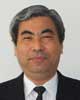
Introduction
One of the characteristics of labour market in Japan is the existence of “internal labour market”. Usually big companies try to employ newly graduated students and provide them a long-term employment (sometimes it refers as “life-time employment”) with continuous in-house training and skills development for their career development. Workers are promoted mainly based on their career within their companies since long- year experience within a company means that the workers acquire enough skills to be promoted and companies hesitate to fill-up a vacant post from “external labour market”. Workers show their loyalty to the companies and hesitate to leave. They do not want to go into the external labour market because they might miss a good career development opportunities within the company.
The internal career development system enables a bottom-up activity such as Kaizen (improvement) and 5S (Seiri (Sort), Seiton (Systematize), Seisou (Sweep), Seiketsu (Sanitize) and Shitsuke (Self-discipline)). This bottom-up system is one of the key factors in strong Japanese manufacturing industry. It also makes functional of prevention of occupational accident caused by unsafe act.
Globalization and standardizations are going on in the world of occupational safety and health (OSH) such as Occupational Safety and Health Management System (OSHMS). OSHMS is a top-down system while Japanese working culture is characterized by in-house training system and bottom-up system such as Kaizen, 5S and KYT (Hazard Prediction Training) which contribute to Japan’s strong competitive power especially in manufacturing industry. Japan Industrial Safety and Health Association (JISHA) developed its OSHMS standards for certification in 2003. The tools for bottom-up system and other voluntary workplace activities are incorporated into the JISHA standards and these tools become good basis in hazard identification and risk estimation at workplaces.
This paper presents how Japanese companies effectively adopt OSHMS, which is designed in different working culture, by combining top-down system and bottom-up system.
Methodology
Statistical data was collected from 47 workplaces of manufacturing industry which were certified by JISHA-OSHMS Standards from 2003 to 2005. Cases were collected from some JISHA-OSHMS certified companies in manufacturing industry.
JISHA-OSHMS Standards were created based on Ministerial Guidelines on OSHMS in Japan and ILO OSH-2001. Bottom-up activities such as KYT*, 5S, hiyari-hatto (near-miss accidents) reporting activities, improvement-suggestion activities, tool-box meeting at the start of work and OSH patrol were incorporated into the Standards.
* KYT aims at preventing accidents due to human error and ensuring safety and health on worksite, at that moment, requires that foremen take the initiative to identify potential dangers at the workplace and work tasks, and take action to avoid accidents. Efforts are made to upgrade workers’ sensitivity to danger, foster their powers of concentration and problem-solving abilities, and increase their eagerness to put these skills into practice.
Results
Figure 1 shows the change in accident rate per 1,000 persons at 47 workplaces of manufacturing industry which were certified by the JISHA- OSHMS Standards in 2003, 2004 and 2005. Most of the certified workplaces belong to big companies so that accident rate is extremely low compare to the average one even before certified. Accident rate of 1 or more days off per 1,000 workers have been reduced after certification from 0.987 to 0.718 and after renewal from 0.718 to 0.604. Continuous reduction of accidents is observed.
Figure 1. Accident rate per 1,000 workers [1]
Figure 2 and 3 show the results of questionnaire to 73 companies of OSHMS Promotion Consortium in 2011. Figure 2 shows the answer of actual effects of JISHA-OSHMS certification. Figure 3 show the answer of expected effects in near future.
Figure 2. Response from Companies on actual effects of JISHA-OSHMS
Figure 3. Response from companies on expected effects in near future
Many companies feel risk reduction and upgrading OSH level as actual effects of JISHA-OSHMS, and expect reduction of accidents and upgrading productivity in near future.
Discussion
Risk Assessment/Reduction and Bottom-up System
Usually risk at work is assessed and reduced by the 5 steps, namely 1) identification of hazards, 2) estimation of risk, 3) evaluation of risk, 4) decision of countermeasures, and 5) action for risk reduction. The most important and difficult step is 1) identification of hazards. Companies which implement KYT and other bottom-up system have advantage to correctively find and identify hazards at actual workplaces by workers. They are able to do so since workers are the best persons who know the actual workplaces and they have been trained every day by the bottom-up system.
Even companies, which introduce risk assessment and reduction system, face with residual risk and KYT is a good tool to fight against residual risk because KYT upgrades workers’ sensitivity and behavior to hazards at their workplaces.
Effects of JISHA-OSHMS
OSHMS is the one which upgrades OSH level in the company by top-down PDCA (Plan-Do-Check-Act) cycle. JISHA-OSHMS was carefully designed to adopt this top-down system into Japanese working culture characterized by bottom-up system. Around 70% of the companies which were certified by JISHA-OSHMS pointed out the risk reduction as an effect of JISHA-OSHMS and the statistical data shows the reduction of occupational accidents even in the big companies who had good record in terms of OSH. These imply that the JISHA-OSHMS is functioning by workers’ participation to the system.
Around 23% companies expect the upgrading productivity in near future. It seems that activation of OSH activity stimulates bottom-up activities, which are the source of competitive power of strong Japanese manufacturing industry.
Some cases in overseas Japanese-affiliated companies which introduced JISHA-OSHMS show the drastic decrease of occupational accidents. They introduced OSHMS step-by-step since the companies had no experience in bottom-up system. This is just a way which Japanese big companies have taken in the past.
Analysis of accidents 5S, KYT, etc. Risk Assessment OSHMS
Figure 4. Step-by-step introduction of OSHMS
Conclusions
Many Japanese companies have been improving productivity and quality of products by bottom-up incorporated production system such as Kaizen (improvement) and 5S. Workers are continuously trained in the company such as in-house training and OJT (on the job training), and become good ones who are able to work in pro-active way and implement PDCA cycle at workers’ level. JISHA-OSHMS, which incorporates bottom-up activities into the top-down management system, is functioning in occupational risk reduction at work and highly expected to have an impact on productivity as well.
It seems that the number of occupational accidents in recent years reaches the limit, but we might be able to break through the limit by proper introduction of OSHMS.
Acknowledgement
We thank to the JISHA staff especially in OSHMS Audit Center for collecting data and cases.
References
- 1. OSHMS Audit Center, JISHA (2013); Review of ten years on JISHAOSHMS. Journal of Industrial Safety & Health, No.4, Vol.14 (2013) 329333, ISSN: 18810462 (in Japanese)
- 2. Ministry of Health, Labour and Welfare; Statistics on occupational accidents, Website on Safety at Work, http://anzeninfo.mhlw.go.jp/user/anzen/tok/anst00.htm (in Japanese)
- 3. Japan Industrial Safety and Health Association; JISHA Annual Report 2013, https://www.jisha.or.jp/international/pdf/JISHA_Annual_Report_2013.pdf
Papers relacionados
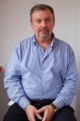

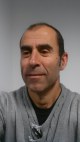

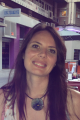
