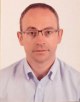


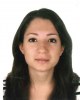
No son pocos los procesos productivos y sectores en los cuáles se manipulan o almacenan sustancias inflamables por citar algunos de ellos tenemos: el sector agroalimentario, textil, químico, reciclado, energético, biomasa, petroquímico, etc., En ellos, y aunque no siempre es así, las instalaciones deberían diseñarse, operarse y mantenerse de manera que los posibles escapes de material inflamable y en consecuencia la extensión de los emplazamientos peligrosos sean mínimos, ya sea en funcionamiento normal o no.
Por ello, es importante examinar aquellas partes de los equipos de proceso, sistemas, etc, en los cuales puede surgir un escape de sustancia inflamable y considerar modificaciones en el diseño para minimizar la probabilidad y la frecuencia de estos escapes y la cantidad y tasa del escape de sustancia.
La clasificación de emplazamientos peligrosos pretende clasificar y analizar el entorno donde puede aparecer una atmósferas explosivas de gas teniendo en cuenta entre otros: las características de inflamabilidad del gas o vapor, tales como la energía de ignición y la temperatura de ignición. El tipo de zona depende principalmente del grado de escape y de la ventilación. Las zonas se conocen como: zona 0, zona 1 y zona 2.
El proceso más importante dentro del control de las atmósferas explosivas es pues, lograr una correcta clasificación zonal y extensión de la zona. Ésta dependerá de la distancia calculada antes de que se produzca la dispersión de la atmósfera explosiva en el aire por debajo del límite inferior de explosividad (LIE).
Para lograr estas premisas, se presentan a continuación dos metodologías: la metodología según la norma UNE 60079-10-1 y la metodología basada en la dinámica de fluidos computacional (CFD).
Metodología basada en la norma UNE 60070-10-1
Esta metodología cuantitativa se muestra esquematizada en la figura 1, y su objetivo determinar el volumen teórico Vz que representa el volumen en el cual la concentración media de gas o vapor inflamable estará entre 0,25 ó 0,5 veces el LIE. Este volumen teórico representa el volumen de la envolvente inflamable desde la fuente de escape, aunque normalmente no equivaldrá al volumen del emplazamiento peligroso. Esto es así, ya que la geometría de este volumen teórico no está definida (si bien se suele adoptar una geometría esférica respecto a la zona de escape) y estará influencia por las condiciones de ventilación.
Fig 1. Proceso de obtención del volumen teórico Vz
Vz: volumen teórico atmósfera explosiva en m3.
fv: factor de eficacia de ventilación en la dilución de la atmósfera explosiva de gas con valores de f=1 (situación ideal) a f=5(circulación dificultosa del aire motivada por obstáculos).
C: número de renovación de aire por unidad de tiempo (s-1).
Qvo: medida de caudal total de aire fresco a través del espacio considerado.
Vo: volumen afectado por la ventilación real en las proximidades del escape.
G: tasa de escape máxima de escape de la fuente (masa por unidad de tiempo, Kg/s).
LIE: limite inferior de explosividad (masa por unidad de volumen, kg/m3).
K: factor de seguridad aplicado al LIE, normalmente: K=0,25 y =0,5.
T: temperatura ambiente (en grados Kelvin, K)
La metodología (que se muestra en la figura 1) conlleva los pasos siguientes:
1. Determinación de la tasa de escape: G
2. Evaluación de la tasa o caudal mínimo de ventilación necesario para impedir la
formación de una atmósfera explosiva : Qvmin
3. Determinación del número de renovaciones de aire: C
4. Cálculo de un volumen Vz (m3).
5. Determinación del tipo de zona (zona 0, zona 1 o zona 2) mediante la tabla 1
“Clasificación de zonas según la ventilación”, fijando como variables el grado de escape definido y el grado y disponibilidad de ventilación (tablas 2 y 3).
6. Cálculo de la extensión de la zona a partir de Vz.
Fig 2.Volumen teórico de atmósfera alrededor de la fuente de escape
A partir del volumen teórico Vz se puede determinar el radio de la esfera ficticia de extensión de la zona a clasificar (fig. 2).
Tabla 1. Clasificación de las zonas ATEX según la ventilación y el grado de escape
Tabla 2. Grado y disponibilidad de ventilación en espacioes interiores
Metodología CFD
La metodología que se propone a continuación se basa en la dinámica de fluidos computacional, para ello se utiliza el software comercial FLUENT de Fluent, Inc. FLUENT es un software líder mundial en soluciones CFD que permite solucionar mediante iteracciones del flujo de fluidos y balances de energía. Los balances generalizados son las ecuaciones de Navier Stokes para la conservación de masa y momento. Se solucionan ecuaciones adicionales de transferencia de calor, mezcla de especies o reacción o ecuación de conservación de especies o modelos de turbulencia.
Aplicación de la metodología según norma UNE 60079-10-1 al caso práctico de sala de calderas
Esta sala consiste en un recinto rectangular con superficie en planta de 99 m2 (9m x 11m) y un volumen de 352 m3 que dispone de dos calderas de vapor alimentadas con gas natural con quemador por aire forzado que producen 6000 kg/h de vapor que proporciona alimentación a la fábrica láctea. El emplazamiento dispone de dos entradas/salidas, la entrada principal dispone de una superficie de 2,64 m2 (1,20m x 2,20m) y conduce al exterior. Se dispone de una puerta salida secundaria de la sección de calderas que conduce a una sala previa a la zona de compresores con las mismas dimensiones que la anterior.
Los circuitos de línea de quemador para ambas calderas son simétricos, la tubería principal (fig. 3) proveniente de los depósitos de GNL (gas natural licuado), entra a la sala de calderas para alimentar el quemador de las mismas donde se dispone de válvula de corte manual (fig. 4) y de ésta, al circuito de línea de los quemadores (fig. 5).
Fig 3. Tubería de gas Fig 4. Válvula de corte manual Fig 5. Línea de los quemadores
La conducción del gas pasa después de precalentarse a través de un circuito en serie (fig. 5) compuesto por una válvula manual de corte, una válvula reductora de presión de gas, un filtro, una válvula reguladora de presión de gas y una válvula automática de corte. De ésta última válvula parten dos conducciones, la superior es la de la llama piloto y la inferior conduce a la entrada-alimentación del quemador (fig. 6).
Fig 6. Disposición de las conducciones de llama piloto y quemador de la caldera
Identificación de las sustancias inflamables
Definidas las características generales de la sala, procedemos a identificar las sustancias inflamables. El combustible utilizado es gas natural licuado cuya composición en más de un 92% es metano, el resto del porcentaje se lo reparten el propano, el butano y el gas odorificante. Para simplificar los cálculos vamos a considerar que todo el gas es metano (CH4) cuyas características se establecen en la tabla 3.
Tabla 3. Parámetros característicos del gas metano (CH4)
Fuentes de escape
Las posibles fuentes de escape son los distintos elementos de la línea que conducen al quemador: bridas, válvulas embridadas, roscas de instrumentación, filtro con bridas a ambos lados, etc.
Grados de escape
Los grados de escape existentes son de tipo primario y son: válvula de entrada de la línea exterior de gas y línea del quemador (válvula manual de corte, válvulas reguladoras de presión del gas, filtro, válvula automática de control de presión de gas y válvula automática de corte).
No existen grados continuos ni grados secundarios de escape.
Influencias de todos los escapes
Como tenemos 6 elementos en los cuales pueden aparecer escapes primarios, calculamos el caudal de aire fresco Qmín para todos los escapes, se suman el de los 3 mayores (válvula manual, válvula reguladora de presión y filtro) para los cálculos posteriores.
Cálculo de la tasa de escape
Los valores tabulados obtenidos de la bibliografía para una temperatura de operación de 40 ºC (caso más desfavorable) son:
-
Válvula manual de corte (entrada conducción de gas): 2,08x10-8 kg/s.
-
Válvula manual de corte (línea de quemador): 2,08x10-8 kg/s.
-
Dispositivo de control de presión: 2,08x10-8 kg/s.
-
Válvula reguladora de presión: 5,20x10-8 kg/s.
-
Filtro de gas: 2,08x10-8 kg/s.
-
Válvula automática de corte de presión: 1,04x10-8 kg/s.
Otra posibilidad que podríamos adoptar es considerar la válvula manual de corte de entrada de gas y obtener el valor global para los otros cinco elementos que constituyen el conjunto de la línea de quemador, es decir:
-
Válvula manual de corte (entrada conducción de gas): 2,08x10-8 kg/s.
-
Quemador: 3,64x10-8 kg/s.
Definición del grado y la disponibilidad
-
Ventilación (tipo): natural.
-
Grado: medio.
-
Disponibilidad: alta.
-
Ineficacia de la ventilación fv: 4 (este valor se obtiene de las tablas para ambientes cerrados con ventilación natural o con ventilación artificial general).
Tipo de zona peligrosa
Teniendo en cuenta la tabla 1 los escapes primarios con un grado de ventilación medio y disponibilidad alta, dan lugar a una zona 1.
Extensión de la zona
A partir del valor Qmín obtenido al sumar los valores mayores se aplica la expresión Ec. 1 considerando un factor de ventilación f igual a 4 y calculamos el volumen de la atmósfera explosiva Vz.
Vz=f·Qmín/Co (1).
Los valores obtenidos se muestran en la tabla 4.
Tabla 4. Resultados obtenidos para la sala de calderas considerando los elementos de la línea del quemador
Estos valores corresponden a la válvula manual de entrada y a una línea de una caldera. El circuito es simétrico y tendríamos los mismos valores para la otra línea del quemador ya que hay dos calderas. En vez de los cinco elementos independientes que componen la línea del quemador, podríamos calcular el escape para toda la línea del mismo cuya tasa de escape global es la que aparece en la tabla 5 junto con el resto de cálculos.
Tabla 5. Valores para la sala de claderas consinderando el quemador como un único elmento
En la tabla anterior podemos observar que el valor que obtenemos para el radio de la esfera considerando la línea del quemador en su conjunto, es inferior al valor obtenido considerando los elementos de la línea por separado. Por seguridad debemos tomar el valor obtenido en la tabla 5 de 0,43 metros que redondearíamos a 0,50 metros.
Al ser el metano un gas más ligero que el aire, adoptamos para las distancias verticales un valor doble que en el resto de las direcciones. Así, como resumen de la clasificación zonal tendríamos:
-
Zona 1: 0,5 metros alrededor de los dispositivos de corte, filtros y regulación, debiendo tomar 1 metro en las distancias verticales por encima de los dispositivos.
-
Zona 2: 0,5 metros alrededor de la zona 1 tomando 1 metro para las distancias verticales.
En las figuras 7 y 8 se representan de forma gráfica la disposición de las zonas de clasificación ATEX en los elementos estudiados.
Fig 7. Clasificación ATEX válvula de corte manual sala de calderas
Como medida preventiva adicional es aconsejable el definir como zona 2 todo el volumen rodeando la caldera. En esta decisión también debemos tener en consideración las posibles fuentes de ignición que nos podamos encontrar en las zonas de estudio.
Fig 8. Clasificación ATEX de la línea del quemador de una de las calderas
Aplicación de la metodología CFD a la sala de calderas
La instalación es un recinto cerrado de dimensiones 9,3m x 13,2m con una altura máxima de 7 metros en su parte más alta y de 4 metros en la parte baja. Presenta ventilación natural a través de dos rejillas que se ubican una en la puerta de entrada y otra en la puerta que comunica con una almacén donde se encuentra la zona de frío de la fábrica. La superficie de ventilación es de 1m x 0,45m = 0,45 m2, el caudal de ventilación para una velocidad medida con un termohigrómetro kestrel k3000 de 1 m/s es de 0,45 m3/s.
Consideramos un escape múltiple cuyo origen viene dado por cinco fugas. Una de ellas en un poro de 1 mm2 y las otras cuatro (correspondientes a las líneas de ambos quemadores) de 2,5mm2 cada una. El hecho de tomar esta medida de escape no es al azar, sino que viene motivada por datos bibliográficos recogidos en el manual práctico de Clasificación de zonas en atmósferas explosivas -CETIB, de autores Frances Escuer Ibars y Javier García Torrent-. Como ya hemos indicado uno de los poros corresponde a la válvula de entrada principal ubicada en el recinto (véase fig 4) y los otros cuatro se reparten dos por cada línea de los quemadores de las calderas 1 y 2. Así, en la válvula principal consideramos un escape de 1mm2 y en cada línea de los quemadores tendríamos dos fugas una en la válvula reguladora de presión y otra en la válvula automática ambas de 2,5mm2.
Consideramos por simplificación la geometría en dos dimensiones (en planta), valorando la extensión horizontal de los escapes de gas (metano) a través los elementos anteriores. Así, podremos comparar con la metodología propuesta según la norma UNE 60079-10-1.
En la figura siguiente (figura 9) se muestra el mallado realizado de la sala de calderas con las condiciones de contorno impuestas.
Fig 9. Mallado de la sala de calderas y puntos de escape
Resultados de la simulación para los escapes y discusión
Los resultados de la simulación se muestran en las Figs. 10-12. La Fig. 10 muestra los contornos de fracción másica de metano en los instantes iniciales de la simulación en el primer intervalo temporal. Como es lógico las mayores concentraciones de metano se producen en las inmediaciones la fuente de escape disminuyendo a medida que nos alejamos del elemento de emisión. De forma análoga la Fig. 11 presenta los contornos de metano alrededor de las fuentes de escape de las dos líneas de quemador de ambas calderas. Teniendo en cuenta las dimensiones de las calderas y los anchos de los pasillos, podemos obtener las distancias horizontales alcanzadas por los escapes de gas que oscilan entre los 1,1, y 1, 2 metros alrededor de las fugas.
Fig 10. Escape de gas metano (CH4) en válvula principal
Fig 11. Escape de gas metano (CH4) en los elementos de la línea del quemador y su extensión
Fig 12. Contornos de velocidad m/s en los escapes de gas metano (CH4)
La simulación de la Fig. 12 muestra los contornos de velocidad de escape de gas en el recinto en planta de la sala de calderas. Puede apreciarse como los mayores valores de velocidad se obtienen en las zonas de emisión disminuyendo a medida que nos alejamos de la fuente de escape. En estas zonas se producen los vórtices del flujo en forma de remolinos. También se puede observar como el gas tiende a “escapar” por la puerta principal de la sala de calderas donde se encuentra el enrejillado.
En esta simulación se utilizó una aproximación a primer orden con 300 iteraciones y considerando las condiciones de contorno de velocidad de escape y caudal de ventilación. Se puede observar como la el flujo se va distribuyendo a lo largo de toda la sala en diferentes concentraciones. Escalando la figura y tomando como referencia las dimensiones de la sala y de las calderas (6,60 metros de largo por 2,30 metros de diámetro) podemos determinar por ejemplo, los valores en metros de los chorros principales de los escapes de los poros de la línea de quemador y de la válvula principal. Como se puede observar en la Fig. 12 los poros de la línea del quemador alcanzan una distancia de 1,20 metros que es el ancho del pasillo (distancia de la caldera al muro izquierdo). Para la válvula de entrada principal se obtiene una distancia del chorro de 1,1 metros. No obstante, el gas se extiende por prácticamente todo el recinto de la sala.
Comparando los resultados obtenidos mediante la aplicación de las dos metodologías propuestas a los casos de estudio, podemos observar como la metodología basada en la norma UNE 60079-10-1 presenta valores menos restrictivos con distancias horizontales de 0,5 metros alrededor de cada uno de los elementos de escape, existiendo solapamientos de las geometrías de las esferas en los puntos de fuga. Por ser el metano un gas más ligero que el aire las distancias verticales se consideran el doble de las distancias horizontales, es decir, 1 metro.
Por otra parte, la metodología basada en la dinámica de fluidos computacional (CFD) mediante el uso del programa FLUENT arroja resultados más conservadores, se obtienen distancias horizontales de los escapes de metano del orden de 1,1 y 1,2 metros (distribuyéndose por prácticamente todo el recinto de la sala de calderas). Podemos en este caso también considerar que las distancias verticales son el doble de las horizontales, es decir, del orden de 2,2 –2,4 metros.
Se han presentado en este trabajo dos metodologías para la determinación de la clasificación y extensión de zonas por atmósferas explosivas por gases, vapores o nieblas. La primera de ellas es una metodología analítica basada en las recomendaciones de la norma UNE 60079-10-1 que persigue determinar el volumen de atmósfera explosiva alrededor de las fuentes de emisión. La segunda metodología es la CFD que aplica las ecuaciones de Navier-Stokes a la solución del flujo de fluidos, para ello se ha hecho uso del software comercial FLUENT.
La discrepancia de los resultados obtenidos viene marcada primeramente por las propias características de los dos métodos. La metodología analítica es una metodología aproximada condicionada por muchos factores como son las propias tasas de escape. Es necesario el recurrir a bibliografía para obtener datos de fuga de elementos y equipos habituales y no siempre existen datos de todos ellos ni éstos se presentan para todas las condiciones de temperatura y presión. Presenta también el inconveniente de los múltiples cálculos a realizar si se aplica a numerosas fuentes de fuga, lo que puede incurrir en errores a la hora de valorar la totalidad de las tasas de escape.
La metodología CFD es más real y más conservadora, permite estudiar de forma más real los casos de estudio e incorporar fenómenos de turbulencia, barreras, diversas condiciones iniciales y de contorno, etc.
Los autores quieren expresar su agradecimiento a la empresa EUROSERUM IBÉRICA, S.L.
Arntzen, B.J. (1998). Modelling of turbulence and combustion for simulation of gas explosions in complex geometries. Thesis. Division of applied mechanics, thermodynamics and fluid dynamics, The Norwegian University of Science and Technology, NTNU, Trondheim, Noruega.
ATEX 1999/92/EC (1999). Directive 1999/92/EC (Atex 137) on minimum requirements for improving the safety and health protection of workers potentially at risk from explosive atmospheres
Barrero, A. y Pérez-Saborid M. (2005). Fundamentos y aplicaciones de la mecánica de fluidos. McGraw-Hill/Interamericana de España, Madrid.
Bjerketvedt, D., Bakke, J.R. y Wingerden, K. van (1997). Gas Explosion Handbook. Journal of Hazardous Materials 52, pp.1-150.
Boussinesq, J. (1868). Mémoire sur l’influence des frottements dans les mouvements réguliers des fluids. J. Math Oures Appl. 13, p. 377.
Bray, K.N.C. (1990). Studies of the turbulent burning velocity. Proceedings of the Royal Society of London A, 431, pp. 315-335.
Bosch, R (2006). Metodología de análisis sobre la protección de los riesgos derivados de atmósferas explosivas. Caso Práctico. Proyecto. ETSIIB (UPC)
FLUENT 6.3.(2007). Tutorial Notes. ANSYS
Früchtel, G., Hassel, E.P. y Janicka, J. (1996). Turbulent length scales in a swirling flame. Twenty-Sixth Symposium (International) on Combustion, pp. 195-202.
GAMBIT 2.3. (2007). Tutorial Notes. ANSYS
García, J. (2003a). El fenómeno de la explosión. En: J. García Torrent (Editor), Seguridad industrial en atmósferas explosivas. Laboratorio Oficial J.M. Madariaga, Madrid.
Hansen, O.R., Storvik, I., Wingerden, K. van (1999). Validation of CFD-models for gas explosions, where FLACS is used as example; model description and experiences and recommendations for model evaluation. Proceedings European Meeting on Chemical Industry and Environment III, pp. 365-382, Polonia.
Hartmann, I., Nagy, J. y Brown, H.R. (1943). Inflammability and explosibility of metal powders. Report Inv. 3722, U.S. Bureau of Mines.
Hjertager, B.H. (1984). Influence of turbulence on gas explosions. Journal of Hazardous Materials 9, pp. 315-346.
Hjertager, B.H. (1986). Three-dimensional modeling of flow, heat transfer and combustion. En: Handbook of heat and mass transfer. Houston, Gulf Publishing Company, pp. 1303-1350.
Hjertager, B. H., Fuhre, K., y Bjoerkhaug, M. (1988). Gas explosion experiments in 1:33 and 1:5 scale offshore separator and compressor modules using stoichiometric homogeneous fuel/air mixtures. Journal of Loss Prevention in the Process Industries, 1, pp. 197-220.
Hjertager, B.H. (1993). Computer modelling of turbulent gas explosions in complex 2D and 3D geometries. Journal of Hazardous Materials, 34, pp. 173-197.
Ledin, H. S. (2002). A review of the state-of-the-art in gas explosion modelling. Report HSL/2002/02. Fire and Explosion Group. Health & Safety Laboratory, Harpur Hill, Buxton.
Martín, J (2005). Clasificación y análisis de los métodos disponibles para la aplicación de la directiva ATEX. Proyecto ETSIIB (UPC).
Patankar, S.V. (1980). Numerical Heat Transfer and Fluid Flow. Taylor & Francis.
Popat, N.R., Catlin, C.A., Arntzen, B.J., Lindstedt, R.P., Hjertager, B.H., Solberg, T., et al. (1996). Investigation to improve the accuracy of computational fluid dynamic based explosion models. Journal of Hazardous Materials, 45, pp. 1-25.
Pritchard, D. K. (1989). A review of methods for predicting blast damage from vapour cloud explosions. Journal of Loss Prevention in the Process Industries, vol. 2, pp. 187-193.
Real Decreto 681/2003. Protección de la salud y seguridad de los trabajadores expuestos a los riesgos derivados de la presencia de atmósferas explosivas en el lugar de trabajo.
Rose, M., Roth, P., Frolov, S.M. y Neuhaus, M.G. (1999). Modelling of turbulent gas/particle combustion by a Lagrangian PDF method. Comb. Sci. Tech., 149, pp. 95-113.
Strehlow, R.A. y Baker, W.E. (1976). The characterization and evaluation of accidental explosions. Prog. Energy Combust. Sci., Vol. 2, pp. 27-60.
Tu, J., Yeoh, G.J. y Liu, Ch. (2008). Computational Fluid Dynamics. A practical approach. Butterworth-Heinemann, Burlington, MA, USA.
UNE-EN 60079-10-1(2009). Clasificación de emplazamientos Atmósferas explosivas gaseosas. AENOR, Madrid.