safety climate measurement. In fact, different authors claim that, as the scores of the safety climate are aggregated in a single level, the climate relationships in an organization remain unwell specified [14-16]. In view of this, it is possible to found some studies where different organizational levels were analyzed with different scales (see, e.g., Zohar & Luria [15]; Brondino et al. [13]; Rodrigues et al. [17]).
In fact, the new advances on safety climate pointed to the need of instruments that contemplates a multilevel structure. However, it is also need to process the data considering the specificities of a multilevel structure, i.e., determine factor structure through a multilevel statistical analysis.
Bearing this in mind, the present study is an extension of ####, previously published, where an analysis of the advantages of the Safety Climate in Wood Industries (SCWI) instrument to assess the safety climate in furniture companies and a parallelism with the advantages and limitations of a multilevel approach is done.
SCWI Instrument
SCWI (Table 1) is an instrument developed to measure the safety climate in the furniture industry sector, which reflects the current level of safety conditions. It was firstly presented by #### through a pilot study in a furniture company and after date validated through a Multilevel Exploratory Factor Analysis (MEFA) in ####.
Table 1. SCWI tool: items for measuring safety climate.
Organizational Level |
Item |
The management of this company…. |
reacts quickly when a dangerous situation is detected, or there is an accident or incident occurs. |
insists on thorough and regular safety audits and inspections. |
|
is not interested in continually improving safety levels in each department. |
|
does not invest in modernizing work machines. |
|
invests in the implementation of measures to minimize the manual handling of loads. |
|
provides all the equipment needed to do the job safely. |
|
is strict about working safely when we are working under pressure. |
|
requires each supervisor/team leader to help improve safety in his or her sector or department. |
|
invests much time and money in safety training for workers. |
|
uses all available information to improve existing safety rules. |
|
promotes the development of appropriate work procedures for the tasks performed by workers. |
|
does not consider to workers’ suggestions about improving safety. |
|
provides workers with sufficient information on safety issues. |
|
Group Level |
Item |
My supervisor or team leader… |
makes sure we receive all the equipment needed to do the job safely. |
does not check frequently to see whether we are all obeying the safety rules. |
|
discusses how to improve safety with us. |
|
rather than using explanations, compels us to act safely. |
|
worries that I fulfil with the regulations and work procedures. |
|
worries that I use all of the machines protections |
|
lets safety rules and procedures be ignored when we are working under pressure. |
|
frequently tells us about the hazards of our work. |
|
makes that sure we follow all the safety rules, not just the most important ones. |
|
is strict about safety at the end of the shift, when we want to go home. |
|
spends time helping us learn to see problems before they arise. |
|
insists that we wear our personal protective equipment even if it is uncomfortable. |
|
Individual Level |
Item |
I…. |
believe that safety is the main priority when I do my work. |
report dangerous situations immediately to one of my superiors whenever I see them. |
|
try to always follow the rules and work procedures when I run my work. |
|
do not use the personal protective equipment necessary for performing tasks. |
|
do not always use the machine’s protections. |
|
refuse to ignore safety rules, even when the work is delayed and production must be increased. |
|
disregard safety rules at the end of the shift, when we want to go home. |
|
clarify all my questions about the risks to which I am exposed. |
|
do not bring it to my colleagues’ attention when I see them violating some rule or safety procedure. |
The development of SCWI comes up from the lack of specific instruments to measure the safety climate in the furniture sector that contemplates the hierarchical structure of the organizations, particularly one that includes the three levels of analysis (organizational, group and individual). In fact the instrument specific for the furniture sector are scarce and in general only considered a single level of analysis (see e.g. Varonen & Mattila [4]).
The SCWI includes two main parts. The first part refers to demographic questions, such as age, gender, department/sector, professional activity, number of years working at the company, number of years at the applicable professional activity and previous involvement in work accidents. The second part included 34 items for measuring safety climate, analyzing three different levels: organizational, group and individual levels. Organizational level was measured with 13 items concerning management investment in safety issues, continuous improvement of safety systems and safety communication. Group level was measured with 12 items about supervisor concerns regarding workers’ safety practices, involvement in safety issues and effort in regards to rules compliance and safety protection use. The individual level was measured with 9 items concerning workers’ commitment to safety. The description of the items included for each level of analysis is presented in Table 1. The level of agreement with each item was assessed using a 5-point Likert scale that ranged from “1=Strongly disagree” to “5=Strongly agree”.
SCWI and the multilevel approach: Advantages and limitations
The authors in #### identified the SCWI as a suitable instrument to the analysis and monitoring the companies’ safety conditions, as it was found a stronger relationship between the determined dimensions and the work group safety performance. Furthermore, SCWI allows to identify different safety climates among work groups in the same furniture company. This is an important advantage of the instrument, because it can help into identify the most problematic work group in a company. This is in accordance with previous studies, where was emphasized the need of the analysis of safety climate at group level [18]. When the analysis is performed considering all the company, a problematic group can be concealed.
SCWI also considers a multilevel structure. This is also an advantage of the instrument, because it allows to analyze cross-level climate relationships [15]. This is not a new approach. Zohar and Luria [15] proposed an instrument with two levels of analysis, organizational and group levels. According the authors the workers perceptions and attitudes was originated simultaneously from policy and procedural actions of top management and from supervisory actions. In this approach, managers are the responsible to establish policies and procedures, which are executed by supervisors in each work group, deciding how and which procedures to implement (supervisor discretion). Latter, Brondino et al [12] add to the group level the co-workers influence. #### opted for a different approach where a new level was included in SCWI, the individual level, who is related to the respondents’ practices. Workers are responsible for complying with company policies and procedures; however due to rational and perceptual processes that can influence the choices of workers about safety behaviors [16], they can decide to follow the procedures defined by managers, supervisors’ advice, or coworkers’ norms. The division in three different scales gives an instrument that can assess workers’ perceptions/attitudes focused on each level, without sources of confusion for the respondents and giving a picture of the state of safety for each level [12].
The SCWI was validated considering a MEFA. In fact when is considered a multilevel structure with repeated measures, a statistical analysis that considers that specificities is needed, i.e., with repeated measures the variance of the item ratings is influenced by both within- and between- level sources. According Brondino et al. [13] as “the workers within each group are rating the same object, there is inherent correlation in their scores – the data has a multilevel nature, and this must be considered in determining the factor structure”. In this way, the Multilevel Factor Analysis (MFA) appears as the appropriate approach, avoiding the traditional problems inherent with factor analysis, particularly in respect to the disregard of dependencies in the data. However, despite the importance of a MFA, it is important to note that it have some limitations. This approach is more complex than a traditional factor analysis and need more time and a large sample size. It is also important to note that the factorial structure achieved can be different at within and between levels. According, the results are more complex to analyze.
Conclusions
This paper showed that SCWI is a good instrument to be applied in the furniture sector. It allows the identification of different safety climates among workgroups in the same furniture company and also reflects their safety performance. Therefore, this instrument can be used as an indicator of the safety performance.
One important advantage of this instrument is the consideration of a multilevel approach and its validation trough a MEFA. Despite this type of statistic analysis be emphasized in this work, and seen as the future for the studies about safety climate, the authors have in mind that a MFA is difficult to be applied and can be only used with very large samples, being not applicable to all situations.
References
- 1. Zohar, D., 1980. Safety climate in industrial organizations: theoretical and applied implications. Journal of Applied Psychology 65(1), 96102.
- 2. Cooper, M.D., Phillips, R.A., 2004. Exploratory analysis of the safety climate and safety behavior relationship. Journal of Safety Research 35(5), 497–512.
- 3. Tharaldsen, J.E., Olsen, E., Rundmo, T., 2008. A longitudinal study of safety climate on the Norwegian continental shelf. Safety Science 46(3), 427–39.
- 4. Varonen, U., Mattila, M., 2000. The safety climate and its relationship to safety practices, safety of work environment and occupational accidents in eight woodprocessing companies. Accident Analysis Prevention 32(6):7619.
- 5. Vinodkumar, M.N., Bhasi, M., 2009. Safety climate factors and its relationship with accidents and personal attributes in the chemical industry. Safety Science 47(5), 659–67.
- 6. Arocena, P., Núñez, I., Villanueva, M., 2008. The impact of prevention measures and organizational factors on occupational injuries. Safety Science 46(9), 1369–84.
- 7. Fugas, C.S., Silva, S.A., Meliá, J.L., 2012. Another look at safety climate and safety behavior: Deepening the cognitive and social mediator mechanisms. Accident Analysis Prevention 45, 468–77.
- 8. Huang, Y.H., Chen, J.C., DeArmond, S., Cigularov, K., Chen, P.Y., 2007. Roles of safety climate and shift work on perceived injury risk: A multilevel analysis. Accident Analysis Prevention 39(6), 1088–96.
- 9. Johnson, S.E. 2007. The predictive validity of safety climate. Journal of Safety Research 38(5), 51121.
- 10. Lu, C.S., Yang, C.S., 2011. Safety climate and safety behavior in the passenger ferry context. Accident Analysis Prevention 43(1), 329–41.
- 11. Nielsen, K.J., Rasmussen, K., Glasscock, D., Spangenberg, S., 2008. Changes in safety climate and accidents at two identical manufacturing plants. Safety Science 46(3), 440–9.
- 12. Rundmo, T., 2000. Safety climate, attitudes and risk perception in Norsk Hydro. Safety Science 34(13), 4759.
- 13. Brondino, M., Silva, S.A., Pasini, M., 2012. Multilevel approach to organizational and group safety climate and safety performance: Coworkers as the missing link. Safety Science 50(9), 1847–56.
- 14. Zohar, D., 2010. Thirty years of safety climate research: reflections and future directions. Accident Analysis and Prevention 42(5), 1517–1522.
- 15. Zohar, D., Luria, G, 2005. A multilevel model of safety climate: crosslevel relationships between organization and grouplevel climates. Journal of Applied Psychology 90(4), 61628.
- 16. Guldenmund, F.W., 2007. The use of questionnaires in safety culture research – an evaluation. Safety Science 45(6), 723–43.
- 17. Rodrigues, M.A., Arezes, P., Leão, C.P., 2013. Development of a multilevel safety climate measure for furniture industries. In: Arezes P, Baptista JS, Barroso M, Carneiro P, Cordeiro P, Costa N et al. (Eds). Occupational Safety and Hygiene. p.515519. London: Taylor & Francis.
- 18. Harvey, J., Erdos, J., Bolam, H., Cox, M.A.A., Kennedy, J.N.P., Gregory, D.T., 2002. An analysis of safety culture attitudes in a highly regulated environment. Work Stress 16(1), 1836.
Papers relacionados

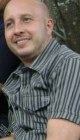
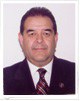

