Andersen, Vibeke
National Working Environment Authority, Landskronagade 33, DK-2100 Copenhagen 45 39152694 / vga@at.dk
ABSTRACT
The National working Environment Authority (NWEA)in Denmark has been working with prevention of musculo-skeletal disorders MSD related to heavy lifting and monotonous, repetitive work under the 10 years action program for a “Clean working environment 2005”. We describe the intensions and objectives with the program, the instruments we have used, the adjustments during the period and have a look at the evolution in reported MSD related to lift and repetitive work.
Keywords
Keywords
National prevention program, MSD, heavy lifting, monotonous repetitive work.
INTRODUCTION
In 1995 the Danish government presented an action program as a framework to intensify the future prevention effort in the work environment area. The overall aim was to make Danish workplaces safe, healthy and inspiring, to the benefit of the employees and the competitiveness of the enterprises. The program was preceded by a broad public debate. The program was drawn up I cooperation with the social Partners and received broad support in the Danish Parliament (Folketing).
Central in the program was 7 visions. 5 were well known and documented problems, which required continued attention and the 2 last were new problems.
The visions were to minimize or avoid all together:
- fatal accidents caused by factors in the working environment
- occupational exposure to carcinogenic chemicals and occupational brain damage due to exposure to organic solvents or heavy metals
- occupational injuries to children and young people
- injuries caused by heavy lifting and occupational diseases resulting from monotonous, repetitive work
- damage to hearing due to noisy work
- damage to health caused by psychosocial risk factors at work
- diseases or serious problems because of a poor indoor climate at the workplace
These was objectives, which the actors should strive to achieve, there was no objective quantified goals.
Players
The overall aim was to encourage enterprises own effort for a good working environment. The national working environment authority (NWEA) should support the
enterprises according to their will and ability to solve their working environment problems.
At sector level the Sector Safety Councils could support the enterprises, and then occupational health service (OHS) could give advice to the enterprise.
Foundation was given by the government to support different activities within the program.
Instruments
General model for inspection: Adapted inspection. A new method was made. The Inspection is solution-oriented and takes into consideration the enterprises’ own efforts to improve the working environment (management) and level of prevention (standards of working conditions) in the enterprise. As an element of the adapted inspection, the NWEA breaks down the enterprises into three levels for the purpose of using the resources on the enterprises, which have the greatest needs.
The vertical axis shows the level of own effort e.g. the work place assessment, standard of the work in the safety organization, education of the members of the safety organization etc.
The horizontal axis shows the actual standard of working conditions in the enterprise,
the level of prevention. The result will be that the enterprise ends with a 1, 2 or 3 level, where 3 is the worst and 1 is the best.
The aim was to make a prioritizing of the resources in the NWEA on the enterprises, which have the most hazardous working environment conditions. But it seems to stimulate the enterprises to activities and will be used for more purposes in the future.
Other instruments
Specific evaluation models for lifting and monotonous repetitive work used by the labour inspectors and the safety organization at the enterprises
Heavy lifting
Evaluation model
Theu model was made in 1986. The traffic light colors red, yellow and green has proved to make the use of the model easy to understand and to use in practice. From the labour inspectors point of view a model shall be easy to use within short time, the result shall be equal for different inspectors when they evaluate the same task, and the need for other instruments shall be minimal e.g. for measuring tape.
The weight is at the vertical axis the distance from the body at the horizontal axis Lifting in red zone means health risk
Lifting in yellow zone has to be evaluated according to the aggravating factors Lifting in green zone; weight in relation to distance is not a problem.
Last an overall assessment of the risk included the aggravating factors has to be done.
The model and the use of it and description of the aggravating factors is implemented in a guideline about lift, push and pulling. The guideline is based on the EU directive about manual handling.
If the actual work is not in compliance with the guideline the enterprise will receive guidance notes and/or improvement notice (only level 3 enterprises).
MSD caused by lifting
1,4
![]() |
1,2 |
1
0,8
0,6
0,4
0,2
0
1993 1994 1995 1996 1997 1998 1999 2000 2001 2002
All Back Neck, shoulder and arm
Incidents pr. 1000 employees of work related MSD from 1993 to 2002
There are a statistical significant decrease in the incidents of disorders
Important sectors in focus has been: Social and Health services
Iron and metal industry
Building and construction Food industry
Transport
Monotonous repetitive work evaluation model
From 1993 – 2000 the social partners has an action plan to reduce the monotonous repetitive work in the industries with 50%. This ambitious goal was not reached but the result was a reduction about 25% mostly by technological changes, simpler job organisational changes (job rotation) and outsourcing of the work to other countries or to small sub suppliers.
The NWEA together with Danish researchers and the social partners agreed in 1994 on the following model for evaluation of the monotonous, repetitive work.
Model for assessment of monotonous repetitive work
Prime factors |
|
High repetitive |
Work is characterized by a work cycle of less than 30 seconds or by repetition of equal movements for more than 50 % of the cycle time or observation time |
Low repetitive |
Work is characterized by not being high repetitive, but a work cycle is between 30 seconds and 5 minutes, or repetition of equal movements is between 50 % and 10 % of the cycle time or observation time |
Time |
Monotonous repetitive work during more than 1/2 working day or 3 -4 hours pr. day shall be mapped and evaluated. If there are aggravating factors also monotonous repetitive work of shorter duration shall be evaluated. Time pressure shall be included in the evaluation |
Aggravating factors |
|
Force |
Force demands e.g. use of hand tools, control actuators, handling or preparation of work items or materials |
Work positions, work place design and variation possibilities |
Improperly, not ergonomic work place design. and/or fixed work position with out possibilities for variation |
Attention, concentration, vision or hearing demands |
Performance of the work require constantly attention and/or concentration e.g. precision work or sort out work. Constantly demands to vision or hearing |
Scope of action |
Little possibility to influence working conditions, pace, contents, practices or techniques |
After mapping the factors an overall assessment of the risks has to be done. The labour inspectors react if the monotonous repetitive work pr. day or pr week has a duration for considerable more than half working day or week, shorter if there are aggravating factors.
During the period with the social partners action plan the NWEA the labour marked partners was the main players. But after the end the activities have reduces even the item since 2002 has been given high priority in the adjustment of the action plan. It seems difficult to progress further, and a new strategy are needed.
MSD caused by monotonous repetitive work
1,6
![]() |
1,41,2 |
1
0,80,60,40,2
0
1993 1994 1995 1996 1997 1998 1999 2000 2001 2002
All Neck shoulder and arm, Back
There are a statistical change in the evolution but no decrease. Important sectors in focus has been:
Food and beverages industry Iron and metal industry Other industries
Cleaning companies
During the2005 action program there has been adjustments in the plan.
During the program the most unsafe 10 jobs was pointed out. Job categories with both many serious work environmental factors and high amount of health problems was selected.
Later in the program 4 highly prioritized areas was pointed out to be in focus.
2 of the 4 item are lifting and monotonous repetitive work, the other was psychosocial factors, and accidents.
The inspectors have concentrated their visits in 16 sectors with the most problems within the 4 prioritized areas
The activities are still ongoing and the final result will be evaluated in 2006.
ACKNOWLEDGMENTS
Injuries caused by heavy lifting has been reduced but not avoided all together. Occupational diseases resulting from monotonous, repetitive workhas not decreased inthe period.
Further investigation of the prevalence of monotonous repetitive work in selected job sectors suggests a decrease in some sectors e.g. in the industries while monotonous repetitive work seems increased in other sectors e.g. with the increasing use of computers. There is a need for new strategies and instruments in the future to continue the activities at the enterprise level.
REFERENCES
D.3.1 Løft, træk og skub
D.3.2 Ensidigt belastende arbejde og ensidigt gentaget arbejde
Overvågningsrapport 2002 (Supervision report 2002) from the Danish National Working Environment Authority
Council Directive 90/269/EEC of 29 May 1990 on minimum health and safety requirements for the manual handling of loads where there is a risk particularly of back injury to workers.
Papers relacionados



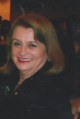

