Lind, Salla
Human-Machine Systems / VTT Technical Research Centre of Finland / Tekniikankatu 1, FI-33101 / Tampere / Finland+358 20 722 3004 / salla.lind@vtt.fiLeino, Simo-PekkaHuman-Machine Systems / VTT Technical Research Centre of Finland / Tekniikankatu 1, FI-33101 / Tampere / Finland+358 20 722 3759 / simo-pekka.leino@vtt.fi
Viitaniemi, Juhani
Human-Machine Systems / VTT Technical Research Centre of Finland / Tekniikankatu 1, FI-33101 / Tampere / Finland+358 20 722 3221 / juhani.viitaniemi@vtt.fiHelin, KajHuman-Machine Systems / VTT Technical Research Centre of Finland / Tekniikankatu 1, FI-33101 / Tampere / Finland+358 20 722 3769 / kaj.helin@vtt.fiMultanen, PetteriDepartment of Intelligent Hydraulics and Automation (IHA) / Tampere University of Technology / P.O. Box 589 FI-33101 / Tampere / Finland+358 50 599 4329 / petteri.multanen@tut.fi
Mäkiranta, Ari
Department of Intelligent Hydraulics and Automation (IHA) / Tampere University of Technology / P.O. Box 589 FI-33101 / Tampere / Finland+358 50 349 8654 / ari.makiranta@tut.fi
Heikkilä, Juhamatti
Metso Minerals Oy / Construction Business Line Technology Development / P.O.Box 306 FI-33101 / Tampere / Finland+ 358 40 774 9272 / juhamatti.heikkila@metso.com
ABSTRACT
ABSTRACT
Demands for maintaining and restoring process reliability reflect to industrial maintenance operations, which must be executed correctly and efficiently. More complicated machinery and subcontracting maintenance services rise new challenges for occupational safety, as maintenance workers must deal with varying operations and changing customer sites. To ensure occupational safety in maintenance operations, efficient training and instructing methods are required. For training such risky operations, virtual environments provide an effective and safe option. The article describes the setting of the virtual environment and its connections to product and production processes. In addition, a set of supportive analysis methods are proposed.
Keywords
Keywords
Maintenance, maintainability, virtual environment
INTRODUCTION
INTRODUCTION
The importance of service business is growing in companies. Companies want to provide after-sales services for their customers buying their products. Meanwhile, global markets and demands for shortening time-to-market are challenging for the companies. Machine maintenance (further: maintenance) is one form of industrial services and has different aims, such as ensuring machine reliability and restoring normal condition in case of disturbances and malfunctions. Maintenance has many indirect effects, such as supporting economical efficiency of production and ensuring that production is safe for persons and environment.
Due to different workplace factors, maintenance operations include a variety of safety risks that may cause harm to the maintenance workers. Such risks are caused by, for example, working in close contact with machinery, changing work sites and working alone and/or at night on duty [16]. In addition, pressure of time can increase the existing risks and create some new ones, e.g. due to increased risk-taking. From management’s viewpoint, the urgency and scheduling with customers, unscheduled downtime and renovation, the increasing level of automation, and the competence and training of personnel may be difficult to manage.
In contrast to many other areas of technology and industry, the direct contact between the operator and machine in maintenance activities cannot be reduced substantially. Typically, distancing people from processes diminishes the likelihood of the occurrence of human errors and other chains of events that can lead to accidents. Maintenance is, and probably always will be, that area in the use of technology where humans will be in direct contact with processes [26]. Maintenance is also a good example of work that is performed in exceptional conditions, such as the time of day, especially when high-priority repairs are involved (c.f. [21]). A maintenance operation may also be exceptional work in itself, depending on the frequency with which it is performed. Maintenance operations typically include both assembly and disassembly, in addition to preparation tasks and resetting to normal use, which may increase the number of injury risks. Subcontracting maintenance services, which is currently becoming more and more typical, may also raise new challenges. [16]
The scope and aim of this article
A study has been launched in 2006 with aim to develop a virtual environment for planning and training maintenance operations. The study will be completed by 2009, when a comprehensive generic method for virtual design, planning and training is introduced. The study is executed in cooperation with VTT, IHA, and industrial partners. The study will produce a comprehensive methodology (VIRVO concept) that includes a virtual environment (VE) for maintenance trainingand a set of analysis methods to support maintainability and safety design in machine design. The novelty is in ways efficiently integrating detailed task planning to the product design.
The aim of this article is to 1) present the VIRVO concept for planning and training maintenance operations in a VE, and 2) define what kind of analysis methods could be included to support maintenance planning and training with aim to promote maintenance safety.
BACKGROUND
Maintenance and safety
In general, studies on maintenance-related risks have been examined from two different viewpoints: 1) human performance as a risk to the maintained process (reliability-based approach), and 2) maintenance operations as a risk to humans (safety-based approach) [15]. The first group includes studies that have concentrated on post-maintenance safety and reliability (e.g. [8], [9], [24], [38], [39], [40]). A finding whereby a significant proportion of equipment failures occur shortly after a maintenance operation [27] supports this approach.
The second group of studies examines maintenance operations as a risk to maintenance workers. Maintenance is often identified as a risky operation from the perspective of occupational safety (e.g. [11], [13], [16], [26], [35]). Both the management and the physical working conditions play important roles in developing safety in risky environments (e.g. [25], [30], [44]). Maintenance can be considered to include the same occupational risks as other operations in industrial working environments, but also boosts some certain specific risks. Such maintenance- related risk factors (e.g. working alone or during nights) especially arise from the need for urgent repairs and disturbance controls. Other typical risk factors are, for example, frequency of tasks, lack of tidiness and order of the working environment, as well as defects in the equipment and tools [16]. These factors can also increase the risk of human error [27], although they are often considered to increase the probability of any occupational accident.
Maintainability
Maintainability design aims to enable easy and cost-efficient maintenance and repair work [31]. Easiness and costs of maintenance depend on system architecture, maintenance organisation and spare parts availability. To ensure new product’s maintainability it is essential that maintenance tasks can be evaluated during the product development process in order to 1) ensure safety and 2) provide the necessary information e.g. to instructions. [42] Latest development of 3DCAD and PLM (Product Lifecycle Management) systems has provided better tools for engineering. However, it may be challenging for the designer to detect all possible maintenance-related problems or hazards by on computer screen. Virtual engineering tools, i.e. augmented reality (AR), digital human models (DHM), and VEs, can improve the situation significantly. There is also a need for a systematic maintenance operation planning method that can be applied during the product development process.
Virtual environments in safety promotion
Virtual engineering tools
Virtual engineering tools provide new possibilities for safety promotion. The soft- and hardware are developing fast and they are getting more affordable and typical in companies (see e.g., [4], [41], [20], [6], [7]).
AR is an environment that includes both virtual reality and real-world elements. Thus, an AR user can see the real world, as well as computer-generated images projected to that world. Azuma [1] defines an AR system as one that 1) combines real and virtual, 2) is interactive in real-time, and 3) is registered in threedimensions. An application for AR is utilising them in the safe development of autonomous machines. Picture 1 presents a test site of IHA where a group of real work machines operating autonomously is extended with a simulated machine. The simulated machine is using real control system and its operation is based on real- time simulation. The visualisation of machine is augmented to the display of remote control room. The system enables the safe development and testing of control algorithms for the movements and navigation of machines without the risk of collisions and material failures.
Picture 1. Augmented and simulated machine as a part of autonomous group of work machines. [18]
DHMs are essential tools when designing tasks that base mostly on human actions. Human models illustrate the human actions in virtual environment with complex kinetics and kinematics (Picture 2). The dimensions and main postures can be tested with simple digital models, whereas highly detailed models enable, for example, versatile ergonomics and comfort analyses of a worker.
Picture 2. Digital human models performing maintenance work. [49], [48]
A VE system consists of pieces of software, virtual models, data communication, computers, display devices, user interface devices, other devices and their drivers, depending on the purposes and applications. Hardware determinates the applicable software that can be utilised and vice versa. Computers require sufficient computing power to calculate complicated simulations and 3D graphics.
One of the biggest advantages of VEs is using them in different kinds of design inspections and planning. Even using large-scale normal visualisation helps a lot in understanding design contents compared to 2D drawings and desktop display. Understanding will be even better when using immersive stereo visualisation environments. A three-dimensional virtual system it is much easier to perceive, when it can be observed in its natural size. It is also possible to change position in a VE and to make kinematics and dynamic simulations. Recently, VEs have been successfully applied in risk assessments (see e.g. [36], [12], [19], [28], [7]).
Task training in virtual environments
A task has a set of constraints formed by organisational, technological and environmental factors. Thus, a task has components of requirements, environment and behaviour. [32] Task training can be considered as systematic modification of knowledge, skills, attitudes and behaviour through instruction, practice, measurement and feedback. [47] Building a training simulator requires expertise about many disciplines: modelling, programming, engineering, ergonomics, workers, etc. It is essential to integrate both technical and human factors training in order to reach good results. [47]
The training simulator should be accurate both technically and psychologically. Technical accuracy means how realistic is the simulation of machine and equipments. Psychological accuracy is the degree how training tasks reproduce actual behaviours that are required for the work task. Need of technical accuracy varies depending on trained task. In some case, very immersive simulators are needed, whereas in some cases low physical accuracy is enough. Most important is to have psychological accuracy in sufficient level, as the goal of training is in advancing attitudes, knowledge and skills for the task execution. In the case of maintenance, the simulator must be accurate also physically as the worker has to train also physical skills, like using mechanical tools and devices. Training a demanding task requires good understanding about special characteristics of trained tasks and environment. [47]
Maintenance training may include, for example, instructors, multimedia and training simulators i.e. virtual environment simulation of the work task and work place. Training style in a simulator can be representative, illustrative, advising or informal. It depends on situation, which one is the most efficient one. In many cases, best option is to proceed systematically from representative style to informal style. In maintenance training, it is typical to have much hands-on type of informal training. [47] Task training focuses on rehearsing each task sequence individually and together. The aim is 1) to achieve task phase’s fluent performance, 2) to understand aspects of user control and error handling, 3) to create correct mental model of the task operation as whole, and 4) to become able to apply learned details. [37], [45]
Use of a VE in maintenance planning and training
For the maintenance personnel, VEs enable design for maintenance through virtual prototyping, as well as comprehensive safety planning in different working environments. In addition to task- and machine-specific risk assessments, VEs enable operations training in a safe environment. A group of publications examine use of VEs in safety training in different industrial work tasks (see e.g. [2], [10], [14], [23], [34], [46]). If either the maintenance task and/or the working environment are especially challenging, training in VE provides the following, specific benefits [45]:
- 1. Time saving: Challenging work tasks may require long training, in order to acquire needed routines and coordination. A VE provides a possibility to train the tasks also in unusual conditions.
- 2. Avoiding production disturbances and achieving economical savings: Production is undisturbed, if maintenance operations are trained using a VE. This leads to economical savings.
- 3. Safety during training: Workers lack of experience does not cause
real risks to humans and/or the production environment.
Finally, for promoting maintenance safety and machine maintainability, it would be beneficial to make the maintenance workers participate in work task planning already in the product design phase, for example through development group working. Using development groups is most efficient when they focus on a certain work task and work environment design, for example, layout design of worker’s workplace or a machine’s maintainability design. A VE enables product’s maintainability and safety assessment already in the designing phase. Themaintenance information can also be linked to a company’s PLM (product lifecycle management) system, which enables transferring knowledge from experts to end users through simulations (e.g. [42], [5], [43], [22]).
METHODS
Methods
A literature review was conducted regarding virtual engineering in the planning and training of maintenance and manual work tasks in the field of mechanical engineering. The review covered various technical scientific databases and Internet. In addition, feasible soft- and hardware were charted with aim to find the best solutions for maintenance training.
Information was gathered from industrial partners with aim to determine the type of the service business and maintenance work. The goal was to define how maintenance work tasks are planned, documented, trained and guided as well as how the requirements of such work are taken into account in machine engineering and design. The needs and requirements for developing planning, design, documentation and guidance methods were also determined.
Industrial test case
The VIRVO concept will be implemented in an industrial test case focusing on maintenance and maintainability design of Metso Minerals’ rock crushers (Picture 3). The test case has been used to verify that the scope and feasibility of the VIRVO concept are appropriate. Rock crushing, screening and conveying equipment is used in a very demanding environment. Rock dust, vibration and outdoor weather conditions are likely to reduce the lifetime of structures and components. Thereby both preventive and corrective maintenance work is needed.
Picture 3. Sectional virtual view of Metso Minerals GP-Series Cone Crusher.
In practice all maintenance tasks are performed manually by one or two workers. During the study, combinations of virtual techniques and analytical methods have been tested in different types of maintenance tasks of rock crushers.
RESULTS
A concept for utilising VE in maintenance task planning
Based on the findings in literature and companies, the structure of the VIRVO concept is proposed (Figure 1). The concept has three main levels 1) links to production management, 2) the analysis procedure, and 3) supportive tools and methods.
Figure 1. The structure of VIRVO concept.
The concept connects production and product information, as well as task planning and maintainability design. It enables maintenance safety planning already in the prototyping phase, as the CAD-models and production information can be applied in a VE or an AR application. Connections to the product data management (PDM) and product lifecycle management (PLM) systems enable automated generation and updating of maintenance materials and instructions.
Currently, the biggest challenges relate to data converting and harmonisation, as the data can be retrieved to the PLM system from different kinds of data sources, and vice versa (e.g. CAD files, reliability data, maintenance materials). The actual maintenance task planning consists of seven phases, as described in the following sub-chapters.
Initial data
Initial data creation in ideal situation starts when product conceptual modelling and system modelling are in progress. At the latest initial data is created when the chosen critical maintenance tasks are analysed and designed in detail. It is essential to recognise the most critical work task for training in virtual simulators, as time and demands for economical efficiency limit training all tasks virtually. Critical tasks can be, for example, tasks that involve high occupational risks and tasks requiring machines to be long out of profitable production.
The tasks can be chosen from the machine’s maintenance program or using maintainability analyses and indexes (e.g. [29]; see also [33]). Initial data can also be gathered during the early phases of product development process and from product data management system. In addition, usability surveys enable gathering valuable information from the end users of the product.
Task modelling
The work task, and the working environment, is first modelled conceptually using simple flowcharts. The modelling has two aims, firstly to create a basis for input for virtual modelling of the system, and secondly to assess the degree of tasks criticalness. When necessary, flowchart is defined more precisely and descriptions can be used to clarify the plan. This “paper-model” includes needed information about work sequences, tools, spare parts, materials and personnel.
The maintenance work task is first modelled as a basic flowchart. The chart is expanded with several additional levels, where the needed resources, instructions and safety regulations are defined. This flowchart model is the basis for the VE, training simulators and work guidance material. The flowchart is Master Model of the maintenance design documents. Master Model is stored in a database (e.g. PDM-system) and engineering tools refer to it. Changes or comments in the VE or in a work place are updated also in the Master Model. The connection between the VIRVO concept and the information management tools are illustrated in Figure 2.
Figure 2. Product Lifecycle Management using the VIRVO concept.
Virtual modelling
In the VIRVO concept, machine design and maintenance planning are made concurrently. 3D CAD models, created in machine design phase, are utilised already during conceptual task modelling. Their role is emphasised when building the VE and making the detailed work task planning. The models are updated in real time and they are maintained in a PDM system.
Task planning
Maintenance tasks should be designed and planned in the earliest possible phase of product development, when it is still possible to make changes in machine and system design. Low-level maintenance planning can be made in desktop 3D
CAD environment. The more detailed critical tasks need profound planning exploiting different kinds of VEs. A set of supportive analysis methods, including a method for task planning, will be included in the VIRVO concept.
Plan inspection
After the virtual modelling, the task plan is inspected in a development group where workers, designers, experts and management are represented. This ensures that all required knowledge and information is available during design and planning. In addition, usability, ergonomics and safety have to be assessed.
Task training
The training simulator consists of 3D models, virtual environments and instructions created in machine design and maintenance planning phases. The training programme is built on models (i.e. flowcharts) describing the procedures of the work task. There are certain requirements for the training simulator, for example, it has to be realistic and immersive in order to reach good results in training, and it has to be updated easily. The VE in the VIRVO concept is adjustable, enabling training of different tasks in different kinds of working environments.
Documentation and guidance
Producing maintenance materials (documentation and guidance material) is challenging, as the content has to be generated easily and cost-effective. It is possible to re-use for example 3D-models and animations created earlier in product lifecycle and product development process.
In the VIRVO concept, the automated generation and updating of a VE and the maintenance materials is enabled through virtual simulation software reading the data from the database during VE generation. For example, if something is changed in a CAD model, it will be updated automatically in virtual environment and vice versa. The tool is based on Microsoft Excel software, but there are also alternative products available. Virtual environments in e.g. Virtools have been constructed in such a way that the design system can import the designed work sequence from the Master Model database (e.g. in Excel). End user or designer can evaluate and redesign task in virtual environment without doing any modification and coding in VE.
Supportive tools and methods
To promote safety in an effective way, the VIRVO concept can be fulfilled with relevant analyses taking into account safety management, technical issues and worker’s role in maintenance safety promotion. Therefore, relevant analyses can include maintainability, risk, and work task analyses. The following chapters list some examples of fulfilling methods, which should be chosen task-specifically.
Maintainability analyses
Maintainability design should pay attention, among others, to fault identification, part reaching, part extracting/fastening and moving. Most common and repeated maintenance tasks should be designed to be conducted with changing subsystems. Design engineers should consider how machines and systems will be maintained taking into account the varying conditions on sites. As the human cognitive and physical capacity can also vary, good maintainability promotes also safety. Machine maintainability is considered in certain standards, such as SFS-IEC 50-191 [31] and SAE J817-2 [29]. Maintainability can also be analysed with certain indexes, as described in e.g. SAE J817-2 [29] and Bretby maintainability index (see e.g. [3], [33]).
Risk analyses
In maintenance safety management, it is essential to take into account management, technical and workplace factors, as well as the worker’s role. Specific features in maintenance are the varying conditions between tasks and sites [17]. In VIRVO concept, the risk analyses fulfil task and maintainability analyses. Risk analyses, paying attention risks rising from the task, workplace or management, indicate also the problems needing special attention in maintenance management. Relevant risk analyses in the VIRVO concept are, for example, FMEA (Failure Mode and Effect Analysis) and FTA (Fault Tree Analysis), which are typically applied to gather more detailed information about the functions, modules and components. The worker’s role can be examined with e.g. Work Safety Analysis (WSA).
Work task analyses
Work task analyses can support and complement safety and maintainability analyses. In the VIRVO concept, applicable analysis methods are, for example, HTA (Hierarchical Task Analysis) which is applicable to human-machine interaction/interface design and for training design. GOMS (Goals, Operators, Methods, and Selection Rules) and CTA (Cognitive Task Analysis) apply interaction/interface design to more complex cognitive tasks design, whereas link analysis applies to workspace design and to workload assessment [32]. Depending on the case, the specific methods used in task analysis process (data collection, task description, data analysis) can apply participatory approach and work process modelling. They can be supported with ergonomics, usability and safety analysis methods, as well as methods exploiting digital human modelling and motion capture (e.g. [20], [6]).
CONCLUSIONS
Maintenance operations can include several occupational risks. Meanwhile, digital engineering tools are developing and getting more typical and affordable for companies. Among other virtual engineering tools, virtual environments can be applied in task, risk and maintainability analyses in the early stage of machine design. In addition, VEs have certain benefits, such as virtual prototyping of new products and safe and cost-efficient training of tasks.
This article proposed a VIRVO concept for designing and training maintenance tasks. The concept connects product and PLM data and exploits user experiences. The concept includes task planning and training in a VE, which is updated through the database combining different types of data. The VIRVO concept and the introduced VE system are suitable for companies’ independent use, as they update automatically and there is no need to re-code the VE. The concept can be fulfilled with additional analyses, such as maintainability, risk and task analyses. The usability and feasibility for companies have been verified with industrial case studies.
REFERENCES
- 1. Azuma, Ronald T. (1997) A survey of augmented reality. Presence: Teleoperators and Virtual Environments (6) 4, 355–385.
- 2. Caird, J.K. (1996). Persistent issues in the application of virtual environment systems to training. In Proceedings of Third Annual Symposium on Human Interaction with Complex Systems (pp. 124132). Los Alamitos, California.
- 3. Desai, A. & Mital, A. (2006) Design for maintenance: basic concepts and review of literature. International Journal of Product Development, (3) 1, 77121
- 4. Flaig, T. (1998) Virtual environment for education and training in safety engineering and maintenance. In Proceedings of Virtual Environments ’98 (pp. 270278). Stuttgart, Germany.
- 5. Helin, K., Kulmala, I., Viitaniemi, J., Säämänen, A. (2005) Component based simulation A tool for ergonomic and indoor environment estimation. In Proceedings of 6th International Scientific Conference Promoting Occupational Hygiene in Africa and Globally. Pilanesberg, South Africa.
- 6. Helin, K., Evilä, T., Viitaniemi, J., Aromaa, S., Kujala, T., Patel, H., Pakkanen, T., Raisamo, R., Salmenperä, P., Miettinen, J., Kilpeläinen, P., Rannanjärvi, L., and Vähä, P. (2007a) HumanICT New humancentred design method and virtual environments in the design of vehicular working machine interfaces. VTT Working Papers 73, Espoo, Finland.
- 7. Helin, K., Viitaniemi, J., Aromaa, S., Montonen, J., Evilä, T., Leino, SP., and Määttä, T. (2007b) OSKU Digital human model in the participatory design approach A new tool to improve work tasks and workplaces. VTT Working Papers 83, Espoo, Finland.
- 8. Holmgren, M. (2005) Maintenancerelated losses at the Swedish Rail. Journal of Quality in Maintenance Engineering (11) 1, pp. 518.
- 9. Jo, Y.D. and Park, K.S. (2003) Dynamic management of human error to reduce total risk. Journal of Loss Prevention in Process Industries (16) 4, pp. 313321.
- 10. Kashiwa, K., Mitani, T. and Tezuka, T. (1995) Development of machine maintenance training system in virtual environment. In: Proceedings of 4th IEEE International Workshop on Robot and Human Communications ROMAN ’95. Tokyo, Japan.
- 11. Kelly, T. P. and McDermid, J. A. (2001) A systematic approach to safety case maintenance. Reliability Engineering & System Safety (71) 3, pp. 271284.
- 12. Leino, SP. Viitaniemi, J., Aromaa, S. (2002) Human comfort and safety analysis in virtual prototyping. Case: offroad vehicle. In: Proceedings of Digital Human Modeling Conference (pp. 457 – 466). Dusseldorf, Germany: SAE International.
- 13. Lin, L.J. and Cohen, H. H. (1997) Accidents in the trucking industry. International Journal of Industrial Ergonomics (20) 4, pp. 287300.
- 14. Lin, F., Ye, L., Duffy, V.C., & Su, CJ. (2002) Developing virtual environments for industrial training. Information Sciences, (140) 12, pp. 153 170.
- 15. Lind, S. (2004) Human error as a risk factor in maintenancerelated accidents. In: Keskinen E. & Hildebrand R. (Eds.), Proceedings of the 2nd Arctic Mediterranean Post Graduate Workshop on Intelligent Machines and Transport Systems, 1321 March 2004, OuluKirunaNarvik.
- 16. Lind, S. and Nenonen, S. (2008). Occupational risks in industrial maintenance. Journal of Quality in Maintenance Engineering. In press.
- 17. Lind, S., Nenonen, S. and KivistöRahnasto, J. (2008). Safety risk assessment in industrial maintenance. Journal of Quality in Maintenance Engineering. In press.
- 18. Multanen, P., Hyvönen, M., Saarinen, J. and Vilenius, M. (2008). Dynamic realtime simulation of intelligent mobile machines. In: Proceedings of the 27th IASTED International Conference on Modelling, Identification and Control. Innsbruck, Austria.
- 19. Määttä, T. (2003) Virtual environments in machinery safety analysis. VTT Publications 516, Espoo, Finland.
- 20. Määttä, T., Viitaniemi, J., Leino, S.P., Helin, K. and Aromaa, S. (2003) Virtual environment based procedure for production task evaluation and design. In: Proceedings of 8th International Federation of Automatic Control Symposium (pp. 203208). Chalmers University of Technology, Gothenburg.
- 21. Nag, P. K. and Patel, V. G. (1998) Work accidents among shiftworkers in industry. International Journal of Industrial Ergonomics (21) 3, pp. 275281.
- 22. Niemelä, R., Koskela, H., Hongisto, V., Sandberg, E., Halonen, L., Lehtovaara, J., Norvasuo, M., Tuomaala, P., and Viitaniemi, J. (2007) Virtual room model A useful tool for presenting the modelling and simulation results of indoor environment parameters. In: Abstracts of the International Conference on Healthy Air Better Work, Helsinki, Finland.
- 23. Oliveira, J.C., Shen, X. & Georganas, N.D. (2001). Collaborative virtual environment for industrial training and ecommerce. In: Proceedings of Workshop on Application of Virtual Reality Technologies for Future Telecommunication Systems. IEEE Globecom’ 2000 Conference, San Francisco.
- 24. Rankin, W., Hibit, R. and Sargent, R. (2000). Development and evaluation of the Maintenance Error Decision Aid (MEDA) process. International Journal of Industrial Ergonomics, (26) 2, pp. 261276.
- 25. Rasmussen, J. (1997) Risk management in a dynamic society: A modelling problem. Safety Science (27) 23, pp. 183213.
- 26. Reason, J. (1997) Managing the risks of organizational accidents. London: Ashgate Publishing Ltd.
- 27. Reason, J. and Hobbs, A. (2003) Managing maintenance error A Practical Guide. Burlington: Ashgate Publishing Company.
- 28. Reunanen, M., Scholliers, J., Säämänen, A., Viitaniemi, J., and Välisalo, T. (2004). Improving safety and dependability by enhancing the availability of product specific information. In: Proceedings of International Conference on Probabilistic Safety Assessment and Management. PSAM7ESREL'04, Berlin: SpringerVerlag.
- 29. SAE J8172. (1991). Engineering design serviceability guidelines – construction and industrial machinery – Maintainability index – OffRoad Work Machines. Society of Automotive Engineers, Warrendale, PA.
- 30. Sasou, K. and Reason, J. (1999) Team errors: definition and taxonomy. Reliability Engineering & System Safety, (65) 1, pp. 19.
- 31. SFSIEC 50191 (1996). International electrotechnical vocabulary. Dependability and quality of service. Finnish Standards Association, Helsinki.
- 32. Stammers, R.B, Carey, M.S., and Astley, J.A. (1990) Task analysis. In: J.R. Wilson, E.N. Corlett (eds.) Evaluation of Human Work. A practical ergonomics methodology (pp.134160). New York: Taylor & Francis.
- 33. Stephan, A. (2005) Maintainability assurance. [net document]. ICOMS 2005 presentation. Available: http://www.mesa.org.au/ICOMS05_064_stephan.pdf Referred 6.3.2008
- 34. Stone, R. (2001). Virtual reality for interactive training: an industrial practitioner’s viewpoint. International Journal of HumanComputer Studies, (55) 4, pp. 699711.
- 35. Su, K., Hwang, S. and Liu, T. (2000) Knowledge architecture and framework design for preventing human error in maintenance tasks. Expert Systems with Applications, (19) 3, pp. 219228.
- 36. Sundin, A. (2001) Participatory ergonomics in product development and workplace design. Supported by computerised visualisation and human modelling. Gothenburg: Chalmers University of Technology.
- 37. Sydänmaanlakka, P. (2007) Älykäs organisaatio. (Intelligent organisation) Talentum: Helsinki.
- 38. Taylor, J. C. (2000) The evolution and effectiveness of Maintenance Resource Management (MRM). International Journal of Industrial Ergonomics, (26) 2, pp. 201215.
- 39. Thomaidis, T. V. and Pistikopoulos, E. N. (1995). Towards the incorporation of flexibility, maintenance and safety in process design. Computers and Chemical Engineering, (19) suppl.1, pp. 687692.
- 40. Toriizuka, T. (2001) Application of performance shaping factor (PSF) for work improvement in industrial plant maintenance tasks. International Journal of Industrial Ergonomics, (28) 34, pp. 225236.
- 41. Viitaniemi, J., Leino, SP., Helin, K., and Määttä, T. (2001) Participating approach to work task design applying virtual environment. In: Proceedings of 33rd Annual Congress of the Nordic Ergonomics Society (pp. 7477). Tampere, Finland.
- 42. Viitaniemi, J., Säämänen, A., and Reunanen, M. (2004) A concept for safety and dependability information exploitation in maintenance planning and product development. In: Proceedings of NordDesign 2004 (pp. 8897). Tampere, Finland.
- 43. Viitaniemi, J., Määttä, T., Helin, K., Aromaa, S., Montonen, J., and Salmi, T. (2006) A simulation tool for production and human activity design. In: Proceedings of 5th CIRP International Seminar on Intelligent Computing in Manufacturing Engineering (pp. 635637). Ischia, Italy.
- 44. Williamson, A. M., Feyer, A.M. and Cairns, D. R. (1996) Industry Differences in Accident Causation. Safety Science, (24) 1, 112.
- 45. Wilson, B.H., Mourant, R.R., Li, M. and Xu, W. (1998) A virtual environment for training overhead crane operators: realtime implementation. IIE Transactions, (30), 7, 589595.
- 46. Winn, W. (1996) Virtual environments in maintenance training. In Pahl, G. (ed.) "Maintenance training", New York, SpringerVerlag.
- 47. AITRAM Advanced Integrated Training in Aircraft Maintenance, project web page. Available: www.aitram.de, Referred 18.3.2008
- 48. Dassault Systemes, web page. Available: www.3ds.com, Referred 18.3.2008
- 49. Siemens, web page. Available: www.ugs.com, Referred 18.3.2008
Papers relacionados

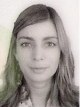
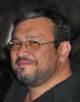
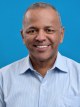
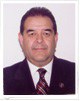
