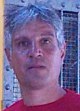
Todas las Industrias, sin tener en cuenta su tamaño, deben cumplir con la legislación medioambiental relacionada con sus procesos productivos. El manejo limpio y responsable de los residuos es posible y no sólo redunda en evitar multas y riesgos para la salubridad pública, también es un factor determinante para mejorar la productividad, aumentar la competitividad de la empresa y, por si fuera poco, obtener beneficios económicos. Por lo tanto, todas las compañías se benefician del conocimiento de las técnicas de prevención de la contaminación que, si se llevan a cabo, pueden incrementar la capacidad de la compañía para cumplir con estas exigencias.
El incorrecto manejo de estos residuos afecta, significativamente, el bienestar y la salud de todos. Los riesgos de accidentes industriales, de contraer enfermedades o de producir impactos ambientales adversos están presentes durante todas las etapas de manipulación del residuo; en su almacenamiento, transporte y disposición final.
Un sistema de gestión es aquel por el que una organización controla las actividades, que causan o podrían causar, impactos ambientales y, así minimiza los impactos ambientales de sus operaciones. Este enfoque se basa en la gestión de “causa y efecto”, donde las actividades son las causas o los “aspectos” y sus efectos resultantes, o efectos potenciales, sobre el ambiente son los “impactos”. Los impactos son, por ejemplo, un cambio en la temperatura media de un arroyo que recibe efluente, o un terreno contaminado como resultado de una infiltración. En consecuencia, la gestión, es esencialmente la herramienta que permite controlar los aspectos y que, por tanto, minimiza y/o elimina los impactos (Hewitt & Robinson, 1999).
También, un modelo de gestión, es un conjunto de personas, recursos y procedimientos que interactúan de forma organizada, cualquiera sea el nivel de complejidad, para realizar una actividad o conseguir un objetivo determinado. Se pueden establecer o diseñar, aparentemente, diferentes sistemas de gestión que se acoplen mejor a las características propias de una organización determinada, pero la esencia debe ser común a todos ellos (Lluna, 1999).
Existen muchas técnicas y tecnologías para la reducción de residuos y para la recuperación de los mismos una vez se hayan generado. Sin embargo, un programa de minimización de residuos no debería contar exclusivamente con la tecnología. Los requisitos fundamentales para el éxito son el compromiso de las máximas autoridades, un programa riguroso de gestión de residuos y un énfasis continuo en la reducción en origen. La recompensa es el cumplimiento de la legislación y una mejor imagen pública. Sin embargo, a pesar del éxito que pueda tener un programa o una gestión adecuada de residuos, no se debe nunca dar por terminado. No es un programa para una sola vez, sino debe ser continuado. Por tanto se deberían realizar mejoras constantes y buscar nuevos métodos de reducción de residuos (Kiely, 1999).
Todo sistema de tratamiento de los residuos debería, preocuparse sobre todo de reducir las cantidades de residuos producidos. Esto eliminaría la necesidad de tratar y eliminar estos materiales.
Existen una serie de ventajas que surgen con la minimización de los residuos (Grüjer, 1991). Estas son:
- La generación de grandes volúmenes de residuos está correlacionada con la disminución de la mayoría de las fuentes no renovables.
- Los requisitos energéticos para la transformación y mejora de las prestaciones de los residuos están proporcionados a la cantidad tratada y aumenta exponencialmente con el incremento de la dilución de los residuos.
- El elevado coste total de la recogida, separación, almacenamiento intermedio, transporte, tratamiento y almacenamiento final, es otro punto a favor de la minimización de los residuos.
- Las siempre crecientes presiones públicas y legislativas parecen mitigarse únicamente con la reducción/minimización de los residuos.
- Ya que los residuos equivalen a pérdida de rendimiento, la reducción de los mismos producirá un aumento de los rendimientos y un mayor provecho.
Los objetivos que nos planteamos fueron:
• Realizar un relevamiento de empresa Pymes de la ciudad de Campana agrupadas por categorías.
• Determinar cuál es el rubro predominante y que residuos generan.
• Plantear estrategias viables de prevención y minimización.
La ciudad de Campana cuenta con empresas e importantes grupos industriales, debido a esto también cuenta con la radicación de Pymes que proveen de insumos a las mismas. Esto provoca una mayor generación de mano de obra en la zona. Por tal motivo es de gran importancia no solo el desarrollo industrial para el crecimiento y desarrollo socio-económico poblacional, sino que es de suma importancia el control del impacto ambiental que estas industrias generan.
La problemática ambiental que generan los residuos no se evita únicamente realizando una correcta gestión de los mismos, es necesario minimizar su generación desde el inicio del proceso productivo. Será bueno aplicar el principio de que el mejor residuo es aquel que no se produce.
En primer lugar se realizó un relevamiento de industrias Pymes de primera y segunda categoría industrial según la (Ley 11459,1996) de Radicación Industrial de la Provincia de Buenos Aires y su Decreto Reglamentario 1741/96. Se encontró que la cantidad de empresas de primera categoría industrial es de 55, la cantidad de empresas de segunda categoría industrial es de 70. Dentro del parque industrial de segunda categoría se encuentran instaladas 9 de las 70 empresas de segunda categoría industrial. Existen 57 empresas que son proveedoras de multinacionales y el rubro mayoritario corresponde al metalmecánico y autopartistas. De estas 57 empresas 14 son de primera categoría industrial y 43 son de segunda categoría industrial.
En segundo término, como respuesta a la necesidad de evitar accidentes laborales y mejorar la competitividad en las Pymes, se realizó una evaluación ambiental de las empresas del rubro predominante metalmecánico. Para determinar la situación actual se realizaron encuestas a través de un formulario sobre los distintos tipos de residuos y cantidades generadas y destino final. Se visitaron diez empresas metalmecánicas en horas laborares acompañados del supervisor, en ellas se observo y se describió la situación actual de la empresa, así como también, listas de chequeo, materias primas y productos, procedimientos, manuales y datos ambientales. Consideramos que las empresas que se visitaron, forman un panorama representativo del total del rubro seleccionado.
Posteriormente se propuso una metodología general como guía para el manejo seguro de los residuos con el fin de reducir los riesgos de accidentes que pongan el peligro a los trabajadores y a los bienes materiales.
En las fábricas y talleres visitados se trabajan metales ferrosos y no ferrosos para hacer o transformar piezas, mediante procesos manuales y/o mecánicos que, en su mayoría, implican el arranque de viruta, algunos de los trabajos incluyen: cortar, tornear, taladrar, fresar, cepillar, esmerilar, pulir, doblar, soldar, limpiar, desengrasar y pintar, entre otros. Estos procesos generan una serie de residuos (sólidos, líquidos y gaseosos) propios del trabajo, entre los que se encuentran algunos catalogados como especiales, es decir, aquellos que por sus características corrosivas, reactivas, explosivas, tóxicas, inflamables, infecciosas o radioactivas pueden generar riesgos o daños para la salud humana, el medio ambiente y la vida en el planeta.
Los insumos son, además de las materias primas de hierro y acero, los materiales auxiliares correspondientes que deben ser aptos para los requerimientos propios del proceso respectivo. Como ejemplo, cabe mencionar la diversidad de aceites y emulsiones especiales.
Los lubricantes y refrigerantes son compuestos utilizados para facilitar las operaciones de trabajo en el metal. Deben también cumplir requisitos de protección a la salud, operaciones subsecuentes, impactos ambientales y disposición final. Pese a que los fluidos de trabajo pueden ser sólidos, líquidos o gaseosos, prácticamente todos los utilizados en la actualidad son líquidos (Foltz, 1990).
La prevención de la contaminación para los fluidos de trabajo debe ser practicada siempre que sea posible. Históricamente, se tendía a disponer los líquidos enfriamiento o líquidos de trabajo tan pronto como mostraran signos de suciedad o disminuyeran su eficiencia. Un programa completo de manejo puede, en teoría, prolongar indefinidamente la vida de estos fluidos (Ohio EPA, 1993).
En general, del proceso de mecanizado, lo podemos dividir en varias etapas básicas.
- Recepción de las materias primas y almacenaje.
- Preparación mecánica de las piezas y materiales
- Limpieza previa
- Mecanizado
- Acabado (pulido, limpieza final, lavado de las piezas)
- Embalaje, almacenaje y expedición.
- Otras operaciones
En la etapa de recepción de las materias primas y almacenaje se producen residuos de embalajes como papel, cartón, plásticos, pallets de madera, etc.
Estos materiales se encuentran limpios no contaminados con aceites y no son residuos especiales. Algunas empresas participan de programas y la Subsecretaría de Ambiente y Desarrollo Sostenible del Municipio efectúa recogida selectiva de algunos de estos materiales.
En la segunda etapa de preparación mecánica de las piezas y materiales, corresponde a los procesos de desbaste o eliminación grosera de excesos de materiales de las piezas y al corte o reducción del tamaño de las piezas para ajustarlas al tamaño de la mecanización.En estos procesos se producen básicamente los siguientes tipos de residuos:
- Limaduras y virutas de metales férreos y no férreos.
- Polvo y partículas de metales férreos y no férreos.
- Residuos de granallados
- Materiales de esmerilado
Los polvos y virutas pueden ir acompañados de partículas del material abrasivo pero se pueden considerar globalmente residuos metálicos. Si estos polvos o virutas van acompañados de aceites o taladrinas deben considerarse como residuos especiales.
En la etapa de limpieza previa se consideran las limpiezas de las piezas para la eliminación de las pequeñas incrustaciones, así como las limpiezas de piezas sucias u oxidadas por el almacenamiento. Los procesos que consideramos en este apartado tienen la característica común que son por vía húmeda.
Residuos que se pueden producir:
- Polvos metálicos y virutas húmedas de agua o disolventes procedentes de desbastes.
- Disoluciones acuosas (ácidas, alcalinas, con sales o aditivos) agotadas.
- Disolventes orgánicos sucios o agotados (clorados o no).
- Aguas de lavado o aclarado
En el caso de que los residuos metálicos vayan impregnados de disolventes deben considerarse residuos especiales debido a que los disolventes son considerados así.
Solamente las aguas de aclarado podrían ir al alcantarillado, previa depuración o no, dependiendo si cumplen con los parámetros de vertido al alcantarillado o al cauce público que apliquen en cada caso. En el caso de sobrepasar los límites de vertido autorizados (por ser concentradas) debería gestionarse como el caso anterior.
La etapa de mecanizado puede comprender entre otras las operaciones de: Corte, Torneado, Fresado, Taladrado, Alisado, etc., y normalmente se utilizan fluidos para la refrigeración y lubricación de las piezas debido a las altas temperaturas que se pueden alcanzar en estas operaciones.
Residuos que se pueden producir:
- Polvos metálicos secos y virutas secas procedentes de operaciones de mecanizado en seco.
- Virutas metálicas y polvos impregnados de aceites o taladrinas procedentes de mecanizados lubricados.
- Residuos líquidos de aceites, taladrinas, disolventes, etc., agotados o sucios.
- Trapos sucios, papeles sucios, absorbentes impregnados, etc., de aceites, grasas, disolventes, etc. (procedentes de limpiezas, derrames, etc.)
En la etapa de acabado (pulido, limpieza final-lavado de las piezas) los residuos producidos en esta etapa son los mismos o son asimilables a los que se han descrito en las etapas anteriores 2 y 3, ya que los procesos son los mismos pero con la pieza acabada.
En la tapa de embalaje, almacenaje y expedición, se producen básicamente los mismos residuos de embalajes que en la etapa de recepción de materias primas: papel, cartón, plásticos, pallets de madera, etc.
En la etapa de otras operaciones, consideramos mantenimiento preventivo de máquinas e instalaciones como en las de limpieza de máquinas y accesorios.
Residuos que se pueden producir:
- Materiales de embalaje en general (papel, cartón, madera, plásticos, etc.) y envases vacíos de materias primas o disolventes (que NO han contenido productos tóxicos o especiales: de pinturas al agua, de disolventes sin símbolos de peligrosidad, etc.).
- Chatarra, metales y piezas metálicas.
- Los propios aceites sucios y los disolventes utilizados sucios procedentes de limpiezas y otros.
- Trapos o papeles impregnados con aceites, grasas, productos químicos en general, disolventes, etc.
- Envases vacíos de materias primas o disolventes (que SI han contenido productos tóxicos o especiales: envases o bidones de disolventes con símbolos de peligrosidad en general, aceites, grasas, sprays, etc.)
- Residuos especiales procedentes del mantenimiento de instalaciones (baterías, pilas, fluorescentes y bombillas, materiales electrónicos, etc.)
De acuerdo a los residuos generados proponemos las siguientes mejoras y minimización para cada una de las etapas:
En la etapa uno.
- Analizar con los proveedores la utilización de envases o contenedores reciclables o retornables.
- Analizar con los proveedores, de la utilización de los mínimos materiales de embalaje que aseguren la correcta conservación de los productos durante el transporte y manipulación.
- Reutilización y reenvió de los materiales a los proveedores (a veces cartones o plásticos de separación entre pisos de piezas pueden ser devueltos y usados de nuevo, también existen cajas de cartón y otros materiales fácilmente plegables que se pueden devolver y reutilizar).
- En cuanto a los pallets de madera, reutilizarlos, y en el caso de existir sobrantes o excedentes analizar la venta de los mismos a empresas que fabrican.
En la etapa dos.
- Analizar las compras de los materiales de partida, de manera de reducir los excedentes al mínimo.
En la etapa tres.
- Considerar los detergentes biodegradables que se acompañan al agua en los procesos de desbaste y abrasión.
- Utilizar métodos de limpieza estandarizados y comprobados, siempre de la misma forma. No “ir inventando” en cada limpieza.
- Intentar utilizar los métodos de limpieza menos agresivos y más respetuosos con el medio ambiente, primero a base de aire a presión y agua (fría o caliente), si no es posible con detergentes acuosos biodegradables, y finalmente las soluciones ácidas / alcalinas y los disolventes.
En la etapa cuatro.
- Utilización de aceites y fluidos de corte que contengan los mínimos productos peligrosos. Hoy en día cada vez se avanza más en este tema y aditivos tóxicos y peligrosos como fenoles, organoclorados, etc., ya se han sido sustituidos por los fabricantes de aceites y taladrinas por otros más respetuosos con el medioambiente.
- La eliminación de sustancias extrañas en estos fluidos, que permite alargar su vida útil. La filtración (continua o intermitente) de los mismos mediante papel de filtro o cartuchos filtrantes para eliminar partículas sólidas y otros. También suele utilizarse la decantación, la separación de los materiales férricos mediante imanes y también el centrifugado.
- La utilización de agua tratada (destilada o desionizada) en la preparación de las taladrinas y emulsiones, y en la reposición del agua por evaporación, también permite eliminar posibles depósitos calcáreos en los circuitos.
- Evitar la contaminación de los fluidos de corte por otros productos y el contacto con el aire (oxidaciones), mediante la protección de las instalaciones con mamparas o tapas, que a su vez reducen las posibles salpicaduras al exterior.
- El Mantenimiento preventivo de estas máquinas e instalaciones. Revisión y reparación de las fugas de los circuitos y sustitución periódica de las juntas para evitar derrames de aceites y taladrinas al suelo y las consiguientes pérdidas.
- Utilizar los mínimos tipos distintos de fluidos y aceites a fin de evitar las mezclas entre ellos y disminuir el stock de los mismos.
En las etapas cinco y seis son las mismas recomendaciones que realizamos en las etapas uno y dos.
En la etapa siete las propuestas de mejoras y minimización son.
- Un residuo especial que se produce son los disolventes de limpieza. Estas operaciones deben realizarse en unas cabinas de limpieza con extracción forzada de aire y/o bien con protecciones personales (mascarilla, guantes, delantales). Nunca deben verterse al alcantarillado y deben recogerse en recipientes adecuados para su gestión.
- Reutilizar los disolventes varias veces. Un disolvente sucio de una limpieza o lavado anterior se puede utilizar para el primer lavado o enjuague de una pieza muy sucia. Utilizar luego disolvente limpio para terminar el lavado y guardar éste para la próxima operación.
- Cada vez más se van imponiendo en el mercado disolventes con menores cantidades de VOC (compuestos orgánicos volátiles), incluso con el 0% de los mismos. Tienen unas formulaciones a base de aceites vegetales de diversos tipos y su poder de limpieza es parecido.
- Utilizar dosificadores de disolventes semiautomáticos o automáticos y regularlos al mínimo. La utilización de los disolventes directamente de los recipientes que los contienen "a chorro" hace que se desperdicien grandes cantidades de los mismos. De la misma forma la utilización de trapos o papeles absorbentes pequeños hace que se consuman menos disolventes.
- La sustitución de los disolventes de limpieza y desengrase (tricloro, percloro, etc.) por detergentes acuosos, más respetuosos con el medioambiente y para la salud de las personas.
- Mantener los recipientes de los disolventes siempre bien cerrados, las máquinas en donde se utilicen con cerramientos o tapas para evitar su evaporación. Recordemos que algunos son inflamables y de riesgo para la salud de los trabajadores.
- En el caso de derrames de aceites u otros, o de goteos de las máquinas es conveniente colocar cerramientos y/o bateas de contención. En el caso de tener que utilizar absorbentes utilizar preferentemente granulados porosos inertes (como sepiolita o similar) antes que serrín, ya que éste al ser combustible aumenta la carga de fuego.
- Aumentar el mantenimiento preventivo y mejorar el correctivo de las máquinas e instalaciones (emplear juntas adecuadas que eliminen las fugas, etc.)
- Respecto a los envases de líquidos, utilizar el tamaño máximo posible a fin de minimizar el número de envases y a ser posible en contenedores retornables o reutilizables.
- Manipular con precaución los envases de aditivos, disolventes, colorantes, etc.
- Formar al personal implicado en estos trabajos a fin de que adquieran unas buenas prácticas y hábitos operativos.
- Una cantidad importante de empresas presenta deficiencias en el manejo de sus desechos desde la etapa de acumulación. En esta etapa, mezclan desechos peligrosos con ordinarios, no se manejan recipientes con la rotulación apropiada ni se realiza una inspección periódica, entre otras deficiencias.
- Los principales contaminantes asociados al rubro son de estado líquidos y están asociados a los compuestos químicos que contiene los fluidos de trabajo y la contaminación por la operación de los mismos.
- En la legislación provincial (Ley 11720,1995) existen recomendaciones sobre el almacenamiento de los residuos peligrosos de acuerdo con sus incompatibilidades, las cuales no necesariamente se siguen en las actividades de acumulación y almacenamiento de las empresas.
- El transporte de residuos especiales se realiza por parte de la mayoría de las empresas cumpliendo con la legislación nacional vigente.
- Varias empresas nos comentaron las dificultades para tratar sus residuos especiales, ya que por su pequeño volumen de residuos generados es más costoso el flete que el tratamiento de los residuos y los tratadores no quieren realizar el retiro de pequeñas cantidades.
- El Art. 49 de la (Ley 11720, 1995) dice: Los municipios podrán, con intervención de la Autoridad de Aplicación y el Consejo Regional respectivo (Ley 11.459), celebrar acuerdos a fin de establecer plantas de almacenamiento comunes con una compensación económica a favor del municipio que la tuviere radicada. Esto podría dar solución al punto anterior, permitiendo aplicar los beneficios de la cooperación entre empresarios para el aprovechamiento de sus residuos, contribuyendo al cuidado del medio ambiente.
- Alrededor de la cuarta parte de las empresas se encuentran en las etapas intermedias de la jerarquía del manejo integral de desechos peligrosos, es decir reusan y reciclan sus desechos. Las tres cuartas partes están en las etapas inferiores de la jerarquía, tratamiento y disposición final.
- La etapa de manejo más frecuente en la cual se encuentran las industrias es la de almacenamiento en espera de un tratamiento.
- Cuando los residuos se manejan de manera adecuada los mayores beneficios se logran al reducir los riesgos de accidentes laborales, creando un ambiente de seguridad en el trabajo.
- Se elaboró y difundió una guía para la gestión y manejo integral de residuos para Pymes, como así también en apoyo al grado de nuestra Facultad en aquellas asignaturas que en su currícula contemplen la prevención de riesgos laborales.
Agradecer a la entidad organizadora del XVI Congreso Internacional de Prevención de Riesgos Laborales (ORP2016) la oportunidad de dar a conocer la investigación realizada.
Foltz, G (1990). Definitions of Metalworking Fluids. Waste Minimization and Wastewater of Metalworking Fluids.
Grüjer, U (1991). Waste Minimisation: A Major Concern for the chemical Industry, Water Sci. Technology, 24(12), 43-56.
Hewitt, R., & Robinson, G. (1999) – ISO 14001 EMS - Manual de Sistema de Gestión Medioambiental – Paraninfo – 1999 – pp. 2
Kiely, G (1999) – Ingeniería Ambiental – Fundamentos, entornos, tecnologías y sistemas de gestión – Mc Graw-Hill – 1999 – Capítulo 18 – Minimización de residuos – pp. 1109
Ley 11720 (1995). De Residuos Especiales – De generación, manipulación, almacenamiento, transporte, tratamiento, y disposición final de residuos especiales en el territorio de la Provincia de Buenos Aires – Anexo I y Anexo II – 2 de noviembre de 1995 – Provincia de Buenos Aires.
Ley 11459 (1993). De Radicación Industrial – 21 de octubre de 1993 – Provincia de Buenos Aires.
Lluna, G (1999) – Sistema de Gestión de Riesgos Laborales e Industriales – Fundación Mapfre - 2ª edición – 1999 – pp. 37
Ohio EPA (1993). Extending the Life of Metal Working Fluids. Fact Sheet - Number 11, March Pollution.
Papers relacionados
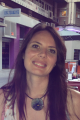
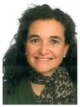


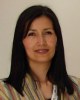