Santamaría Martín, Ángel
Laboratorio Oficial J. M. Madariaga / Universidad Politécnica de Madrid / C/ Alenza, 1 / 28003 Madrid, España
+34 91 366 64 69 / asantamaria@lom.upm.es Martínez Díaz, Carlos
Laboratorio Oficial J. M. Madariaga / Universidad Politécnica de Madrid / C/ Alenza, 1 / 28003 Madrid, España
+34 91 366 64 69 / carlos.martinezd@upm.es
ABSTRACT
ABSTRACT
Durante el 2005, el Laboratorio Oficial Madariaga realizó un proyecto cuyos objetivos fueron analizar la viabilidad técnica de una inspección de maquinaria móvil utilizada en explotaciones mineras y desarrollar procedimientos operativos adecuados. Esta inspección debía realizarse en las propias explotaciones y con un tiempo de parada mínimo.
A raíz de los resultados obtenidos, en el 2006 se puso en marcha una campaña de inspecciones con el fin de perfeccionar los procedimientos ya desarrollados y elaborar unos criterios de aceptación objetivos.
Estos trabajos han tenido continuidad en el pasado año, habiéndose inspeccionado un número significativo de máquinas en varias Comunidades Autónomas.
Palabras clave
Palabras clave
Seguridad, maquinaria móvil, verificación
INTRODUCCIÓN
INTRODUCCIÓN
Los resultados obtenidos en determinados trabajos desarrollados por el Laboratorio Oficial J. M. Madariaga (LOM) de la Universidad Politécnica de Madrid, sobre verificación, asesoramiento y asistencia técnica de materia de prevención de riesgos laborales en explotaciones mineras, y los análisis de los índices de siniestralidad en el sector, han puesto de manifiesto las debilidades existentes en relación al cumplimiento de la normativa aplicable a los equipos de trabajo puestos a disposición de los trabajadores en la industria extractiva, y en particular a las máquinas de movimiento de tierras.
Durante el año 2005 el LOM, en base a un Convenio Específico de Colaboración con la Dirección General de Política Energética y Minas (DGPEM) del Ministerio de Industria, Turismo y Comercio, llevó a cabo el proyecto titulado “Verificación de los requisitos reglamentarios aplicables a máquinas móviles en uso en explotaciones mineras mediante una unidad móvil”, cuyo objetivo consistió en desarrollar y analizar la viabilidad de la inspección sistemática de la maquinaria móvil existente en las explotaciones mineras, en base a lo establecido en el Real Decreto 1215/1997, mediante una unidad móvil de verificación, que permita verificar que las máquinas móviles en uso en explotaciones mineras siguenmanteniendo las condiciones básicas de seguridad es decir, comprobar si el mantenimiento que se ha llevado a cabo en la maquinaria de movimiento de tierras ha sido el adecuado como para garantizar que se siguen cumpliendo los requisitos del Real Decreto 1215/1997, de obligado cumplimiento.
Las premisas establecidas fueron que esta inspección se pudiera realizar sin desplazamiento de las máquinas fuera de su lugar de trabajo y que el tiempo de parada fuera mínimo.
Para la definición de los parámetros o puntos susceptibles de verificación in situ en este tipo de maquinaria, así como los procedimientos necesarios para llevar a cabo dicha verificación y criterios de aceptación y rechazo, ha participado un grupo de trabajo constituido por servicios técnicos oficiales representativos de este tipo de maquinaria, empresas mineras y centros de formación sobre utilización y mantenimiento: Caterpillar, Volvo, Liebherr, Komatsu, Encasur y la Fundación Santa Bárbara.
DESARROLLO DEL PROYECTO
Con objeto de poner en marcha los procedimientos de verificación de maquinaria de movimiento de tierras desarrollados, durante el año 2007 el LOM llevó a cabo, en base a Convenio Específico de Colaboración con la DGPEM, una campaña de verificación de las condiciones básicas de seguridad de máquinas móviles de movimiento de tierras (excavadoras hidráulicas, palas cargadoras, volquetes de bastidor rígido, volquetes de bastidor articulado y tractores de cadenas –bulldozers-) existentes en determinadas explotaciones mineras a cielo abierto, según lo establecido en el Real Decreto 1215/1997.
Para la consecución de los objetivos planteados en el convenio, se realizaron las siguientes tareas:
• Selección y visitas a las explotaciones mineras donde se efectuaría la verificación in situ de la maquinaria minera.
• Selección de la maquinaria a verificar.
• Evaluación de resultados obtenidos y entrega de informe con propuestas de mejora en los aspectos relacionados con la seguridad, para cada una de las máquinas verificadas.
• Definición de listas de chequeo y análisis de resultados de lacampaña de verificación de maquinaria.• Análisis de peligros y parámetros o puntos de verificación de la nueva maquinaria que se incorpora al estudio de viabilidad. Elaboración de listas de chequeo para realizar la verificación in situ y realización de inspecciones piloto.
MAQUINARIA INCLUIDA EN EL PLAN DE VERIFICACIÓN
Debido a la variedad de tipos de máquinas existentes, inicialmente se seleccionaron aquellas que presentaran un alto índice de siniestralidad y que fueran representativas del sector, con el objetivo de realizar un estudio de viabilidad lo más detallado posible de forma que, posteriormente, fueran de fácil extrapolación los resultados obtenidos a otros tipos de máquinas. Las máquinas seleccionadas fueron las excavadoras hidráulicas de cadenas, los volquetes y las palas cargadoras sobre ruedas. Posteriormente, en el año 2006, se amplió el estudio de viabilidad con la incorporación de dos nuevas máquinas: los tractores de cadenas y las moto traíllas. En la Ilustración 1 se muestran las máquinas que actualmente estánincluidas en el plan de verificación:
Ilustración 1. Máquinas incluidas en el Plan de Verificación.
MAQUINARIA VERIFICADA DURANTE LA CAMPAÑA 2007
Durante esta campaña, se verificaron un total de 138 máquinas: 61 palas cargadoras, 26 volquetes de bastidor rígido, 18 volquetes de bastidor articulado, 5 tractores de cadenas y 28 excavadoras hidráulicas, pertenecientes a 33 explotaciones de 5 Comunidades Autónomas. En las Ilustraciones 2 a 5 se muestran algunos momentos del procedimiento de verificación in situ llevado a cabo.
Ilustración 2. Ensayo de frenado de servicio con tren de cadenas elevado. Comba de la cadena.
Ilustración 3. Ensayo de frenado de rotación de la superestructura, en pendiente y con carga.
Ilustración 4. Ensayo de frenado de rotación sin carga.
Ilustración 5. Medición de emisiones gaseosas.
ASPECTOS A VERIFICAR
Los parámetros o puntos verificados, y que afectan a la seguridad de las máquinas, se pueden englobar en alguno de los siguientes sistemas:
• Documentación• Chasis• Tren de rodaje• Motor• Tren de impulsión• Sistemas hidráulicos• Sistemas neumáticos• Estructuras de protección• Accesos a cabina y puntos de mantenimiento• Cabina del operador• Implemento de trabajo• Resguardos• Protección contra incendios• Indicadores de advertencia y de peligro• Circuito eléctrico• Iluminación• Avisadores acústicos
Esta agrupación ha sido determinada a partir de las características de seguridad, constructivas y funcionales de cada una de las máquinas. En las Ilustraciones 6 y 7 se pueden observar estas agrupaciones, donde también se señala el número de parámetros o puntos evaluados en cada uno de estos sistemas.
Ilustración 6. Agrupación de los parámetros o puntos de verificación (I).
Ilustración 7. Agrupación de los parámetros o puntos de verificación (II).
CLASIFICACIÓN DE LOS DEFECTOS
Una de las propuestas del LOM ha sido el método para evaluar los defectos encontrados en cada uno de los parámetros o puntos verificados. Estos defectos se han clasificado, en función de la probabilidad de aparición del peligro (o peligros) asociado y a la gravedad de las consecuencias que pudieran originarse, en defectos menores, mayores o graves.
Implican riesgo elevado para la seguridad y salud de las personas
Afectan a la seguridad de las personas, pero no suponen un riesgo inminente o grave
Defectos graves/críticos
Defectos mayores/moderados
No afectan a la seguridad y a la salud de las personas de forma inmediata Mínimas consecuencias
Defectos menores/leves
![]() |
Sin defecto Ilustración 8. Clasificación de los defectos encontrados. |
Para poder evaluar la clase de defecto que presenta cada uno de los parámetros o puntos a verificar, se recurrió a la experiencia y conocimiento de fabricantes y usuarios, así como al estudio de los resultados obtenidos en las visitasrealizadas a las distintas explotaciones, dando lugar al establecimiento de los criterios de aceptación y rechazo para cada uno de estos parámetros o puntos a verificar.
RESULTADOS GENERALES
La distribución de defectos encontrados en los sistemas de las máquinas evaluadas durante la campaña 2007 se refleja en la Ilustración 9, donde se puede observar que el mayor porcentaje de defectos están relacionados con el ruido y las vibraciones en cabina, los dispositivos de iluminación e indicación, los sistemas de protección contra incendios y los sistemas de dirección, principalmente:
0% 10% 20% 30% 40% 50% 60% 70% 80% 90% 100%
![]() |
Documentación Chasis Tren de rodaje2,9%8,0%31,2% |
5,8%
Dirección Sistemas de frenado Compartimento motor
Sistemas Hidráulicos/neumáticos21,0%
14,5%
0,7%
0,7%2,9%
2,9%7,2%
0,7%
Estructuras de Protección
Elementos de acceso Puesto del operador Trabas de seguridad Implemento de trabajo
Resguardos Indicadores de advertencia y de peligro4,3%
0,7%
3,6%
8,0%
0,7%
5,1%0,7%
1,4%
5,1%
24,6%
1,4%
Protección contra incendios
Sistema eléctrico16,7%
1,4%11,6%0,7%
Avisadores acústicos Dispositivos de iluminación e indicación Ruido Operador /Vibraciones CE
3,6% 6,5%
10,9%2,9%
28,3%
71,9%
5,8%
20,2%
Gases de escape16,7%
2,6%
6,1%
Menor Mayor Crítico
![]() |
Ilustración 9. Defectos encontrados en los sistemas de las máquinas verificadas. |
RESULTADO DE LAS PRUEBAS DE FRENADO
Como ejemplo de los ensayos realizados sobre los sistemas de frenado, en la Ilustración 10 se muestran los resultados obtenidos sobre el freno de servicio de las palas cargadoras, máquinas que han presentado unos resultados aceptables en este apartado:
60,00%
![]() |
20 km/h35 km/h |
50,00%
![]() |
40,00%30,00%20,00%10,00% |
0,00%
![]() |
Ilustración 10. Eficacia del freno de servicio en palas cargadoras. |
RUIDO, VIBRACIONES Y GASES DE ESCAPE
En relación a resultados sobre el ruido en cabina, en la Ilustración 11, se puede observar como un alto porcentaje de máquinas superan los niveles de 80 y 85 dB(A):
95
![]() |
90 |
85
![]() |
807570 |
134 140 157 164 164 183 193 193 199 203 210 221 224 224 228 235 240 240 259 259 287 302 309 313 313 313 320 325 354 354 354 357 366 373 485 485 522 533 533 544 567 567 597 699 735
Potencia de la máquina (kW)
Ilustración 11. Ruido en cabina.
En el caso de las vibraciones de cuerpo completo transmitidas al operador, el número de máquinas que superan los niveles de 0,5 y 1,15 ms-2 son aún mayores, como se refleja en la Ilustración 12:
9,00
![]() |
8,007,00 |
6,00
![]() |
5,004,003,002,001,000,00 Año de fabricación Ilustración 12. Vibraciones de cuerpo completo. |
Para terminar este apartado, en la Ilustración 13 se muestran los resultados referentes a las emisiones contaminantes, en concreto los niveles de Opacidad de los humos de los motores de las máquinas:
6,50
![]() |
6,005,505,00 |
4,50
![]() |
4,003,503,002,502,001,501,000,50 |
0,00
![]() |
Año de fabricación Ilustración 13. Opacidad de los humos. |
NIVEL DE SEGURIDAD DE LAS MÁQUINAS
Finalmente, para cada uno de los sistemas verificados, se estableció su importancia relativa en relación a la seguridad de la máquina que, junto a la clasificación de los defectos encontrados, sirvió para evaluar el estado de seguridad de cada una de las máquinas verificadas. De esta forma, se puede hablar del nivel de seguridad que presenta cada máquina, que podrá ser uno de estos cuatro (Ilustración 14):
Ilustración 14. Nivel de seguridad de las máquinas.
• Sin defectos o favorable.
• Favorable, pero necesita una nueva verificación a medio plazo.
• Desfavorable, y que es necesaria una nueva verificación a corto plazo.
• Desfavorable o negativo, que implica la necesidad de parar lamáquina hasta la subsanación de los defectos encontrados.
En base a lo anterior, para las 138 máquinas evaluadas se obtuvieron los siguientes resultados (Ilustración 15), clasificados según su antigüedad:
62
45%2619%
32%
4734%
Favorable Favorable con revisión Desfavorable con revisión Negativo
![]() |
70%60%50%54%49%60% 62%40%30%20%40% 30% 29% |
19%
33%
38%
30%
23%
15%
10% 6%
0%0%
10%
2%0% 0% 0%2004-2007 (Nuevas) 2000-2003 (Seminuevas) 1995-1999 1990-1994 < 1990 (Antiguas)
![]() |
Ilustración 15. Resultados obtenidos en las máquinas evaluadas. |
CONCLUSIONES
Las principales conclusiones que se han extraído de la realización de este proyecto son las siguientes:
• Se ha demostrado que técnicamente es viable la creación de una unidad móvil que permita verificar in situ que las máquinas móviles en uso en explotaciones mineras siguen manteniendo las condiciones básicas de seguridad y salud para los trabajadores.
• Se han desarrollado los procedimientos operativos que permitenrealizar de forma sistemática dichas verificaciones.• Se han fijado criterios objetivos de aceptación y rechazo para los tipos de máquinas incluidas en el plan de verificación.• Tanto los procedimientos operativos como los criterios de aceptación y rechazo, pueden ser fácilmente extrapolables a otros tipos de máquinas.• El tiempo total de inspección depende de las condiciones de laexplotación y del modelo y tipo de máquina, estimándose entre 1 y 1½ horas.• En muchos casos los usuarios desconocen el estado de los sistemasde seguridad de las máquinas.• Altos niveles de ruido y vibraciones.
Papers relacionados
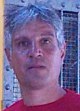

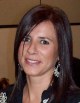
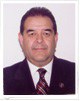
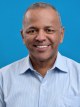
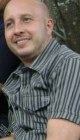