González Díaz, Rafael Eugenio
Departamento de Ingeniería de Organización, Administración de Empresas y Estadística / Universidad Politécnica de Madrid / Pza. Cardenal Cisneros, 3 / 28040 Madrid, España+34 1 3366618 / rafaeleugenio.gonzalez@upm.esAlonso Pérez, Jacinto JulioDepartamento de Ingeniería de Organización, Administración de Empresas y Estadística / Universidad Politécnica de Madrid / Pza. Cardenal Cisneros, 3 / 28040 Madrid, España+34 1 3367494 / jacintojulio.alonso@upm.es
Sánchez-Valero Catalá, Javier
Departamento de Tecnologías Especiales Aplicadas a la Aeronáutica / Universidad Politécnica de Madrid / Pza. Cardenal Cisneros, 3 / 28040 Madrid, España+34 1 3367492 / javier.sanchezvalero@upm.es
RESUMEN
RESUMEN
En este artículo se describen los materiales y procesos usados en el campo de los materiales compuestos haciendo una revisión sobre los riesgos laborales asociados a los procesos de producción de piezas con estos materiales y proponiendo una guía para la elaboración de cuestionarios en las empresas que permita evaluar los riesgos de los puestos de trabajo. El artículo se centra, fundamentalmente en el sector de los materiales compuestos avanzados.
Keywords
Keywords
Materiales compuestos, prevención de riesgos, cuestionario, guía
INTRODUCCIÓN
INTRODUCCIÓN
Un material compuesto es la combinación de dos o mas materiales, aportando, cada uno de ellos, por su contenido, forma, o disposición en que esté, distintas propiedades, lo que confiere al resultado, el material compuesto, unas propiedades mejores que la de cada uno individualmente.
La industria de los materiales compuestos en el mundo emplea tres tipos de formas de combinar los materiales:
• Materiales compuestos de matriz polimérica (PMC)• Materiales compuesto de matriz metálica (MMC)• Materiales compuestos de matriz cerámica (CMC)
El primer tipo es el más usado desde hace unos 30 años teniendo su mayor aplicación en el campo de la construcción de aviones y en menor medida en automoción, barcos y en bienes de consumo[1].
El segundo grupo está en su fase inicial de aplicación utilizándose únicamente en sectores donde se precisan altas características mecánicas.
El tercer grupo dista todavía un tiempo de su consolidación a nivel de mercado, utilizándose únicamente en algunas aplicaciones donde mantener la resistencia mecánica a altas temperaturas es prioritaria.
España es un líder en Europa en la producción de distintas piezas o conjuntode piezas en el sector aeronáutico, empleándose un número elevado de trabajadores especializados en procesos convencionales y en nuevos procesos automatizados[2].
En este artículo nos concentraremos en el material compuesto mas usado en los distintos sectores industriales, como son los PMCs, y analizaremos su repercusión sobre la prevención de los riesgos laborales que pueden entrañar su uso.
LOS MATERIALES COMPUESTOS DE MATRIZ POLIMÉRICA
Hay tres sectores que emplean los materiales compuesto de matriz polimérica: aeronáutica y espacio, automoción y naval, y bienes de consumo (especialmente las gamas blanca y marrón).
Los más utilizados son los que emplean como matriz el poliéster insaturado(UP) y la fibra de vidrio en distintas formas. Las propiedades que se obtienen son medias, recibiendo este grupo de materiales el nombre de plásticos reforzados.
En aeronáutica y espacio, y en parte en automoción, se emplea, entre otras, lasresinas epoxi y la fibra de carbono, en forma de cinta o tejida. Se considera que por las características obtenidas y los materiales y procesos empleados, que estos se denominen materiales compuestos avanzados.
La industria de los distintos bienes de consumo industrial utiliza los materialescompuestos de una forma distinta. Emplean SMC y DMC, siglas que identifican una mezclas de resina, generalmente poliéster, fibras cortas orientadas al azar y aditivos. Los primeros son en forma de lámina y los segundos en forma de bloque. Se emplean para producir tapas, carcasas, y armazones de la mayor parte de los electrodomésticos.
Las resinas
Desde el punto de vista químico los plásticos utilizados como resinas en materiales compuestos se pueden clasificar en: termoplásticos y termoendurecibles. Éstos últimos son los más utilizados, estando entre ellos los ya mencionados, epoxi y poliéster, y poliuretano, fenólicos, bismaleimidas y poliamidas.
Las resinas epoxi se obtienen con distintas formulaciones, que solo saben sus fabricantes, pero generalmente parten de epiclorhidrina y bisfenol-A. Un tercer componente son los compuestos de bifenilo. Estas resinas pasan por distintas etapas hasta que endurecen (curado). Son líquidas, con más o menos viscosidad dependiendo de su Mw en la etapa A, en la etapa B son sólidos viscosos y en la C están endurecidas. Los preimpregnados se suministran con la resina en etapa B, que es como a la mitad de su reacción, su peso molecular es muy alto y por tanto pocos vapores pueden desprenderse al ambiente. En cambio, en los procesos en húmedo, cuando hay que impregnar las fibras con la resina, ésta necesita estar muy líquida empleándose en una etapa cercana a la A, en cuyo caso se pueden desprender vapores en el ambiente.
Otras sustancias presentes son los agentes de curado como son las diaminas. Suele emplearse MDA metilen dianilina y DDS que es una dianilina sulfurada[3]. Al igual que la resina tienen alto peso molecular y solo pueden ser problemáticas en procesos en húmedo
Las fibras
Las más usadas son las de vidrio, pero las de carbono/grafito han tenido un gran crecimiento debido a las altas prestaciones que confieren al material. En menor mediad también se emplean fibras de aramida y otras en menor proporción.
Se pueden utilizar en distintas formas:
• Fibras cortas o largas( individuales o en roving(cuerda)• Fibras tejidas, en muy distintas formas, o sin tejer(cinta)• Fibra corta prensada para hacer fieltros
Otras sustancias presentes en el material o en el proceso
Para hacer preimpregnados se utilizan las fibras largas tejidas o en cinta, mientras que procesos como el bobinado de filamentos y la pultrusión utilizan fibras en mazos o en rovings. Otros procesos como los moldeos por inyección incorporan fibra corta en un proceso llamado RRIM (reinforced reaction inyection moulding).
Por moldeo por compresión se obtienen piezas a partir de SMC o DMC, antes mencionados.
Los disolventes pueden aparecer como propia formulación de las resinas,especialmente en el método húmedo, pero también pueden ser parte del proceso y se usan para la limpieza de los moldes. Lo más frecuente es encontrarlos en los dos últimos casos. Los más usados son las cetonas, alcoholes, y los hidrocarburos clorados. Las formulaciones que se emplean atienden mas a no perjudicar al material que a otros aspectos, por lo que debe, como en todos casos, revisarse la MSDS (material safety data sheet) de la sustancia que estemos empleando y revisemos sus componentes para observar si existe una posible toxicidad.
Los procesos con materiales compuestos
No nos referimos en este artículo a los procesos de fabricación de piezas de material compuesto y no al proceso de obtención de los materiales compuestos.
Los procesos principales son los siguientes[4]:
- 1. Preimpregnado manual y curado en bolsa de vacío
- 2. Moldeo en autoclave: a. Con apilamiento manual de las capas preimpregnadas b. Con máquinas de apilamiento automático del preimpregnado
- 3. Bobinado de filamento en húmedo
- 4. Pultrusión
- 5. Moldeo por transferencia de resina
- 6. Moldeo por inyección Los procesos de mecanizado y acabado incluyen los siguientes:
- 1. Mecanizado a alta velocidad con fresadoras
- 2. Recanteado
- 3. Taladrado
- 4. Avellanado
- 5. Remachado y encolado
A estas tareas hay que añadir otra tarea que resulta muchas veces frecuente durante los procesos de producción. Se trata de las reparaciones de piezas que salen con defectos, pero según normas de reparaciones en producción hay defectos que pueden repararse y devolver la pieza a su estado normal de calidad. La justificación de estos procedimientos viene determinada por el elevado coste de las piezas de material compuesto.
De igual forma durante las operaciones de mantenimiento de coches, barcos y aviones se reparan los daños sufridos durante su funcionamiento, siendo los procedimientos de reparación semejantes a los que se realizan a las piezas defectuosas en el proceso de producción. Las tareas implicadas en este caso requieren eliminar las pinturas, eliminar la zona dañada, lijar los bordes y poner un parche[5].
Haremos referencia a estos procesos desde el punto de vista de las tareasque realiza el personal que está en contacto con los materiales compuestos.
TAREAS QUE DESEMPEÑAN LOS TRABAJADORES DE UNA EMPRESA DE MATERIAL COMPUESTO AVANZADO
Podemos distinguir entre dos casos, cuando el proceso de creación del apilamiento se hace manualmente y cuando se hace, con la ayuda de máquinas, de forma automática:
A) Proceso Manual para fabricación de kits:
• Manipulación de la materia prima extraída de los arcones frigoríficos, consiste en rollos de material preimpregnado envuelto en bolsas, rollos de adhesivo en forma de film envuelto en bolsas y latas de adhesivo y otros materiales• Corte de patrones en máquinas automáticas o manualmente• Elaboración manual de kits• Mecanizado de núcleos caso de llevar éstos la pieza
• Aplilamiento manual• Compactación mediante vacío, pudiendo ser en varias etapas en función del espesor de la pieza• Hay piezas que se rigidizan con núcleos de distintos materiales. Éstos deben quedar pegados a las capas por lo hay que introducir una capa de adhesivo en forma de película por encima y por debajo del núcleo.• Preparación del utillaje y molde, limpieza y aplicación de desmoldeante y/otejido desmoldeante• Colocación de capas. Actualmente los procesos con materiales compuestos avanzados emplean la ayuda de un laser para posicionar las capas• Colocación de termopares, masilla sellante y otros materiales auxiliares• Colocación de la manta de tejido de vidrio como respirador y cierre con la bolsa de vacío. Antes de cerrar la bolsa se pueden colocar placas metálicas, llamadas “pisas” que sirven para dejar la zona que cubren mas lisa.
B) Proceso automático:
Se pueden emplear dos tipos de máquinas:
• a m a ñ o
![]() |
lt Figuras 1 y 2. Mesa de ATL y cabezal y Sistema de alimentación de cinta (Cortesía MAG Cincinnati) Figura 3. Detalle del cabezal (Cortesía de MAG Cincinnati)el tamaño de la mesa[2]. En la figura 1 podemos ver la mesa con parte del material ya puesto (brillo) y el cabezal de aplicación de la cinta (podemos ver en detalle en la figura 3). En la figura 2 se aprecian los rollos de materia prima en distintos carretes que constituye el sistema de alimentación.• En Segundo lugar tenemos las máquinas de Fiber Placement (encintado). Se utilizan para hacer grandes piezas de poco espesor y con grandes curvaturas. En la figura podemos ver el cabezal encintando una superficie curva. En la figura 4 observamos uncabezal poniendo la cinta sobre una superficie curva. Figura 4. Cabezal Viper Fiber Placement (Cortesía de MAG Cincinnati) |
En la figura 5 vemos el útil de una parte cilíndrica que se utilizará para encintar. Podemos observar las gradas de montaje necesarias y los apoyos de los útiles. Los operarios mueven el útil con la ayuda de grúas.
![]() |
Figura 5. Preparación de máquina de encintado (Cortesía de Lockheed Martin) |
RIESGOS LABORALES POR EL CONTACTO CON LOS MATERIALES COMPUESTOS DURANTE EL PROCESO DE PRODUCCIÓN DE PIEZAS
Los riesgos que pueden ocurrir durante el proceso de producción se relacionan con las resinas, las fibras, agentes de curado, el polvo procedente de los procesos de mecanizado, desmoldeantes en forma de aerosoles y los disolventes que se utilizan para la limpieza.
Riesgos debidos a las resinas
Como ya vimos antes las resinas que se utilizan en los materiales compuestos tienen alto peso molecular por lo que no se han detectado problemas por vía aérea. No obstante vamos a particularizar en cada resina para ver sus efectos:
• Epoxi: algunas veces se han encontrado moléculas de epiclorhidrina debido aque el proceso de curado no alcanza el 100%. Es conveniente emplear los filtros adecuados en los autoclaves y revisar el contenido de los volátiles que se retenga. Si puede ser un problema, en cambio, el contacto con la piel, pudiéndose producir irritaciones que pueden llegar a dermatitis. Además se han producido casos de sensibilización con alguna de las sustancias lo que implica el inmediato cambio de puesto del trabajador[6].• Fenólicos: la reacción entre el alcohol fenólico y el formaldehido puede implicar presencia de ambos en el ambiente pudiéndose absorber por la piel. Son sustancias tóxicas por lo que se debe controlar el ambiente para evitar su presencia• Poliésteres: no se han detectado problemas durante su procesado.
Riesgos debidos a los agentes de curado
Los agentes de curado de las reinas epoxi como el MDA pueden ser tóxicos para el hígado y se ha comprobado que es una sustancia carcinógena en animales. El contacto con la piel puede provocar manchas que deben eliminarse rápidamente ya que se absorbe con facilidad. Hay que lavar con agua y jabón y no emplear detergentes. La OSHA determina unos límites de 10 ppb en jornadas de 8 horas y100 ppb en periodos menores de 15 minutos. Las aminas DDS en muy bajas concentraciones en el ambiente no han dado lugar a problemas.
Las toluenaminas pueden dar lugar a irritaciones de la piel, pero las aminas con grupos cíclicos presentan irritaciones de piel y ojos pudiendo llegar a irritar la garganta.
Existen otros agentes de curado que presentan menos efectos que los anteriores pero algunos de ellos producen sensibilización a la sustancia en algunos trabajadores.
Riesgos debidos a las fibras
Las mas empleadas son las fibras de vidrio, pero de igual forma, las fibras de carbono que pueden producir irritación por su contacto con la piel debido al carácter abrasivo, pudiendo llegar a irritar ojo y garganta. Las fibras de carbono que tienen como precursor (fibras de las que se obtiene) el poliacrilonitrilo PAN no han dado evidencias de ser sustancias que favorezcan la mutación de las células, Tanto las fibras de vidrio como las de carbono tienen un tamaño que no las hace respirables, aunque llevan un tratamiento superficial con resinas epoxi que da lugar a las reacciones irritantes. Las fibras de aramida no han dado resultado de riesgo alguno.
El problema puede surgir cuando se mecaniza cualquiera de las fibras ya quese pueden fracturar en pequeños filamentos que pueden dar lugar a problemas. Concentraciones típicas de filamentos son 0,2 f/ml en jornadas de 8 horas.[1]
Riesgos debidos al polvo
El polvo proviene de los distintos procesos de mecanizado para el acabado de las piezas, el mecanizado de núcleos, y el generado en las reparaciones de piezas con defectos de producción o dañadas. El tamaño de este polvo es lo que determina que pueda ser respirable o inhalable. Las operaciones que generan el polvo son:
• Fresado y rectificado final de las piezas• Recanteado, agujereado, taladrado y avellanado de la pieza• Lijado de las zonas con defectos o dañadas para realizar la reparación. En el caso de reparaciones hay que observar que el polvo de la pintura lijada puede contener elementos metálicos en su composición (aditivos de las pinturas).
La mayor parte de los residuos de polvo es una mezcla de fibras y resina curada.
Las fibras, por su tamaño solamente serían inhalables y es mas importante controlar la parte de los residuos de polvo que se transforma en filamentos de la fibra. Su tamaño es mucho menor y podría ser respirable. Los límites se encuentran en 2 filamentos por centímetro cúbico en periodos de 8 horas. En la figura 6 podemos una micrografía de una sección de una pieza de tejido de fibra de carbono y epoxi, pueden observarse en las secciones transversales de
las fibras que están compuestas por pequeñosfilamentos de tamaño mucho menor que la fibra.
Riesgos debidos a los disolventes
Figura 6. Micrografía a 400x pieza de tejido(elaboración propia)
A diferencia de las resinas los disolventes son mucho mas volátiles y algunos incluso inflamables. Los riesgos son debidos a irritaciones de la piel, de los ojos y a la absorción de algunos a través de la piel. Por otro lado algunos pueden provocar la sensibilización a sus componentes por lo que debe apartarse al trabajador de esas tareas. Debe comprobarse la MSDS para determinar que guantes y mascarilla deben ponerse los trabajadores. Entre los principales tipos de disolventes encontramos: MEK (metiletilcetona), DMK(acetona), MIBK (metilisobutilcetona). Pueden provocar irritaciones de la piel, garganta y ojos y en periodos prolongados dar síntomas de narcosis con dolores de cabeza, mareos y vómitos. También se usan alcohole: metilalcohol, etanol, e isopropanol. Producen menos intensidad enlos efectos que los anteriores pero con los mismos resultados. Debido al menor riesgo de inflamabilidad algunos fabricantes han introducido los compuestos clorados: diclorometano, tricloroetano, tricloroetileno. Producen efectos similares a los primeros pudiendo llegar a producir dermatitis. Finalmente también podemos encontrar en algunos casos otras sustancias como: tolueno, silanos, tetrahidrofurano, dimetilformaldehido, entre otros[7].
Puestos de Trabajo relacionados con la producción de piezas de material compuesto avanzado
Existen distintos puestos de trabajo que tienen una relación con posibles riesgos laborales. Hay casos que van desde un contacto esporádico hasta trabajadores que tienen un contacto diario. Podemos clasificarlos en:
- 1. Personal con tareas indirectamente asociadas a la producción: es un grupo amplío que va desde el personal del departamento de diseño hasta el personal del departamento de ingeniería de producción
- 2. Personal de preparación y montaje de kits de material compuesto. El personal implicado desempeña las siguientes tareas: extracción de la materia prima desde los arcones frigoríficos, corte manual o con maquinas automáticas de patronaje de los rollos para obtener las capas, montado manual de capas y preparación de kits para almacenar en el arcón o para producción. Esta última tarea puede acompañarse por otra denominada compactación que sirve para extraer el aire entre capas.
- 3. Personal de producción:
Hay que diferenciar entre procesos basados en el montaje manual y los basados en la automatización de procesos.
En el primer caso tenemos:
a. Con los kits preparados previamente las que continúan el proceso son las siguientes: preparación y ubicación del utillaje y molde y, encima del molde montar la bolsa de vacío. Esta última tarea se compone de la aplicación de desmoldeantes, y, según el caso, termopares, retenedores, pisas, válvula de vacío, masilla, mantas de fibra de vidrio como tejido respirador y la bolsa de vacío, y otros materiales auxiliares[8].
b. Otro personal dentro de este apartado es el personal que lleva elutillaje con el molde hasta el medio de calentamiento y presión que suele ser un autoclave. Las tareas suelen implicar el movimiento de grandes utillajes con la ayuda de grúas, la conexión del sistema de vacío y termopares. Este personal también realiza las tareas de control del proceso con la supervisión del personal de los departamentos de ingeniería de producción y de producción, la extracción de los utillajes con los moldes y las piezas ya curadas del autoclave, y el demoldeo de las piezas de los moldesc. Las piezas desmoldeadas tienes aristas, rebabas y no tienen ladimensión final ya que se proyectan con creces, para dar la dimensión final hay que recantear las piezas, y dependiendo del diseño, se terminarán agujeros, aberturas o otros mecanizados menores.d. Las piezas recanteadas se llevan al montaje final de subconjuntos, que pueden implicar aplicar adhesivos y remachado para la unión entre piezas y finalmente aplicar pintura.
En el segundo caso la aplicación de máquinas automatizadas implica una relación distinta del trabajador con el proceso de producción con material compuesto. Básicamente consiste en una robotización de algunos procesos, por tanto se deben incluir ciertas tareas distintas de los procesos habituales.
Al margen de la especialización por parte del trabajador para el correcto uso de las máquinas, las tareas implican el manejo de grúas para ubicar grandes moldes en las máquinas, posturas distintas, una gran atención a las tareas realizadas, y un contacto semejante al de montador de capas con la materia prima.
EJEMPLO DE CUESTIONARIO PARA LA EVALUACIÓN DEL PUESTO DE TRABAJO DESDE EL PUNTO DE VISTA DE PRL
A continuación se expone un método posible para preparar un cuestionario que evalúe los riesgos laborales y permita definir la posible prevención de éstos.
Hoja de información general de riesgos del puesto
Con objeto de establecer una estandarización en la definición de la prevención de riesgos laborales se presenta un cuestionario que pretende enfocar los distintos puestos que puede desempañar un trabajador de materiales compuestos
Identificación del trabajador/a• Numero RPT:• Nombre:
Identificación del puesto de trabajo• División/ Departamento/Fábrica:• BPO/ BPU (business process operation/business process unit):• Puesto de trabajo específico:• Puesto de trabajo genérico:
Descripción del puesto de trabajo:
• Describir las tareas que el trabajador desarrolla en el puesto de trabajo
Áreas específicas de análisis de riesgos laborales del puesto
Vamos a definir las características específicas del puesto de trabajo, introduciendo las variables de medida, con el objeto de poder evaluar cada puesto de trabajo. Las características a evaluar son las siguientes:
- 1. CONDICIONES DEL PUESTO DE TRABAJO a. CONFIGURACIÓN DEL PUESTO i. Espacio de trabajo: aspecto, dimensiones y visión ii. Iluminación: intensidad luminosa, luz natural iii. Vibraciones: manobrazo, cuerpo completo, intensidad b. CALIDAD AMBIENTAL i. Ventilación: calidad y renovación del aire ii. Temperatura: de 18 a 30C se considera normal iii. Estrés térmico: ciclos térmicos, intervalo de exposición iv. Ruido: Se permite estar sin protección a este nivel de ruido Hasta 8 horas 90 decibelios Hasta 4 horas 95 decibelios Hasta 1 hora 105 decibelios
- 2. CARGA DEL PUESTO DE TRABAJO a. CARGA FÍSICA i. Sentado ii. Agachado iii. Tumbado iv. Posición de pie trabajo ligero v. Posición de pie trabajo intenso vi. De pié con operaciones manuales en máquina/utillaje vii. De pie inclinado α < 30º viii. De pie inclinado α > 30º ix. Altura de brazos respecto a los hombros, cuerpo torsionado b. CARGA SÍQUICA i. Presión por el tiempo ii. Atención iii. Complejidad iv. Monotonía v. Iniciativa vi. Aislamiento vii. Horario de trabajo viii. Presión general
- 3. CONTAMINACIÓN POR AGENTES QUÍMICOS ESPECÍFICOS a. Contacto aéreo i. Vapores de preimpregnados ii. Vapores de Adhesivos iii. Vapores de disolventes iv. Polvo de recanteado, taladrado y mecanizado en general b. Contacto con la piel i. Con preimpregando ii. Con adhesivos iii. Con disolventes
- 4. CONDICIONES DE SEGURIDAD DEL PUESTO
a. Caída de personasb. Golpes con o por objetosc. Aprisionamiento o aplastamientod. Contactos térmicose. Contactos eléctricosf. Contactos con sustancias corrosivasg. Intoxicaciones agudash. Sobre-esfuerzosi. Incendios
Escalas de medida y sistema de puntuación
Tenemos distintas variables a valorar:
• Variables objetivas sujetas a normativas que establecen límites en su valoración
Ejemplo de Contaminantes químicos:
- Para valorar definimos tres variables: peligrosidad del contaminante, intensidad de la exposición y tiempo de exposición. En el caso de polvo de fibras hay que hacer referencia a la diferencia entre partículas inhalables y partículas respirables. La American Conference of Governmental Industrial Hygienist establece unos límites de exposición de 10mg/m3 para las primeras y 3 mg/m3 para las segundas. De acuerdo con estos valores podemos definir los intervalos para cada variable[9] y [10]: i. Peligrosidad: menos de 0,3, de 0,3 a 0,5, de 0,5 a 2 y mas de 2 f/cm3 ii. Intensidad: TLVSTEL, tiempo medio ponderado de exposición menor de 15 minutos, se considerará cara a la intensidad siempre mayor de 15 minutos iii. Tiempo de exposición: menos de 4 veces, 4 veces, o mas de 4 veces el TLVSTEL • Variables subjetivas que dependen mas de la variabilidad de los trabajadores Aunque existen estudios importantes como NIOSH, para cargas físicas las empresas pueden emplear también criterios estadísticos basados en ponderaciones de los valores posibles que puede adquirir la variable o por su frecuencia, siempre observando las normas vigentes en la materia. Ejemplo de Carga Física:
- Como el trabajador puede estar en distintas posturas a lo largo de la jornada de trabajo, dividimos el 100% del tiempo en percentiles del 10%. Construimos una lista con las distintas posturas que puede tener el trabajador. Con ambas hacemos una tabla en donde cada valor de la tabla será distinto en función de la postura y el tiempo que se mantiene en ella. Es aplicable tanto en actividad física estática como dinámica Ejemplo de variable de Seguridad:
- Medimos la frecuencia de la ocurrencia del hecho • Escala de 1 a 10 de Muy baja a Muy alta
- Medimos la probabilidad de que ocurra el hecho • Escala de 0,1 a 1 de puede ocurrir a se espera que ocurra
- Establecemos las consecuencias que puede tener
• De 1 a 10 de Leve a Muy Grave
Parece adecuado multiplicar las puntuaciones para obtener el valor final
RESULTADO
Una vez obtenidas las puntuaciones para cada grupo de variables se tomará, como resultado, el valor del grupo con mas alta puntuación, dado que cada grupo puede representar riesgo suficientemente grave.
MEDIDAS DE PREVENCION:
• Listar las medidas que se propongan poner en marcha para prevenir los riesgos descritos del puesto de trabajo.
• Detallar los medios de protección que debe utilizar el trabajador paraprevenir los riesgos del puesto de trabajo.• No debe olvidarse que todo los que suponga la información y concienciación de los trabajadores redundará en una mejor prevención de los riesgos, por tanto se deben hacer acciones formativas que expliquen el por qué[11].
APLICACIÓN A DISTINTOS PUESTOS DE TRABAJO
Vamos a aplicar de forma teórica las áreas generales y específicas definidas anteriormente a dos tipos de puesto de trabajo:
a. Montador de capas de preimpregnadob. Personal en trabajos de ensamble: encolado y remachado
Montador de capas de preimpregnado
Identificación del trabajador• División/ Departamento/Fábrica:• BPO/ BPU:• Puesto de trabajo específico: Montador de capas de piezas elementales• Puesto de trabajo genérico: MATERIALES COMPUESTOS
Descripción del puesto:
• Se realiza el posicionado o moldeado de materiales preimpregnados sobre los diferentes útiles para la fabricación de piezas de material compuesto.
Posibles riesgos asociados:
• Dinámicos:
- Cortes en manos con herramientas de corte manual y con el propio material.
- Golpes en pies por caída de objetos y herramientas o durante el movimiento de porta carros, carros o útiles. También pude quedar el trabajador atrapado bajo los elementos citados anteriormente
- Posturas difíciles para el trabajador que excedan sus límites físicos.
- Golpes o impactos en ojos de cuchillas y otros materiales durante el montado de capas.
- Proyecciones o rebotes en piel y ojos del adhesivo en espray. • Higiénicos:
- Contactos con la piel y con las vías respiratorias de los vapores de resinas y otros componentes de origen polimérico que forman la matriz del material compuesto o de otros materiales auxiliares; así como del adhesivo en forma de aerosol o en film. • Otros:
- Impactos accidentales de rayo laser en ojos
Medidas de prevención:
• Revisiones médicas anuales por riesgo dermatológico. Establecer un protocolo médico para casos especiales• Formación obligatoria para conocer y entender la materia prima que se emplea en materiales compuestos y sus procesos.• Formación específica para trabajadores en puestos específicos, por ejemploen el manejo, uso y en riesgos de los equipos de láser.• Evitar el contacto directo con los materiales utilizando los equipos de protección individual (guantes, gafas de protección y vestimenta adecuada como mono, calzas y gorros para el pelo). La ropa de trabajo debe tener mangas largas y ajustadas en puños.• Extremar la higiene personal: lavarse las manos en las pausas de trabajo y a la finalización del mismo.• Disponer de áreas bien ventiladas para aplicar el adhesivo, o cualquier otra sustancia en forma de aerosol.• Evitar el mantenimiento prolongado de cualquier postura forzada.• Asistir a los reconocimientos médicos voluntarios durante el año y obligatorios periódicos anuales.• Conocer las señales y significados de los procedimientos en caso de emergencia y evacuación para el desalojo del edificio.• Medio de contacto para emergencias del protocolo médico
Detalle particular de medios de protección:
• Guantes de caucho o algodón y una capa de crema barrera protectora contra grupos epoxi, ester, aceites o disolventes orgánicos. Se aplicará sobre la piel limpia, siendo adecuado para evitar el contacto directo con las resinas y catalizadores endurecedores.
• Calzado de seguridad con suela de poliuretano antideslizante.
• Gafas de seguridad estándar contra proyecciones y salpicaduras y especiales para protección de radiación laser.
![]() |
Figura 7. Calzado reglamentario (mod. Halcón) Figura 8. Gafas reglamentarias (mod. Apolo)• Guantes de caucho nitrílico resistente química y mecánicamente con flocado interior para el empleo de materiales pre-impregnados y adhesivo en forma de aerosol. |
• Mascarilla de alta protección con filtro resistente a los agentes químicos, antes citados, especialmente para vapores epoxi o poliéster, disolventes y adhesivo en aerosol. Se debe disponer des mascarillas con filtros P2 o P3.
![]() |
Figura 9. Guantes de caucho para trabajo con sustancias agresivas (mod. Solvex) Figura 10. Mascarilla buco-nasal con filtros (mod. Advantage 200) |
En cualquier caso de duda se seguirá lo establecido en el artículo 18 de la Ley 31/1995, de 8 de noviembre, de Prevención de Riesgos Laborales.
Personal de trabajos de unión: remachado y encolado
Identificación del trabajador• División/ Departamento/Fábrica:• BPO/ BPU:• Puesto de trabajo específico: Ensamblador de piezas elementales• Puesto de trabajo genérico: MATERIALES COMPUESTOS
Descripción del puesto:
• Se realizan operaciones de aplicación de adhesivo en forma de película y líquido, también operaciones de taladrado y remachado con instalación de suplementos (shims).
Posibles riesgos asociados:
• Seguridad:
- Cortes y golpes
- Caídas de objetos por la manipulación de herramientas y útiles
- Contactos químicos con sustancias irritantes/alergizantes
- Contacto con polvo procedente de operaciones de taladrado o avellanado
- Sobreesfuerzos por levantamiento, sostenimiento o manipulación de útiles y en el montaje de piezas
- Atrapamientos
- Posibilidad de incendios • Higiénicos:
- Contactos con la piel y con las vías respiratorias de los vapores de los adhesivos y otros componentes de los materiales compuestos. Contacto con el polvo resultante del mecanizado[12]
- Ventilación en condiciones específicas, exposición a agentes tóxicos
- Ruidos puntuales durante las operaciones de taladrado, avellanado y remachado
Medidas de prevención:
• Lavarse las manos y cara antes de las comidas, fumar, o al final de la jornada, con agua y jabón• Utilizar calzado y mono protector desechables.• Utilizar mascarillas buco nasales• Mantener el área limpia y ordenada• No fumar durante el trabajo por el riesgo de higiénico y de incendios• Saber el manejo de los extintores• Conocer la situación del lava ojos• Solicitar la hoja de MSDS del producto al supervisor• Asistir a reconocimiento médicos voluntarios durante el año, y de forma obligatoria una vez al año• Medio de contacto para emergencias del protocolo médico
Detalle particular de medios de protección:
• A las condiciones descritas en el caso anterior hay que añadir, cremas protectoras y guantes especiales, monos desechables, protección cubre- calzado, tapones para los oídos y cualquier otro medio de protección que indique el fabricante de la materia prima.
Señalización del área:
Se debe señalizar la obligatoriedad de usar zapatos de seguridad, crema de seguridad, mascarilla buco-nasal y lavarse las
![]() |
manos, lava ojos, extintores, y área restringida. Un ejemplo cualquiera, la figura 11 muestra una foto aparecida en el diario “The Seattle Times” en la que podemos observar a una trabajadora Figura 11. Trabajadora en operación de lijado (fuente Mike Siegelrealizando una operación de lijado. Va provista de gafas para evitar proyecciones de aristas y unos guantes ergonómicos. Para la prevención de ingerir polvo por la nariz debería llevar una mascarilla y los guantes no son suficientemente fuertes para evitar que una astilla se pueda clavar en la mano |
CONCLUSIONES
A continuación se exponen las conclusiones más importantes como resultado del estudio:
• Es de vital importancia la incorporación a los procedimientos de los procesosde producción con material compuesto la aplicación de guías que midan a través de cuestionarios el riesgo laboral de los puestos de trabajo en las condiciones reales de las instalaciones.• En virtud de lo anterior proponer un plan de mejoras en materia deprevención de riesgos a aplicar de forma urgente, en algunos casos y paulatina en otros.• Hacer mucho hincapié en materia de formación de los trabajadores para quefavorezca no solo el aprendizaje sino también la concienciación de los riesgos que implica el uso de estos materiales.• Sin duda, el empleo correcto de los medios de prevención de riesgos hace seguro el uso de los materiales compuestos en todas sus etapas.• Una medida final que podemos pensar entre todos es si no debería incluir en los textos de mayor importancia en este campo un capítulo expresamente dedicado a los aspectos tratados en este artículo.
REFERENCIAS
- 1. Engineered Materials Handbook, Vol. 1: Composites. ASM International, Metals Park, Ohio: 1987.
- 2. González Díaz, R.E. “La mejora de los procesos con materiales compuestos mediante el empleo de Catia”. AECMA. V Congreso Nacional de Materiales Compuestos. MATCOMP2007. Pp. 7980
- 3. OSHA Technical Manual of Advanced Composites. US Labour Department. 2006. Chapter 6
- 4. The composite materials handbook MIL HDBK 173E. Thecnomonic Publishing Co. 2003. Pp 3847
- 5. Structure Repair Manual Boeing 757. SRM Handbook. The Boeing Co. 1997.
- 6. Safe Handling of Advance Composite Materials. SACMA. July 1991. Arlington USA
- 7. Occupational Safety and Health Administration, Department of Labor, Final Rule: Occupational Exposure to 4,4'Methylenedianiline (MDA) for 29 CFR Parts 1910 and 1926. Federal Register 57(154): 35630 (August 10, 1992)
- 8. Lubin, G., Ed. Handbook of Composites. Van Nostrand Reinhold Co., New York: 1982.
- 9. Anaya Durán, F. Riesgos asociados al montaje de fibra de carbono en la industria aeronáutica. AIRBUS. 2007
- 10. Worldwide Occupational Exposure Values. American Conference of Governmental Industrial Hygienist. 2007 CD database
- 11. Doyle, E.J. Suggested Strategies in Screening for Health Effects in Personnel who Work with Composites. Applied Industrial Hygiene Special Issue: December 1989. Pp 6467.
- 12. Guide to Preventing Dermatitis while working with advanced composites
materials. SHARP. Safety & Health Assement & Research for Prevetion. Washington State Departament of Labour and Industries. Report 55-04-99 y 55-03-99
Páginas web
- 1. www.magias.com fabricantes de máquinas automáticas de producción con materiales compuestos
- 2. www.seattletimes.nwsource.com noticias locales de Boeing.
Papers relacionados

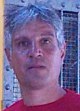



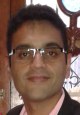