diagnóstico de las condiciones de trabajoen una empresa de motores eléctricos en Venezuela” ID 916
Escalona, Evelin
Centro de Estudios en Salud de los Trabajadores (CEST-UC)/ Facultad de Ciencias de la Salud/Universidad de Carabobo-Núcleo Aragua/ Final Av. Ruíz Pineda s/n ,Morita II. Aragua, Venezuela/ Tlf. 58-416-5436188/ evelinescalona@gmail.com
Yanes, LeopoldoInstituto de Altos Estudios de Salud « Dr. Arnoldo Gabaldon ». Ministerio del Poder Popular para la Salud. Maracay. Venezuela/ Telf. 58-416-6430790/ leo_yanes@cantv.netYanes, LuciaEscuela de Medicina « Witremundo Torrealba ». Centro de Estudios en Salud de los Trabajadores. Universidad de Carabobo/ Maracay. Venezuela.Poet_lucy@hotmail.com
Sandia, Ronald1
Gestión Ambiental/ Aldea Universitaria de Turmero/ Universidad Bolivariana de Venezuela. Sandia83@hotmail.comYanes, AnabelleCentro de Estudios en Salud de los Trabajadores (CEST-UC)/ Facultad de Ciencias de la Salud/Universidad de Carabobo-Núcleo Aragua/ Final Av. Ruíz Pineda s/n ,Morita II. Aragua, Venezuela.
ABSTRACT
ABSTRACT
Se estudiaron las condiciones de trabajo de los y las trabajadoras de una empresa de motores eléctricos. Estudio de campo descriptivo. Métodos. La observación. Entrevista individual, esquema corporal y el método DEPARIS modificado. Resultados: Fueron evaluados 27 puestos de trabajo, permitió identificar problemas en el diseño de los puestos de trabajo, la organización y en el entorno así como la opinión de los trabajadores. Conclusión: La incorporación activa de los y las trabajadoras en el diagnóstico de sus condiciones de trabajo, permitió la elaboración de propuestas de transformación y la integración del comité de salud y seguridad en la empresa.
Palabras clave
Palabras clave
Ergonomía, participación, condiciones de trabajo
INTRODUCCIÓN
INTRODUCCIÓN
En Venezuela la constitución aprobada en 1999 y la reforma de la Ley Orgánica de Prevención Condiciones y Medio ambiente de trabajo, establecen que los trabajadores y trabajadoras tienen el derecho a conocer y participar en el control de las condiciones peligrosas de trabajo. En este sentido el Instituto Nacional de Prevención Salud y Seguridad Laborales (INPSASEL) ha desarrollado importantes esfuerzos el cual se traduce, en la elección democrática de unos 47.000 trabajadores Delegados y Delegadas de Prevención en los últimos dos años. Estostrabajadores tienen el mandato legal de representar a los trabajadores en la vigilancia de las condiciones de trabajo. De manera que en Venezuela es de alto interés la aplicación de métodos que permitan la incorporación activa de los y las trabajadoras en el diagnóstico de sus condiciones de trabajo.
Análisis de la actividad
En el análisis de la actividad laboral se pueden distinguir los aspectos observables de la actividad y los mecanismos que regulan la organización. Así mismo es posible evaluar las diferentes tareas y operaciones para llegar a comprender las diferentes estrategias desarrolladas por los trabajadores. Inicialmente la observación abierta es la metodología más apropiada para el desarrollo de las observaciones preliminares, para posteriormente, a partir de estas observaciones, construir las hipótesis de trabajo y desarrollar las observaciones sistemáticas.
En el análisis de la actividad de trabajo es conveniente tener en consideración que todo trabajo humano tiene un componente físico y un componente mental y que no existe una separación entre ambos. Todo trabajo, por rutinario y simple que parezca tiene un componente mental que es necesario determinar [1]. Por señalar un ejemplo, citado por Plaisantin y Teiger [2] en los trabajos repetitivos y monótonos, donde las operaciones son realizadas en cortos períodos de tiempo, tienen implícito una serie de actividades mentales que ocupan prácticamente todo el cerebro. Cuando se habla del componente físico, es con referencia al trabajo muscular realizado durante la actividad laboral, bien sea este de tipo estático o dinámico. En este sentido podemos estudiar las posturas, los esfuerzos y las condiciones en que se ejecuta el trabajo. Para su evaluación se han desarrollado muchos métodos que permiten evaluar el trabajo muscular estático, el trabajo muscular dinámico, la capacidad física de trabajo etc. Este componente es observable y de fácil medición durante el desarrollo de la actividad de trabajo, así como existen múltiples indicadores de tipo fisiológico que es posible utilizar [1] [3] [4].
Cuando se menciona el componente mental, no se trata de una separación radical entre lo mental y lo físico, se trata simplemente de indicar cuales son las variables sobre las cuales queremos hacer énfasis. La actividad mental es uno de los aspectos mas complejos de evaluar de la actividad de trabajo ya que no es posible observarla directamente, solamente es posible observar las respuestas de esta actividad. Estas respuestas pueden ser espontáneas o provocadas en el trabajador. Las respuestas espontáneas que se han descrito son los desplazamientos, la postura y gestos adoptados por el trabajador, la dirección de la mirada, las operaciones realizadas, las diferentes acciones de comunicaciones establecidas durante la realización del trabajo, los resultados de estas acciones, etc. Las respuestas provocadas que se han descrito son aquellos productos de la verbalización y autoconfrontación del trabajador. De esta manera es posible conocer cual es la opinión del trabajador, que es lo piensa, que pasa dentro de su cabeza cuando realiza su trabajo [5].
En relación a la capacidad del trabajador, las exigencias y el tiempo requerido para realizar una tarea, este último puede ser utilizado como una medida del trabajo mental exigido, pero es necesario considerar que va a depender a su vez de cada individuo [6].
En ergonomía es importante distinguir los aspectos cognitivos y emotivos de la actividad mental. En relación a los aspectos cognitivos Montmollin [7]. refiere que por una parte están referidos al conjunto de actividades y procesos por los cuales el ser humano adquiere la información, la trata, la conserva y la explota. Así como también considera el ensamble de actividades por las cuales el sujeto desarrolla suconocimiento y adquiere nuevos conocimientos. Por otra parte incorpora la noción de “cognición située” para señalar el conocimiento que tiene el individuo antes de la actividad, el creado para la acción y durante la acción. Menciona también “la noción cognitiva socialmente distribuida” en este sentido toma en cuenta la actividad colectiva de numerosas situaciones de trabajo, en este sentido el análisis se orienta en relación al compartir de saberes entre los miembros de un equipo de trabajo.
En relación a los aspectos emotivos se ha estudiado en este sentido las emociones y sentimientos que puede dar origen el trabajo y que están en relación con la aparición de estrés. Sobre todo en aquellos empleos que se establece una relación de ayuda entre el trabajador y el cliente y donde hay que enfrentar al sufrimiento humano, como por ejemplo las enfermeras de hospital [8]. Pero esta noción ha sido poco considerada en la evaluación de los problemas relacionados con el trabajo femenino y a nivel de los estudios en ergonomía [9] [10].
La actividad de trabajo y sus consecuencias
Para la ergonomía, es de capital importancia el análisis de la actividad de trabajo, la cual es considerada como la respuesta del trabajador al conjunto de las condiciones de trabajo. Para realizar su actividad el trabajador o la trabajadora tienen el compromiso de cumplir con los objetivos definidos por la producción y/o la organización, para ello, deben adaptar sus propias características y capacidades en función de las exigencias laborales [11].
En cuanto a los determinantes de la actividad de trabajo se puede precisar: por una parte, está el trabajador con sus características específicas, y por la otra parte la empresa, la cual establece las reglas de funcionamiento y el cómo se va a realizar el trabajo. Mediando entre el trabajador y la empresa se encuentran: a) el contrato de trabajo, el cual establece los objetivos de la negociación; b) la tarea prescrita, la cual es impuesta por la empresa y establece los objetivos que el trabajador debe alcanzar y la tarea real sería la que es ejecutada por el trabajador o trabajadora para alcanzar los objetivos impuestos por la empresa. Particularmente entre las dos existen grandes diferencias las cuales no son consideradas por la empresa al momento de evaluar el trabajo, c) la actividad de trabajo, que va a ser la manera como el operador alcanza los objetivos que le son fijados y la cual va a ser el resultado del compromiso entre los factores externos al trabajador (objetivos y medios de trabajo de la empresa) y los factores internos (características personales y su estado para el momento de la realización del trabajo). Como resultado de esta actividad están las consecuencias sobre la producción y sobre la salud de los trabajadores [11].
Por otra parte consideramos importantes los aportes de Teiger [12]. en función de analizar las diferencias entre el trabajo prescrito y trabajo real, esta autora se ubica en tres niveles distintos: en primer lugar, se refiere a la noción de trabajo teórico, queriendo decir que es aquel trabajo que existe en las representaciones sociales mas conocidas y en el cual esta incluido la concepción de los ingenieros y los diversos conceptores en general, en segundo lugar, considera el trabajo prescrito o esperado, como aquel que se desarrolla a nivel local de la organización del trabajo, donde se fijan las reglas, los objetivos correspondientes de acuerdo a las representaciones del trabajo y teniendo en cuenta los antecedentes y las especificidades locales y en tercer lugar considera el trabajo real, que sería a nivel de la actividad de una persona, en un lugar y en un tiempo determinado (aunque esté incluida dentro de un colectivo de trabajado). Plantea que en el trabajo real es donde se desarrollan el saber hacer y los conocimientos de los operadores, donde se pone en juego los diferentes compromisos entre los objetivos a lograr y la capacidad del operador y finalmente donde se construye la subjetividad del trabajo.
Otro elemento a considerar en el análisis de la actividad de trabajo es la dimensión colectiva de la actividad. El trabajador o trabajadora no se encuentran aislados totalmente de manera que para desarrollar su trabajo se establecen diferentes articulaciones entre los colegas. En este sentido Guérin et al. [11], menciona las múltiples interacciones entre actividades como por ejemplo, la colaboración explicita para realizar conjuntamente una tarea, las comunicaciones que se dan en el trabajo, el conocer el trabajo que hacen otros etc.
OBJETIVO
Realizar el diagnóstico de las condiciones de trabajo y los problemas de ergonomía en una empresa de motores eléctricos con la participación activa de los trabajadores y trabajadoras.
METODOLOGIA
Tipo de investigación
Estudio de campo descriptivo, donde se utiliza el enfoque de la ergonomía.
Población y muestra
La empresa cuenta con una población de 276 trabajadores y 90 puestos de trabajo. La muestra es intencional. Los criterios de selección fueron: por solicitud de la empresa se realiza el estudio en el área de metalmecánica, en 27 puestos de trabajo, debido al incremento de accidentes de trabajo y lesiones músculo esqueléticas en los trabajadores.
Unidad de análisis27 Puestos de trabajo del área de metalmecánica y los trabajadores asignados a cada puesto.
Métodos, técnicas e instrumentos
Análisis de la actividad
Se observó la actividad durante una semana típica de trabajo, para identificar las tareas (ciclo de trabajo, variaciones observadas), las exigencias y los esfuerzos. Se realizaron entrevistas individuales en forma abierta a todos los trabajadores para conocer sus opiniones en cuanto a los problemas que estaban presentes en los puestos de trabajo y las sugerencias para mejorarlos.
Esquema corporal
A cada trabajador se le presento la figura del cuerpo humano vista de frente y dorsal, en el cual se les solicito señalaran los sitios de dolor y fatiga al final de la jornada de trabajo [13].
Método DEPARIS modificado
Se utiliza el método DEPARIS del autor J. Malchaire [14] y el cual fue modificado y adaptado por los autores para los efectos de este trabajo. El método original comprende 18 aspectos a evaluar y fue diseñado para ser aplicado en las pequeñas y medianas empresas. La modificación realizada del método para este trabajo comprendió, en primer lugar la adecuación del lenguaje al contexto venezolano. Se incorporó la descripción del trabajo y las zonas de dolor y fatiga al final de día de trabajo. Posteriormente se realizó un cuadro síntesis de los resultados obtenidos en cada puesto de trabajo y se incorporaron las soluciones propuestas por los y las trabajadoras en cada uno de los aspectos evaluados.
Forma de aplicación del método DEPARIS
En el marco de la estrategia SOBANE, se aplicó el método de diagnóstico participativo de los riesgos profesionales DEPARIS. Esta estrategia está concebida para ser utilizada por los trabajadores y sus superiores inmediatos; para identificar los problemas lo más objetivamente posible sobre su situación de trabajo cotidiana, no para dar información o responder cuestionarios, sino para discutir los detalles prácticos, lo que permite realizar el trabajo en condiciones óptimas para ellos y para la empresa. Éste método consta de dieciocho secciones. Los autores de este trabajo le incluyeron el punto señalado con el Nº 1 y el 20, de manera de integrar la evaluación del puesto.
Aspectos evaluados. Método DEPARIS Modificado
1) Descripción del trabajo
2) Las áreas de trabajo
3) La organización técnica entre puestos de trabajo
4) Las adaptaciones del trabajo
5) Los riesgos de accidentes
6) Los comandos y señales
7) Las herramientas y material de trabajo
8) El trabajo repetitivo
9) Las manipulaciones10) La carga mental11) La iluminación12) El ruido13) Los ambientes térmicos14) Los riesgos químicos y biológicos15) Las vibraciones16) Las relaciones de trabajo entre los trabajadores17) El ambiente social local y general18) El contenido del trabajo19) El ambiente psicosocial20) Zonas de dolor y fatiga en los trabajadores y trabajadoras al final de la jornada de trabajo.
Se organizaron reuniones con grupos homogéneos de trabajadores y trabajadoras con un máximo de 4 personas por grupo, se incluyó a los delegados de prevención y los miembros del sindicato. Se discutió con ellos los 20 aspectos antes mencionados en la búsqueda de problemas y sus soluciones.
Para cada aspecto evaluado los trabajadores calificaron usando colores y sonrisas precisando que prioridad le daban para ser intervenido o modificado el aspecto estudiado.
• Semáforo verde situación completamente satisfactoria• Semáforo amarillo: situación mediana y ordinaria para mejorar, si es posible• Semáforo rojo: situación insatisfactoria, susceptible de ser peligrosa, paramejorar necesariamente
Las reuniones se realizaron durantes las horas de trabajo, previa autorización del supervisor del área. La duración de las reuniones varió entre 60 a 90 minutos con cada grupo. El lugar donde se aplicó el método fue en una oficina de la empresa que por su ubicación permitía observar los puestos de trabajo evaluados.
Una vez finalizada la reunión el coordinador de la reunión sistematizó los resultados que luego fueron presentados a los trabajadores y a la empresa con el objeto de dar a conocer las soluciones a los problemas detectados.
RESULTADOS
El estudio se realizó en una empresa de Motores eléctricos, ubicada en la Zona Industrial Los Tanques en Villa de Cura, Estado Aragua. La empresa de capital nacional dedicada a la fabricación de motores para artefactos electrodomésticos y línea blanca. Se producen motores para lavadoras, secadoras, licuadoras, aires acondicionados, refrigeración comercial, motores universales, polo sombreado, condensador permanente, entre otros. Los principales objetivos de la empresa están basados en la eficiencia productiva, en la alta calidad de sus productos, en la mística de servicio a los clientes y en competitividad de precios a nivel nacional e internacional. Actualmente es la mayor compañía en su ramo, se ha consolidado como empresa nacional y se ha ampliado su área productiva integrando más maquinaria y nuevas líneas de producción. Cuenta con una fuerza laboral de 276 trabajadores.
La empresa tiene 02 galpones para las áreas de producción. En uno de ellos funciona el área de ensamble de los motores y en el otro funciona el área de metalmecánica. En este estudio fueron evaluados 27 puestos de trabajo en el área de metalmecánica. 5 puestos de la línea de carcasa; 8 puestos de la línea de inyección; 4 puestos de la línea de tapas y 10 puestos de la línea de ejes. Los elementos comunes que fueron encontrados en el diagnóstico de las condiciones de trabajo son expresados en cada una de las siguientes gráficas de las diversas líneas de producción evaluadas. Las líneas de producción evaluadas funcionan todas en un galpón en la empresa y en todos los puestos de trabajo se constata trabajo altamente repetitivo y en muchos casos muy artesanal.
Línea de carcasa
Esta línea esta conformada por cinco puestos de trabajo, en los cuales se produce la carcasa de los motores según las especificaciones requeridas por el modelo fabricado. En la línea de carcasa el puesto de soldadura de centro punto y la cabina de pintura en polvo fueron considerados más critico. A continuación se describen el trabajo observado en cada unos de los puestos.
Dobladora hidráulica y soldadora
Tarea principal: Realizar el doblado de la tira carcasa. Soldar la carcasa utilizando alambre Microwire
Descripción del ciclo de trabajo en el doblado de la tira carcasa• Carga con las dos manos el lote de láminas desde la paleta ubicada cerca del sitio de trabajo• Las coloca en mesa pequeña ubicada a la derecha• Toma una lámina• La introduce en el ángulo para doblar• Dobla una punta• Voltea la lámina• Dobla la otra punta• La coloca a su izquierda• Repite la operación hasta concluir con el lote de láminas
Descripción del ciclo de trabajo dobladora hidráulica y soldadora• Agarra la lámina doblada manualmente de la mesa• La introduce en la dobladora hidráulica• Presiona botones en parte inferior del tope de la mesa con ambas manos• Saca la carcasa de la prensa• Agarra otra lámina doblada y la coloca en la prensa• Introduce la carcasa en el molde de la soldadora• Golpea suavemente con un martillo de elaboración artesanal para que la carcasa haga tope• Presiona el switch de arranque (con la mano izquierda)• Vuelve a la dobladora hidráulica• Retira carcasa de la dobladora con la mano izquierda• Coloca nueva lámina con la mano derecha• Vuelve a la soldadora
Zonas de dolor y fatiga: Refiere dolor de cabeza, así como dolor en hombro derecho espalda alta, región lumbar leves, rodillas, hueco poplíteo y pantorrillas. Manifiestan los trabajadores que el dolor se origina por postura de pie prolongado y por doblar manualmente la lámina.
Puesto de trabajo Soldadura de centro punto
La tarea principal: Soldar las orejas/soporte a las carcasas Descripción del ciclo de trabajo:
• Agarra la carcasa del riel ubicado a la derecha• Coloca la carcasa en útil o patrón (de hierro o aluminio)• Coloca la carcasa con el patrón en la soldadora• Sostiene el patrón con la izquierda• Agarra la oreja/soporte con la derecha• La coloca sobre la carcasa• Levanta el pie (alterna derecho e izquierdo) para accionar el pedal de soldadora• Presiona 2 o 3 veces por oreja según el modelo de la carcasa y oreja• Levanta el pie• Retira la carcasa con las 2 manos• Coloca la carcasa en mesa a su izquierda
Zonas de dolor y fatiga: Hombros, espalda alta y región lumbar, rodillas (parte posterior) y las pantorrillas. Al final de la jornada siente agotamiento físico general o cefalea.
Foto. 1. Soldadora centro punto
Puesto de Trabajo: Torno de carcasa
La tarea principal: tornear la carcasa Descripción del ciclo de trabajo• Toma las carcasas• La coloca en el torno presiona un botón mientras frena el torno• Pule la carcasa• Saca la carcasa• Deposita la carcasa en la mesa del lado izquierdo
Foto. 2. Torno de carcasa
Zonas de dolor y fatiga: Hombro derecho, espalda alta y región lumbar. Al final de la jornada siente agotamiento físico general y cefalea.
Puesto de trabajo: Cabina de pintura en polvo
Tarea principal: Desengrasar, fosfatizar y pintar estatores, carcasas, porta tripoides, soportes ACS, triángulos para ventiladores de pared, soportes 2.600 y 2.500.
Descripción del ciclo de trabajo
Fosfatizado de estatores• Puesta a punto de la máquina (entre 6 y 7 am)• Mide los enjuagues, la concentración de ácidos, limpia las boquillas• Entre las 7 y 9 am comienza a llenar la cadena• Desde las 9 am baja ganchos con piezas fosfatizadas y sigue llenando la cadena con los ganchos que se desocupan• Empuja el carrito con los campos• Lo coloca frente a la cadena de pintura• Agarra el chorizo de estatores con la derecha y lo sostiene por debajo con la izquierda• Lo guinda en gancho del trole
• Cuando sale el estator fosfatizado baja el gancho con la izquierda• Soporta abajo con la derecha• Quita el gancho del chorizo• Coloca el chorizo en el el cajón
Pintura de carcasas, soportes, pedestales, tripoides, ángulos:
• Empuja el carrito con cesta de carcasas del área de carcasas• Lo coloca frente a la cadena de pintura• Agarra gancho ubicado al frente• Con la izquierda agarra una carcasa• La introduce en el gancho• Agarra otra carcasa• La introduce en el gancho• Guinda el gancho en la cadena con las dos carcasas• Repite el proceso 150 veces cuando comienzan a salir simultáneamente saca piezas y monta nuevas por procesar• Cuando sale las carcasas baja el gancho con la izquierda• Golpea el gancho para que salgan las carcasas• Se agacha para colocarlas en el cajón
Para las otras piezas es similar el proceso. Para el soporte 2500 y 2650 la altura es mayor. (Sugieren una paleta en el piso que los suba un poco para colocar las piezas)
Zonas de dolor y fatiga: Dolor moderado en espalda media, cuello (intenso), hombros, brazos y antebrazos piernas y pies (intenso). Uno de los operarios reporta haber presentado accidentes en manos (muñecas) estuvo tres meses de reposos durante el último año.
Foto. 3. Cabina de pintura en polvo
Resumen de la síntesis de la evaluación participativa de los cinco puestos de trabajo en la línea de carcasa (ver Grafico N° 1).
En cuanto a las áreas de trabajo: En todos los puestos de la línea de carcasa es necesario intervenir, el más crítico en este aspecto fue la cabina de pintura en polvo. El operario trabaja en un pasillo con poco espacio, no hay organización apropiada de los cajones y cajas donde se colocan las piezas por fosfatizar o ya procesadas, lo que produce hacinamiento en el área (Foto N° 5). En la Dobladora Hidráulica se recomienda ampliar el tamaño de la superficie de trabajo para que la actividad se pueda realizar con mayor comodidad. Se recomienda la demarcación y señalización de las áreas de trabajo y de circulación de montacargas y carritos para evitar accidentes.
La organización técnica entre los puestos: Organizar mejor el espacio de trabajo entre los tres puestos de la Dobladora Manual Hidráulica y Soldadora. Ya que el paquete de las tiras de carcasa las colocan sobre un pipote de basura, ya que no dispone de espacio suficiente.La adecuación del trabajo: En el Torno de carcasa se sugiere, colocar una alfombra de descanso, colocar una silla giratoria alta que permita alternar posición de pie y sentado. Mejorar la distribución de los objetos de trabajo para trabajar con mayor comodidad y evitar que estén tan juntos con los otros puestos. Se requiere mejorar las dimensiones de las superficies de trabajo para trabajar con mas comodidad, referida a la distancia horizontal y la altura de la plataforma, que permita trabajar lo mas cerca del cuerpo, que tenga espacio disponible para los pies y que la plataforma sea de tamaño variable para garantizar que varios usuarios puedan quedar cómodos. En la cabina de pintura para los campos se recomienda que los ganchos sean más largos. Actualmente miden 46 cm. se sugiere 56 cms. para que los trabajadores no tengan que elevar los brazos.
En el caso de los soportes 2.500 y 2.650 se recomienda que usen una plataforma móvil que eleve al trabajador mientras procesa estas piezas y puedan retirarla finalizado la operación. En la Soldadura de centro punto. Sustituir los patrones de hierro por patrones de aluminio, los cuales son más livianos y no se calienta como el hierro. Revisar distancia visual y altura del útil de la máquina o posibilidad de una silla para este puesto para evitar inclinación del cuello durante el ciclo de trabajo.
Los riesgos de accidentes se deben mantener el uso de los equipos de protección personal lentes, botas, mascarilla, uniforme y el uso de guantes para protegerse de accidentes.
Las herramientas de trabajo: Proveer las herramientas necesarias para el ajuste del torno de carcasa. Mejorar el diseño de las herramientas para que sean más cómodas al manipularlas.
El trabajo es muy repetitivo en todos los puestos de trabajo, se requiere introducir pausas de descanso compensadoras y ejercicios de estiramiento y relajación de los músculos involucrados.
Gráfico Nº 1. Síntesis de la evaluación de la línea de carcasa. Área de Metalmecánica. Empresa de Motores eléctricos. Aragua, Agosto 2007
LÍNEA DE CARCASAS
1.- áreas de trabajo
![]() |
2.- organización técnica entre puestos de trabajo3.- Adecuación del trabajo4.- Riesgos de accidentes5.- Los comandos y señales6.- Las herramientas y el material de trabajo7.- El trabajo repetitivo8.- Lasmanipulaciones de cargas9.- la carga mental10.- La iluminación11.- El ruido La 12.- El ambiente térmico13.- Lacontaminación con sustancias quimicas14.- Las vibraciones15.- Las relaciones de trabajo entre operarios16.- El ambiente social local y general17.- El contenido del trabajo18.- El ambiente psicosocial19.- Zonas de dolor en el esquema corporal |
manipulación de cargas esta presente en todos los puestos evaluados, en todos los casos se recomienda adecuar la forma de transportar los materiales de trabajo. El puesto más critico es este aspecto fue la cabina de pintura.
La carga mental fue considerada de mediana intensidad en casi todos los puestos. El trabajo requiere concentración en la tarea.
Los factores ambientales evaluados no fueron considerado crítico excepto el ruido proveniente de área de trabajo vecinas en el torno y en la cabina de pintura.
Los aspectos psicosociales fueron bien valorados en todos los puestos. En cuanto a las zonas de dolor y fatiga es una constante todos los trabajadores manifiestan dolor músculo esquelético, debido a la repetición de las tareas, las posturas incomodas, la alta repetición de las tareas. Finalmente, en todos los puestos de esta línea es necesario intervenir mejorando el área de trabajo, para evitar los accidentes, mejorar la adecuación de las herramientas de trabajo y protección de los trabajadores para manejar el material de trabajo y la forma en que son manipulados los objetos o materiales de trabajo. En todos los puestos de trabajo es común los dolores a nivel músculo esquelético.
Línea de inyección
La Línea está conformada por ocho (8) puestos de trabajo. Los puestos más críticos fueron los tornos, el insertado manual de distanciales y el Insertado de Ejes Falsos y Verdaderos. Sin embargo todos los puestos de trabajo requieren de cambios ya que constituye el área evaluada con mayores problemas de inadecuación de los puestos de trabajo (ver gráfico Nº 2).
Puesto de trabajo: Torno Rotores RAC
Tarea principal: Tornear rotores RAC (ver Foto. 6) Descripción del ciclo de trabajo• A las 7:00 a.m. prende el torno, lo calienta por 15 minutos• El operario de la bruñidora pasa las torres de rotores al riel del torno• Agarra 2 rotores cada vez hasta hacer torre de 5• Los coloca a la derecha sobre el torno• Agarra 1 rotor con la mano derecha, Lo coloca en el útil• Agarra la cuña de acero con la mano derecha• La coloca en el torno• Pasa el switche centro punto ubicado a su derecha• Mueve hacia delante la palanca para que se mueva el torno• Pasa el switche centro punto• Saca la cuña• Voltea el rotor• Coloca la cuña• Pasa el switche centro punto• Mueve la palanca• Saca el rotor• Mide el diámetro del rotor con la galga• Coloca el rotor sobre la máquina a la izquierda• Retira la viruta del torno con varilla de metal• Repite el proceso• Una vez que llena la superficie izquierda de la máquina, traslada los rotores y losorganiza en torres de 5 piezas sobre un carro hasta llenar el carro con 45 torres (250 rotores).• Traslada las torres de 5 hileras de rotores al riel del puesto del horno de dropeado. En esta tarea tarda 30 minutos. Realiza esta tarea dos veces por jornada.
Procesa 50 rotores por hora Le piden 400 rotores por día.
El trabajo es muy repetitivo el ciclo de trabajo dura 36,50 seg. El trabajador realiza torsiones frecuentes del tronco.
En el puesto de trabajo potencialmente pueden ocurrir los siguientes accidentes: Heridas leves +, Caídas de objetos +, Apisonamiento ++, Seccionamiento ++, Pinchazos +, Cortaduras +, Quemaduras +
Proyección ++.
Zonas de dolor y fatiga: Refiere el trabajador dolor en los miembros inferiores, en las extremidades superiores sobre todo en las muñecas debido a los movimientos repetidos que realiza.
Puesto de Trabajo: Inyección Yota
Tarea principal: Inyectar aluminio en forma líquida al rotor a través de un proceso mecanizado (ver Foto. 7).
Descripción del ciclo de trabajo: Proceso de Desgasificación:
• Este proceso se realiza una vez por turno. Consiste en completar la carga de aluminio en el crisol.
• Se abre la llave de paso de aire para que suba la lanza de grafito• Con la barra de metal se empuja la lanza al centro del crisol• Una vez entre en el seguro, la lanza se fija• Enciende el tablero en el botón derecho para que pase la corriente• Presiona botón izquierdo para bajar la lanza• Presiona botón del medio para que la lanza gire• Se deja que remueva el aluminio en el crisol durante 25 minutos para que el gas se expanda• Presiona botón izquierdo para subir la lanza• Hala con la barra hacia el lado de afuera del crisol• Presiona botón izquierdo para bajar la lanza• Presiona botón del centro para apagar el motor• Cierra la llave de paso• Limpia la escoria del aluminio del crisol con la espumadera• Coloca la escoria en lámina de acero ubicada en el piso• (La exposición al calor no es más de 10 minutos)
Precalentamiento del molde:
• Coloca la manguera del quemador en entrada de gas• Abre la llave de paso del gas ubicada al lado de la Yota.• Prende un trozo de material combustible (cartón) y abre la llave de paso de gas, colocando el material cerca del mechero para encenderlo• Coloca el mechero debajo del molde de la Yota por 10 a 15 minutos.• (La exposición al calor no es más de 5 minutos)• Cierra la llave de paso• Desconecta la manguera
Proceso de inyección de rotores
• Toma 4 rotores (2 en cada mano). Los coloca uno a uno en el molde• Luego toma dos rotores adicionales y los coloca en los moldes restantes• Presiona botón de control para poner la máquina en automático• Acciona botón de brazo del robot• Acciona botón que cierra el molde de la máquina• Pone en neutro botón automático usando la mano derecha• Toma la manguera de aire y desmoldante (con la mano izquierda)• Acciona gatillo de la pistola• Presiona gatillo de la pistola para limpiar el molde• Toma la barra para retirar la colada de plancha móvil• Limpia la plancha móvil con pistola de aire y desmoldante• Presiona botón expulsor para retirar los rotores de la cavidad• Repite el proceso
Foto 4. Inyección Yota (coloca rotores)
Potenciales accidentes en el puesto de trabajo: Pinchazos +, Quemaduras ++, Proyección ++ (molde no cierra bien y chispea), Explosión +, Estallido + y Caída de personas +.
Condiciones peligrosas observadas: Exposición al aluminio liquido caliente. Tienen precaución que los lingotes estén bien secos y lo colocan cerca del calor para evitar salpicaduras al introducirlos en el crisol. Piso dañado al lado de máquina, le colocan una lámina de metal. Canal alrededor no tiene rejilla ni protección, puede ocasionar accidente. Piso resbaladizo debido al desmoldante
Equipos de Seguridad utilizados:
• Lentes, botas de amianto, uniforme, guantes de carnaza, delantal de amianto• El operario sólo estaba usando botas y lentes. No tenía delantal ni guantes
Zonas de dolor y fatiga: Hombros, ambos brazos, región lumbar y las piernas. Dolor de cabeza debido al calor. El martillear constante para sacar los rotores les produce dolor en los hombros y en los brazos
Puesto de Trabajo: Insertado de eje verdadero
Tarea principal: Insertar eje verdadero (ver Foto. 5) Descripción ciclo de trabajo
Rueda la cesta por el riel desde desinserción
Saca los rotores de la cesta con ambas manos y lo coloca sobre mesa del puesto de trabajo de manera organizada
Agarra un puño de ejes y los va posicionando en cada rotor (repite hasta completar todos los que tiene en la mesa)
Con la mano derecha agarra el rotor con su eje y lo coloca en utillaje de la máquina
Con ambas manos presiona botones en parte baja de la mesa para que la prensa baje
Con la mano izquierda retira el conjunto del rotor
Coloca el conjunto del rotor en la tabla sobre riel a su izquierda
Foto 5. Insertado de eje verdadero
La operaria manifiesta que produce entre 1.500 y 2.000 rotores por día y procesa unos 360 rotores por hora. Ella alterna su actividad principal con el desinsertado de ejes falsos y con el insertado manual de distanciales.
Zonas de dolor y fatiga: Dolor en el hombro derecho, Espalda alta, región lumbar, muslo derecho y en ambos pies (dolor intenso).
Puesto de trabajo: Empilado Rotor REV
Tarea principal: Empilado de rotor Descripción del ciclo de trabajo• El montacargas trae el cajón con “chorizos” de laminación• Lo coloca de lado derecho del puesto de trabajo• Con ambas manos saca el chorizo del cajón• Lo coloca en envase de metal al lado derecho (hasta 14 chorizos)• Agarra un chorizo de láminas del recipiente• Lo coloca sobre el ángulo de soporte para el corte• Le retira guía de seguridad• Con la mano derecha agarra la galga o selector• Con el pulgar izquierdo presiona el chorizo• Con la galga mide el grupo de lámina• Agarra el grupo de láminas con los dedos pulgar e índice• Con la derecha toma el eje falso y lo introduce en el orificio central de láminas de rotor• Repite la operación 15 veces y coloca los rotores armados en ángulo soporte al lado derecho de la prensa• Toma rotor con la derecha• Inserta en vaso de prensado• Con la derecha toma paleta para darle “SKew” (la medición adecuada)• Con la derecha sostiene la paleta y gira ¼ de vuelta a la derecha.• Con la mano izquierda presiona botón de activación de la prensa• Con pie izquierdo presiona pedal que sube el rotor• Con mano izquierda retira el eje de la prensa• Coloca el eje en riel que lleva rotores a inyección Zona de trabajo:
La zona de trabajo del Empilado de Rotores es de 40cm de largo x 30cm de ancho. Es sumamente reducido.
Alcances, postura laboral y Ubicación de planos del área:
Como se mencionó anteriormente, cada turno de Empilado de Rotor, debe elaborar 1500 Rotores. Éstos, al ser Empilados, pasan a una rampa de 2 niveles que los dirige a la máquina de Inyección de Aluminio, donde un operador se encargará de realizar la tarea.
Dicho esto, los trabajadores distribuyen el 80% del tiempo (5-6 horas) en empilar los Rotores y colocarlos en la rampa inferior. El 20% del tiempo restante (1-2 horas), empilan los Rotores para dejarlos en la rampa superior con la finalidad de mantener reserva de Rotores para el próximo turno y evitar el “coleo” con el operador de Inyección de Aluminio. En base a esto, la distancia de extensión del brazo del trabajador hacia la rampa inferior es de 70cm y a la superior es de 110cm (ver Foto 11). Con respecto al 80% del tiempo, es decir 5-6 horas, el trabajador tiene un alcance de 27-30 cm con relación al área de trabajo. Y la postura dominante es la posición sentada con el brazo izquierdo en abducción en ángulo de 90º, siendo muy exigente.
Foto 6. Empilado de rotores
Características de la silla:
Es incomoda e inadecuada, los trabajadores le han realizado adaptaciones con tirro, le colocaron otro cojín en fin buscando comodidad. Es necesario intervenir urgente en colocar una silla apropiada.
Espacio disponible para las piernas:
El diseño del puesto obliga al trabajador a mantener sus piernas en semiflexionadas y apoyadas sobre el reposapié de la silla ya que no hay espacio para estirar las piernas.
Puesto de trabajo Insertado manual de distanciales
Tarea principal: Colocar los distanciales a los rotores y empujarlos con el distanciador manual (ver Foto. 13).
Descripción del ciclo de trabajo:
• Los rotores llegan al puesto en una tabla que trae el operario del torno.
• Sobre la mesa al lado izquierdo tiene dos charolas: una grande con distanciales y la otra pequeña con arandelas.
• Agarra un puñado de arandelas con su mano izquierda• Coloca una arandela en cada eje de rotor (son 72 rotores por tabla)• Con ambas manos toma un puñado de distanciales• Los va colocando sobre los 72 rotores• Agarra el insertador con la mano derecha y golpea el rotor para introducir el distanciador• Con ambas manos voltea los rotores sobre la tabla• Con las dos manos toma un puñado de distanciadores• Los va introduciendo en el lado corto del eje• Toma el insertador con la derecha y golpea cada rotor para bajar los distanciadores• Con el Vernier digital mide la distancia entre los dos distanciales rotor por rotor• Cada operario debe revisar todos los rotores• Coloca la tabla con los rotores en el carro transportador (hay dos modelos decarro: los de 4 y los de 9 tablas).• Una vez lleno el carro transportador, lo empuja hasta el área de Control de Calidad• Si Control de Calidad rechaza los rotores, busca nuevamente el carro transportador con los rotores y lo retorna hasta el puesto de trabajo
Al concluir el proceso de revisión, empuja el carro transportador hasta el Área de Control de Calidad. El operario textualmente señaló lo siguiente:
“Nuestro proceso termina al entregar el carro transportador con los rotores procesados en control de calidad”.
Foto.7. Insertado manual de distanciales
Resumen de la síntesis de la evaluación participativa de los ocho puestos de trabajo en la línea de Inyección (ver Grafico N° 2).
Las áreas de trabajo: Los trabajadores pueden comunicarse libremente y cada operador puede visualizar a sus colegas. En cuanto a las vías para las personas y montacargas no están demarcadas, así como las salidas de emergencia. La limpieza del área es adecuada, son los propios operadores que la realizan al final de la jornada. La organización de los materiales no es adecuada y cuentan con muy poco espacio para colocar las herramientas. El diseño de las mesas de trabajo de los distanciales no son iguales, existen diferencias del espacio disponible debajo de la tabla para colocar la herramienta. Esta situación ocasiona incomodidad y produce malestar en la trabajadora ya que se lesiona las manos con el material al chocar sus manos con los rotores. Las máquinas requieren mantenimiento correctivo y preventivo.
La organización técnica entre puestos: en este aspecto la línea tiene una situación critica requiere re-organizar mejor los puestos de trabajo de manera de garantizar una mejor ubicación de los puestos según el orden de las operaciones y evitar el hacinamiento.
Las adecuaciones del trabajo: en todos los ocho puestos evaluados se requiere realizar correcciones de la altura de trabajo, problemas con las zonas de alcancefuncional. Las sillas son muy incomodas, no son regulables en altura y algunas operarias quedan en posición inadecuada, el material es impermeable lo que genera calor en el cuerpo. El cojín esta vencido y el espaldar es muy bajo.
Los riesgos de accidentes están presentes en todos los puestos de trabajo, siendo más peligrosos los puestos de la inyección Yota, los Tornos y el insertado manual de distanciales.
Los comandos y señales, se observaron inadecuación de los comandos en los puestos de insertado de eje falso y verdadero. Las herramientas y material de trabajo, requiere de adaptaciones. El trabajo repetitivo esta presente en la mayoría de los puestos. Es una constante los problemas de dolor músculo esquelético en todos los puestos de trabajo.
La manipulación de cargas constituye un problema a resolver. En cuanto a los problemas del ambiente de trabajo, el ruido y el calor son los principales problemas señalados.
Gráfico Nº 2. Síntesis de la evaluación de la línea de Inyección. Área de Metalmecánica. Empresa de Motores eléctricos. Aragua, Agosto 2007
Línea de Inyección
1. Área de trabajo.
![]() |
2.- Organización técnica entre los puestos3.- Las adecuaciones del trabajo4.- Riesgos de accidentes5.- Los comandos y señales6.- Las herramientas y material de trabajo7.- El trabajo repetitivo8.- Las manipulaciones9.- la carga mental10.- La iluminación11.- El ruido12.- Los ambientes térmicos13.- Los riesgos químicos y biológicos14.- Las vibraciones15.- Las relaciones de trabajo entre operarios16.- El ambiente social local y general17.- El contenido de trabajo18.- El ambiente psicosocial19.- Zonas de dolor en el cuerpo al final de la jornada de trabajo |
Línea de Tapas.
En está línea el puesto con mayor problemas fue la sopladora (ver Foto 10), todos los trabajadores y trabajadoras son de la opinión que es necesario re-ubicar este puesto en otra área que no contamine de ruido al resto de la línea.
En todos los puestos existen problemas de manejo inadecuado de sustancias químicas como la taladrina, ruido, problemas de inadecuación del trabajo (sillas incomodas); problemas de los mandos y señales (ver gráfico Nº3).
Foto 8. Sopladora de tapas.
Gráfico Nº 3. Síntesis de la evaluación de la línea de Tapas. Área de Metalmecánica.
Empresa de Motores eléctricos. Aragua, Agosto 2007
Línea de Tapas
1. Área de trabajo.
![]() |
2.- Organización técnica entre los puestos3.- Las adecuaciones del trabajo4.- Riesgos de accidentes5.- Los comandos y señales6.- Las herramientas y material de trabajo7.- El trabajo repetitivo8.- Las manipulaciones9.- la carga mental 10.- La iluminación11.- El ruido12.- Los ambientes térmicos13.- Los riesgos químicos y biológicos14.- Las vibraciones15.- Las relaciones de trabajo entre operarios16.- El ambiente social local y general17.- El contenido de trabajo18.- El ambiente psicosocial19.- Zonas de dolor en el cuerpo al final de la jornada de trabajo |
Línea de Ejes
Todos los puestos de trabajo tienen en común la repetición de los mismos gestos y operaciones, inadecuación de los puestos de trabajo desde el punto de vista del diseño. Todos los trabajadores y trabajadoras manifiestan síntomas de dolores y fatiga. La postura de pie es la predominante. En aquellos puestos de trabajo que se realiza la tarea sentada, las sillas son inadecuadas.
Puesto de la Rectificadora 01 y 02
En ambas rectificadoras cada una de ellas tiene dos puestos. El operario 1 y el operario 2. Tarea principal: Devastar los ejes para disminuir el diámetro.
Descripción del ciclo de trabajo: Operario 1 proceso de ejes Rac• Traslada carrito con charola de ejes desde laminadora• Coloca el carrito en la parte de atrás de la silla de trabajo• Coloca una cantidad en la mesa de trabajo al frente• Toma un eje con la mano derecha• Lo coloca en la guía de entrada• Lo empuja hacia adentro con la mano izquierda• Con la derecha agarra un palo de madera con la punta afilada para empujar el eje por la guía• Repite la operación
Foto 9. Rectificadora 1. Operario 1 Foto 10. Rectificadora 2. Operario 1
![]() |
• Toma un puño de ejes con la mano izquierda• Apoya el antebrazo sobre un taco de madera con una serie de trapos que utiliza como almohadilla• Toma un eje con la mano derecha• Lo coloca en la guía de entrada• Empuja el eje hacia adentro con la derecha• Si el eje se traba en la guía, lo ayuda a salir empujando con palo de madera• Repite la operación |
Ejes REV
Estrategias para descansar Operario 1• Trabaja sobre plataforma de madera• El puesto tiene una alfombra plástica antiresbalante• Descansa el pie sobre pedazo de hierro de manera alterna• Los operarios alternan el que entrega en la Rectificadora 1, recoge en la rectificadora 2. Esto permite alternar posición de pie y sentado en cada función
Descripción del ciclo de trabajo: Operario 2• Los ejes Rev van callendo en una bandeja debajo de la guía• Recoge los ejes• Mide en cada grupo, 1 eje• Coloca los ejes en la charola uno sobre otro• Alterna posturas sentado y de pie por cuanto se tiene que parar a medir los ejes Las áreas de trabajo en la Rectificadora 1 y 2.
En la línea de ejes hay dos rectificadoras de ejes, las cuales están ubicados en el lado derecho del Galpón de Metalmecánica es un espacio abierto, los trabajadores pueden comunicarse libremente y cada operador puede visualizar a sus colegas. No existen limitaciones para la movilización, los espacios entre las máquinas son adecuados. En cuanto a las vías para las personas y montacargas no están demarcadas. La limpieza del área es adecuada, son los propios operadores que la realizan al final de la jornada. La organización de los materiales es adecuada y cuentan con espacio para colocar las herramientas.
La organización técnica entre puestos de trabajo:
• Los puestos en la Rectificadora están dotados de los materiales necesarios para realizar el trabajo, el área destinada para almacenar es independiente para cada puesto. Las interacciones entre los operarios se realizan sin dificultad. Se trabaja contra reloj esta establecido una meta de producción por día de trabajo, en la rectificadora 1 es de 7.000 ejes, en tanto en la rectificadora 2 varía entre 5.000 y6.000 unidades.• Trabajan de 7:00 a.m. - 4:30 p.m. Los viernes trabajan de 7:00 a.m. a 3:30 p.m.• Pausas: 30 minutos para el almuerzo• Todas los operarios son hombre La adecuación del trabajo
En el puesto de la Rectificadora 1, el operario 1 requiere estar todo el tiempo de pie, no cuentan con la posibilidad de sentarse. Área de trabajo horizontal ó distancia desde la línea media del cuerpo a donde coloca las manos para trabajar es adecuada. El área de trabajo vertical es adecuada, tomando como referencia la altura del codo de los trabajadores. Se observa que existe una paleta que esta colocada en frente a la máquina, la cual hace que el trabajador adopte una postura incomoda, teniendo que inclinar el cuello y lateralizar el tronco para buscar apoyo del brazo izquierdo. La distancia visual es de 50 cm. se considera que es adecuada.
El ángulo visual varía entre 15º habitualmente y 45º al momento de realizar la lectura del micrómetro, siendo ambos casos adecuados. Espacio disponible para piernas y pies: Hay espacio disponible para los pies.
El operario 2 en la rectificadora 1. Área de trabajo horizontal no es adecuada. El cajón donde caen los ejes mide 73 cm de largo, los ejes que vienen por una canal caen a una distancia de 70 cm del operario, lo que obliga permanentemente a estirar los brazos para recoger los ejes.
Foto 11. Rectificadora 1. Operario 2
![]() |
70 cm |
En la rectificadora 2 el puesto del operario 2, la bandeja es rectangular, el operario se sienta del lado de la bandeja, y la forma como esta colocada lo obliga a trabajar con el brazo derecho con movimientos de abducción. No cuenta con espacio para colocar las piernas y los pies.
Foto 12. Rectificadora 2. Operario 2 Foto 13 Rectificadora 2. Operario 2 no cuenta con espacio paralos pies
El área de trabajo vertical en el operario 2 no es adecuada esta muy alta para realizar las tareas de medición.
La distancia visual es de 50 cm. se considera que es adecuada. El trabajo demanda alta precisión visual solamente para medir los ejes en el micrómetro por lo que la distancia recomendada es entre 10 y 20 cm. durante esta operación
En la rectificadora 1 el micrómetro está ubicado en la bandeja donde caen los ejes.
Foto. 14 Trabajador usa micrómetro
En la rectificadora 2 la ubicación es diferente esta colocada en una posición incomoda para trabajar.
La organización técnica entre puestos de trabajo• Los puestos están dotados de los materiales necesarios para realizar el trabajo, el área destinada para almacenar es independiente para cada puesto. Las interacciones entre los operarios se realizan con dificultad debido a los implementos de seguridad utilizados. Se trabaja contra reloj esta establecido una meta de producción por día de trabajo. Trabajan de 7:00 a.m. - 4:30 p.m.• Pausas: 30 minutos para el almuerzo• Todas las operarios son hombre
Las herramientas y material de trabajo
Los operarios disponen de herramientas para cada operación, los objetos se toman con seguridad y facilidad y su manipulación causan fatiga de manos y de brazos hecho que se evidencia cuando el trabajador apoya el antebrazo izquierdo en el taco de madera. La máquina presenta derrame de aceite.
Trabajo repetitivo. El trabajo requiere repetir continuamente los mismos gestos en las mismas posturas y con los mismos esfuerzos. Promedio diario de producción:
6.000 unidades. Procesan 1.000 en una hora. Este microciclo tiene una duración de 52,50 segundos.
La manipulación de cargas. En este puesto se manipulan los ejes de REV y RAC y mantienen en la mano varios ejes para alimentar la máquina. Sostiene con la mano un puño de 27 a 30 ejes. Se pesaron 30 ejes: 1,153 Kg. La altura de los carritos transportadores es adecuada facilitando el transporte de la carga.
La carga mental. El trabajo solicita una atención intensa. No toma prácticamente decisiones ya que el trabajo es altamente repetitivo. Siempre esta muy pendiente que un eje este doblado.
Puesto de trabajo Torno
Tarea Principal: Cortar barras de acero Descripción del ciclo de trabajo:
• Al iniciar la jornada prende el torno accionando el botón rojo ubicado en el tablero del torno• Carga barras desde el contenedor hasta el soporte, entre 7 y 10 barras cada vez(peso de barra de REV es de 1,5 Kgs y la barra de RAC es de 3,7 Kgs). Esta operación es efectuada cada tres días aproximadamente.• Coloca las barras en el soporte• Toma una barra, la levanta con ambas manos, la posiciona dentro del tubo alimentador, una vez que está en posición, verifica y ajusta con manivela colocada en la parte superior del alimentador• Se ubica en su posición de pie junto a la máquina• Con la mano derecha va recibiendo los ejes• Con la izquierda interrumpe cuando se traba algún eje• De cada barra verifica el diámetro de 3 o 4 ejes.• Coloca los ejes en la charola• Al completar de llenar la charola la traslada hasta la laminadora en el carrito• Después de la jornada de trabajo, cada quien limpia su puesto con una mopa con desengrasante.
Variaciones observadas del ciclo de trabajo• Acciona el botón interruptor manual del equipo cuando coloca la barra, cuando se traba un eje o para medir el eje• Cuando el eje se traba, con la mano izquierda da vueltas a la manivela hacia delante o hacia atrás para sacarlos. La máquina puede usarla manual.• El torno N° 6 la operaria mantiene el brazo dentro del torno para recibir los ejes porque vienen muy rápido. La viruta sale y hace que se enrede el segundo eje y puede romper las cuchillas.
Las áreas de trabajo en los Tornos
En el área de tornos son seis máquinas los cuales están ubicados es un espacio abierto, los trabajadores pueden comunicarse libremente y cada operador puedevisualizar a sus colegas. No existen limitaciones para la movilización, los espacios entre las máquinas es de 80 cms siendo adecuados. En cuanto a las vías para las personas y montacargas no están demarcadas. La limpieza del área es adecuada, son los propios operadores que la realizan al final de la jornada. La organización de los materiales es adecuada y cuentan con espacio para colocar las herramientas.
La organización técnica entre puestos de trabajo: Los puestos están dotados de los materiales necesarios para realizar el trabajo, el área destinada para almacenar es independiente para cada puesto. Las interacciones entre los operarios se realizan sin dificultad y libremente. Se trabaja contra reloj esta establecido una meta de producción por día de trabajo. Trabajan de 7:00 a.m. - 4:30 p.m. La pausa formal es de 30 minutos para el almuerzo. Todas las operarias son mujeres.
Trabajo repetitivo: El trabajo requiere repetir continuamente los mismos gestos en las mismas posturas y con los mismos esfuerzos. En el torno se procesan 150 ejes por hora. El ciclo de trabajo dura 10 minutos, tiempo necesario para procesar una barra y de cada barra se obtienen 30 ejes. De manera que cada micro ciclo tiene una duración de 20 segundos para cada eje. En una jornada de ocho horas se procesan unos 1200 ejes aproximadamente. Los operadores consideran que el volumen de producción es exigente sobre todo por las limitaciones de las máquinas. En cuanto a la repetitividad se considera altamente repetitivo. Las trabajadoras hacen micro pausas cada vez que finaliza una barra.
Manipulación de cargas: Las trabajadoras ven con dificultad cargar las barras. El peso de cada barra es de 1,5 Kgs. para los ejes de REV y de 3,7 Kgs. para los ejes de RAC, ellas transportan este material entre dos operarias y en ocasiones reciben ayuda de los compañeros masculinos.
La adecuación del trabajo: El trabajo requiere estar todo el tiempo de pie, no cuentan con la posibilidad de sentarse. Área de trabajo horizontal ó distancia desde la línea media del cuerpo a donde coloca las manos para trabajar es adecuada. La zona usual de trabajo esta ubicada a unos 35 cm. y la charola esta ubicada a unos 65 cm.
El área de trabajo vertical es adecuada, tomando como referencia la altura del codo de las trabajadoras.
En el torno Nº 6 se presentan dificultades, la operaria mantiene el brazo derecho extendido hacia el frente dentro del torno para recibir los ejes, debido a dificultades del equipo: los ejes salen muy rápido, la viruta hace que se enrede el segundo eje y esto puede romper las cuchillas del torno. Situación que obliga a la trabajadora adoptar esta postura incomoda a una altura de trabajo de 128 cm.
La distancia visual es de 98 cm se considera que es adecuada.
El ángulo visual varía entre 15º habitualmente y 45º al momento de realizar la lectura del micrómetro, siendo ambos casos adecuados
En cuanto al espacio disponible para los pies no esta considerado. La máquina llega hasta el piso de forma continua.
Espacio para los pies. Los tornos no tienen espacio libre para los pies
Posturas observadas:
De pie tronco recto ambos pies apoyados en el piso
De pie tronco recto parada en un solo pie y el otro pie en el reposapiés
De pie tronco en flexión moderada (al cargar y colocar las barras en soporte)
De pie tronco recto brazos extendidos (posiciona barra dentro del tubo alimentador) Sentada sobre mesa brazo derecho extendido a la altura del hombro sin soporte De pie brazo derecho extendido a la altura del hombro sin soporte dentro del torno
Desplazamientos observados: Los desplazamientos observados fueron cuando van al baño, a tomar agua o al momento de la pausa.
Estrategias de descanso observadas:
• : Se recuestan o sientan sobre la mesa lateral. Considera que trabajar sentada es incómodo por el poco espacio.
• Paradas en un solo pie, descansan el otro sobre una bovina de plástico improvisada como reposapiés• Cada hora aproximadamente hacen micro pausas van al baño o toman agua.
Foto 15. Trabajadora descansa en un solo pie y usa bobina
Potenciales peligros que puedan generar accidentes:
• El área de trabajo es resbaladiza por la grasa de las máquinas• Las virutas pueden proyectarse fue considerado un riesgo grave• Las cuchillas pueden ocasionar una quemadura siendo un riesgo moderado• La molestia que reporta con mayor frecuencia son contracturas musculares debido a la cargada de barras. Antes cargaban más peso.• No se han reportado ningún accidente
Equipos de Seguridad utilizado• Uniforme• Botas de seguridad• Lentes de seguridad
Los comandos son adecuados y su uso es poco frecuente.
Las Herramientas y el material de trabajo: Las operarias disponen de herramientas para cada operación, los objetos se toman con seguridad y facilidad y su manipulación no causan fatiga de manos y de brazos. El material de trabajo posee elementos como la viruta la cual ocasiona pequeñas cortaduras en las manos. El material de trabajo esta ubicado cerca del área.
Los trabajadores manifiestan que el mantenimiento de las máquinas es necesario hacer con mayor regularidad para garantizar un mejor desempeño.
Utilizan como herramientas: Micrómetro, reloj de comparación, barras, llaves y la caja del vernier.
La iluminación general se considera adecuada para el tipo de trabajo que se realiza. La luz natural entra por los ventanales del galpón. Es necesario que les hagan mantenimiento más frecuente de las luminarias.
Ruido en el área de trabajo, procede de áreas vecinas. Pero no ocasiona molestia a los trabajadores, los cuales pueden comunicarse sin dificultades.
La temperatura es la ambiental. Cuentan con ventiladores en cada puesto de trabajo. La vestimenta utilizada por los trabajadores es liviana de color azul oscuro. Las operarias consideran que el calor es molesto.
El aire esta viciado se siente al ingresar al galpón. Se utiliza la Taladrina la cual es un fluido de corte de composición compleja que se adiciona pieza-herramienta- viruta de una operación de mecanizado, afín de lubricar y eliminar el calor producido. Este producto puede ocasionar afecciones de la piel, alteraciones en el tracto respiratorio y se ha descrito cáncer. Pueden contener cromo. Son sensibilizantes causan alergias.
Las relaciones de trabajo entre operarios: Hay buen entendimiento, colaboración y clima social son buenos entre los trabajadores y los superiores. Los trabajadores establecen los contactos que juzguen necesarios con otros servicios.
El ambiente social local y general: Los operarios pueden hablar libremente cuando lo desean. Ellos pueden modificar su ritmo de trabajo y dejar el puesto sin perjudicar la producción. Los sitios para la recreación, salones y comedor son considerados adecuados.
El contenido del trabajo: El trabajador es responsable de una operación o tarea simple únicamente. Están claramente definidas sus tareas, su rol y los limites de sus responsabilidades. No puede modificar su trabajo. El tiempo de entrenamiento requerido al inicio de este trabajo en el torno es de un mes.
El ambiente psicosocial: Los operarios consideran que deberían ganar mejor sueldo. Trabajan horas extras por la necesidad de aumentar sus ingresos. Los trabajadores saben como es evaluado y controlado su trabajo.
Gráfico Nº 4. Síntesis de la evaluación de la línea de Ejes. Área de Metalmecánica.
Empresa de Motores eléctricos. Aragua, Agosto 2007
LINEA DE EJES
1. Área de trabajo.
2.- Organización técnica entre los puestos3.- Las adecuaciones del trabajo4.- Riesgos de accidentes
5.- Los comandos y señales
6.- Las herramientas y material de trabajo7.- El trabajo repetitivo
8.- Las manipulaciones
9.- la carga mental 10.- La iluminación11.- El ruido
12.- Los ambientes térmicos
13.- Los riesgos químicos y biológicos14.- Las vibraciones
15.- Las relaciones de trabajo entre operarios16.- El ambiente social local y general17.- El contenido de trabajo
18.- El ambiente psicosocial
19.- Zonas de dolor en el cuerpo al final de la jornada de trabajo
Síntesis de las propuestas de solución planteadas por los trabajadores y trabajadoras en la aplicación del método DEPARIS modificado en los 27 puestos de trabajo.
En cuanto a la organización del trabajo
Del estudio realizado se pudo observar la existencia de problemas relacionados con la organización de la producción, especialmente en lo relacionado con el manejo de materiales y la provisión y disposición de los componentes, insumos y productos de cada una de las etapas. En ese sentido se considera conveniente la implementación de las siguientes medida:
• Incorporar un trabajador “pie de línea” en aquellas áreas donde se congestionan de material, para facilitar la movilización y flujo de materiales e insumos.
• Evaluar la actual disposición de maquinarias y equipos a los fines de dar mejor organización y coherencia a la estructura del proceso productivo. Se recomienda evaluar el actual layout e introducir cambios que faciliten el flujo de materiales.
• Es necesario introducir modificaciones en los sistemas de almacenamiento de partes e insumos. En la actualidad se discute una norma sobre manejo de materiales y levantamiento de cargas orientada a limitar la carga máxima a ser manipulada por trabajador. En tal sentido se recomienda estudiar la reducción del tamaño de cestas y canastos y el mejoramiento de los sistemas de traslado y movilización de pesos.
• Uno de los elementos que resaltan de la observación del proceso se refiere a las fallas presentes en los equipos (fugas de aceite, pérdida de presión, etc.) que contribuyen a incrementar el disconfort y la fatiga del personal. Es necesario establecer una política de mantenimiento preventivo y correctivo para los equipos y maquinarias.
• Por las características del proceso productivo es difícil implementar medidas organizativas orientadas a la rotación de puestos de trabajo debido a que la mayoría de ellos presentan la misma situación de trabajo repetitivo. En tal sentido es conveniente la implementación de un programa de pausas con ejercicios dirigidos que permitan contrarrestar el efecto del trabajo repetitivo.
• Se recomienda hacer énfasis en la educación de los trabajadores en el campo de la salud laboral para desarrolla una cultura de la prevención que facilite la incorporación activa de los trabajadores y trabajadoras a las estrategias que desde la empresa se implementen para minimizar los efectos del trabajo sobre la salud de los trabajadores.
• Fortalecer la formación de los Delegados de Prevención como una estrategia orientada a crear condiciones de que permitan un espacio de diálogo productivo entre los actores sociales.
• Enfatizar en el uso y conservación de los recursos disponibles para la protección individual en los puestos que así lo requieran.
• Vigilar desde el punto de vista médico los trabajadores expuestos a fluidos refrigerantes (taladrina), haciendo énfasis en la evaluación de su función respiratoria y dérmica. Igualmente establecer normas y procedimientos, así como políticas educativas e informativas orientadas a evitar el contacto de los trabajadores con este tipo de sustancia.
• Mejorar la vigilancia en el comedor y en los lockers de los trabajadores para evitar hurtos.
• Fortalecer las políticas de la empresa en relación al uso del tiempo libre, la recreación, el deporte, la cultura y el turismo social en concordancia con las nuevas políticas que se vienen generando desde el Estado.
Medidas en el entorno de trabajo
• Se recomienda la realización de un estudio orientado a lograr un reordenamiento de los espacios disponibles en el área de Metalmecánica que permita una mejor disposición de los espacios de trabajo disponibles según criterios de producción.
• Es necesario hacer una evaluación integral de la contaminación sónica existente en el área de producción y de las fuentes generadoras de ruido.
• Relacionado con el aparte anterior, se recomienda estudiar la posibilidad de cambiar la técnica de limpieza de las tapas (proceso de soplado) por un mecanismo de eliminación de virutas mediante contacto con superficies acolchadas (felpeado) o reubicar el puesto de soplado en áreas externas para evitar contaminación de ruido.
• En el área de fundición se recomienda mejorar el confort térmico colocando extractores al fondo del galpón que permitan la descarga del calor generado por los hornos hacia el exterior. De igual manera se puede implementar un sistema de inyección de aire fresco al lugar de trabajo.
• Revisar las normas y medidas para el uso, manejo y disposición final de la taladrina a fin de garantizar el cumplimiento de las normas ambientales (evitar su disposición al sistema de aguas servidas municipal).
• Colocar ayudas mecánicas para el manejo de materiales (grúas, transportadores, carros, etc.) para el levantamiento de cargas, trasporte y disposición de insumos y partes en los puestos de trabajo.
Medidas en relación a los equipos de trabajo
• Medidas para mejorar las exigencias de las posturas Postura sentada
La postura sentada es la posición de trabajo más confortable, ya que ayuda a reducir la fatiga corporal, disminuye el gasto de energía e incrementa la estabilidad y la precisión en las acciones desarrolladas. Sin embargo, esta postura también puede resultar perjudicial para la salud si no se tienen en cuenta los elementos que intervienen en la realización del trabajo, principalmente, la silla y la mesa o el plano de trabajo y si no se dispone de la posibilidad de cambiar de posición de vez en cuando. Las consecuencias de mantener una postura de trabajo sentada inadecuada son: molestias cervicales, abdominales, trastornos en la zona lumbar de la espalda y alteraciones del sistema circulatorio y nervioso que afectan, principalmente, a las piernas. Tanto en actividades del sector servicios como en el industrial muchas personas realizan su trabajo sentadas, por lo que es conveniente considerar los principales requisitos ergonómicos que deben reunir el asiento y el plano de trabajo, con el fin de lograr posturas confortables durante periodos de tiempo más o menos prolongados. Mantener la postura sentada durante mucho tiempo puede llegar a resultar molesto. Por lo tanto, es aconsejable alternar la postura sentada con la de pie y, a ser posible, andar o caminar. Se debe trabajar
En todo puesto de trabajo sentado es necesario considerar espacio disponible para las piernas y pies. Será como mínimo (60 cm de ancho y de 65 a 70 cm de profundidad) (NTP 602, 1997).
Dotación de sillas con las siguientes características
Altura del asiento: regulable para varios usuarios y que permita que los trabajadores(as) queden cómodos respetando la altura de su plano de trabajo en la máquina. La posición de los muslos con respecto al cuerpo debe permitir un ángulo entre 90 y 110 grados. Idealmente la altura debe permitir que los pies queden apoyados en el piso. El borde delantero del asiento debe ser redondeado.
Respaldo de la silla: debe ser regulable en altura e inclinación, debe disponer de un almohadillado en la zona lumbar. Se recomienda que como mínimo, el respaldar debe llegar a la altura de la parte media de la espalda por debajo de los omoplatos y deber ser ancho en su parte superior para no restar movilidad a los brazos.
Base de la silla: debe ser de cinco (5) patas para garantizar la estabilidad. Que puedan girar sobre su eje vertical en aquellos puestos que así lo requieran.
Mandos y controles: se deben poder manipular con facilidad mientras la persona esta sentada.
Material de revestimiento: transpirable, acolchado (20 mm) como mínimo.
Postura de pie
En aquellos puestos de trabajo que los operarios permanecen de pie se recomienda que el operario u operaria tenga la posibilidad de alternar la postura de pie y la postura sentada. En tal sentido se deben colocar bancos o reposa nalgas retráctiles en los puestos que no permitan el uso de sillas.
Se recomienda dotar de alfombras ergonómicas relajantes en la superficie de trabajo del operador(a) para evitar la fatiga de las extremidades inferiores.
Para los trabajadores que deben realizar la actividad de pie se recomienda la dotación de reposapiés de manera que los trabajadores puedan alternar la postura y la superficie de apoyo a fin de disminuir el impacto de la bipedestación prolongada.
Es conveniente el uso de plataformas en aquellos puestos que requieran mejorar la altura de trabajo de los usuarios. Se recomienda preferiblemente usar madera en la superficie de desplazamiento siempre que la estructura de la misma sea segura y suficientemente fuerte para evitar accidentes.
Ejercicios de relajación
Se recomienda la realización ejercicios de relajación y estiramiento de los músculos durante las pausas orientados a los grupos musculares comprometidos por las características de la actividad laboral.
Mejorar la calidad de las cestas y canastos. Se sugiere que sean más pequeñas de manera de garantizar que los trabajadores(as) manipulen menor peso. Esto permitirá tomar medidas ya que pronto entrará en vigencia una Norma Técnica que limitará el peso máximo a levantar.
Ayudas mecánicas para el levantamiento de cargas, utilizar adecuadamente las mesas de riel. O traspaletas para transportar materiales.
Los carritos de transporte de materiales es necesario dar mantenimiento a las ruedas
Colocar brazos articulados dispensadores en aquellos puestos que utilizan piezas pequeñas, con el objeto de ubicar los mismos en la zona óptima de trabajo al frente del trabajador y evitar que los materiales de trabajo queden colocados atrás a espalda de los trabajadores(as).
Superficies de trabajo
En la mayoría de los puestos de trabajo se utilizan mesas y superficies anexas a las máquinas las cuales disponen de muy poco espacio de trabajo en el plano horizontal. Se sugiere evaluar la posibilidad de mejorar esta situación con un rediseño de las superficies auxiliares que cumplan con las siguientes características:
a) estructura de soporte de las superficies que no limiten la movilidad de laspiernas y b) altura y ubicación que permitan el fácil acceso para tomar y colocar las piezas y partes.
Vigilancia de los accidentes e incidentes de trabajo
El área de metalmecánica es una de las que tiene mayor número de accidentes en la empresa. Es necesario estudiar cada accidente, tomar las medidas correctivas para evitar nuevos problemas.
CONCLUSIONES
Los puestos de trabajo evaluados presentan serios problemas de diseño, organización del trabajo, manejo manual de materiales en forma inadecuada los cuales es necesario corregir. Todos los trabajadores presentan problemas músculo esquelético a predominio de los miembros superiores y la espalda. Debido a los problemas detectados se explica el incremento de accidentes de trabajo.
La participación de los y las trabajadoras en el diagnóstico de sus condiciones de trabajo permitió obtener un conjunto de propuestas de solución las cuales han permitido a la empresa realizar modificaciones en los puestos de trabajo.
Los Delegados y Delegadas de Prevención con la metodología utilizada podrán ejercer el control social y hacer seguimiento y re-evaluación de las áreas una vez realizadas las modificaciones por parte de la empresa.
El método utilizado ha permitido que la empresa organice su respuesta a losproblemas encontrados a través de la puesta en práctica de un plan de acción y ha facilitado la discusión con los trabajadores de las soluciones propuestas.
AGRADECIMIENTOS
Agradecemos sinceramente al apoyo financiero recibido por parte de la empresa en el marco de los proyectos LOCTI, el Centro de Estudios en Salud de los Trabajadores de la Universidad de Carabobo y a los trabajadores por su constante apoyo hacia esta investigación.
REFERENCIAS
- 1. Sperandio, J.C. L’ergonomie du travail mental. 2 edition, Paris Masson. 1988. p.137.
- 2. Plaisanti, M. et Teiger, C. La lutte des travailleuses de la féderation HACUI TEXCFDT. Les contarintes du travail dans les travaux répeétitifs de masse et leurs conséquences sur les travailleuses. In Les effects des conditions de travail sur la santé des travailleuses: Actes du colloque organisé par le Comité de condition féminine de la CSN et parriné para le Bureau Internacional du travail (BIT) du 15 au 21 mai 1983 á l’Université du Québec á Montreal: CSN. Montreal. P.3367.
- 3. Leplat, J. L’analyse psychologique du travail. In Leplat J. La psychologie ergonomique. P.24.50. Presses Universitaires de France. 1980.
- 4. Kilbom, A. Measurement and assessment of dynamic work. In Wilson J.R. et al. Evaluation of Human Work. P. 520541. London. Washington DC. Taylor & Francis. 1992.
- 5. Leplat J. Perpectivas méthodologiques por l’étude des activités mentales. In Gaussin J. et Van Laethem A. L?Ergonomia des activités mentales. P. 6270. LauvainLa Neuve. Ed. Cabai. 1982.
- 6. Welfort A. T. La Charge mentale de travail comme founction des exigentes de la capacité de la stratégie et de l’habilité. In Jacques Leplat. L’analyse du travail en psychologie ergonomique. Tome I. ToulouseFrance, OCTARES ëditions. 1992. p.121145.
- 7. Montmollin M. Vocabulaire de l’ergonomie. Toulouse. Collection travail Premiére édition. OCTARES ëditions. 1995. p. 52 y 53.
- 8. Vecina N et al. 1992. Pour donner un sens au travail. Bilan et orientations du Québec en santé mentale au travail. Le Comité de la santé mentale du Québec. Québec. Gaetan Morin éditor p.32).
- 9. Messing K. Pour la reconnissance du caracteré punible des emplois des femmes. Recherche Féministes, Vol 4(1)1991:87102.
- 10. Pezet V., Villatte R., Logeay P. Usure professionnelle des travailleurs sociaux et rôles de l’équipe éducative. In Six F. et Vaxevanoglou X. Les acpects colletifs du travail. P.157171. Tolouse. Octares ëdition. 1993
- 11. Guérin, F., Lavilla, A., Daniellou, F. et al. Comprende le travail pour le transformer la practique de l’ergonomie. Ed. ANACT. 1991.
- 12. Teiger C. 1993. "L'approche ergonomique: du travail humain à l'activité des hommes et des femmes au travail. Education permanente, Nº 1163, p. 7296
- 13. Escalona E, Yonnusg M, González R, Chatygny C, Seifert AM. LA ERGONOMIA COMO HERRAMIENTA PARA TRABAJADORAS Y TRABAJADORES. 1ra Ed. Valencia: Ediciones Universidad de Carabobo; 2002.
- 14. Malchaire J. 2002. Diagnóstico participativo de riesgos profesionales en una situación de trabajo: Método DEPARIS. [citado el 09 de Julio de 2007]Disponible en http://www.md.ucl.ac.be/hytr/new/Download/presentacion_deparis.pdf
Papers relacionados
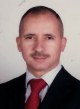

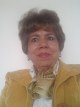
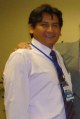

