Mata, F
Escuela Universitaria Politécnica de Almadén, Universidad de Castilla-La Mancha, Plaza Manuel Meca, 1, 13400, Almadén, Ciudad Real, España,+34 926 264007 francisco.mcabrera@uclm.es
ABSTRACT
ABSTRACT
Se reflexiona en esta comunicación sobre la importancia de la cultura del mantenimiento predictivo en aras de introducir mejoras significativas en las máquinas desde el punto de vista de la disponibilidad y especialmente en lo que se refiere a la seguridad.
Diferentes técnicas ya estandarizadas como el análisis de vibraciones o la termografía permiten monitorizar periódica o permanentemente el estado de funcionamiento de las máquinas y equipos industriales, lo que permite reflejar en su histórico todas las posibles anomalías e incidencias, de forma que se garantice el "buen estado de salud" de las mismas, al tiempo que su utilización quede siempre dentro de los estándares de seguridad.
Palabras clave
Palabras clave
Máquinas, Mantenimiento, Seguridad
MIGRACIÓN HACIA EL MANTENIMIENTO PREDICTIVO
Mantener consiste en aplicar las técnicas adecuadas para la correcta utilización de las máquinas e instalaciones, y asegurar el continuo funcionamiento del equipamiento productivo [1]. Las actividades de mantenimiento deben orientarse, por tanto, a reducir al mínimo la indisponibilidad de las máquinas y a eliminar las disfunciones que, aunque sean breves, distorsionan la continuidad del proceso productivo y la calidad de los productos.
Por otra parte, existe la idea generalizada de que el mantenimiento comienza cuando la máquina en cuestión tiene la primera avería. Pues bien, esta concepción es errónea a todos los efectos ya que el mantenimiento comienza mucho antes de la puesta en marcha de la propia máquina, esto es, como una variable más incorporada a los protocolos de diseño. Por tanto, desde el primer día en el que la máquina se pone en funcionamiento, se ha de tener establecido el proceso de mantenimiento que se ha de seguir (técnicas, medios, periodicidad…).
Otro de los papeles que debe desempeñar la función mantenimiento es el de determinar cuando la máquina ha dejado de ser rentable y debe ser reemplazada.
Cada vez más, se ha ido migrando del entretenimiento, entendido como arreglo o reparación, al mantenimiento, con connotaciones de predicción y prevención y con una visión a medio o largo plazo. Este cambio ha sido obligado, dado que los equipos de producción cada vez están más automatizados, los plazos de amortización son más cortos y los tiempos de indisponibilidad son económicamente más críticos y algunos incluso hasta prohibitivos.
Las tareas de mantenimiento, tanto las de gestión como las de ejecución propiamente dicha, deben ser realizadas siempre por profesionales cualificados, bien organizados como departamento propio de la empresa o bien, en caso de tener la función externalizada, perteneciente a empresas especializadas. Elprofesional del mantenimiento ha de ser un especialista en instrumentación y control, en mecánica, hidráulica o electrónica, pero también debe estar convenientemente entrenado en el manejo de complejos sistemas de monitorizado y diagnosis.
El tránsito del estado de fallo al estado de funcionamiento normal de una máquina o, en otras palabras, su recuperabilidad, viene condicionado por la existencia de un plan de mantenimiento, que incorpore las tareas específicas necesarias, y que se aplique de forma coherente a una función de mantenimiento bien organizada, en la que sean ejes rectores las políticas predictivas y preventivas.
En la Figura 1 se destaca cómo la definición de las políticas de mantenimiento en cualquier planta de producción incide directamente en los resultados, en particular en la relación coste-productividad, y también en la calidad del producto fabricado y en las vertientes de prevención y medio ambiente. Por tanto, una adecuada y eficaz política de mantenimiento, que prime el mantenimiento preventivo frente al correctivo y que, de manera especial, tenga bien definido un plan de predictivo de toda su maquinaria y equipamiento, redundará sin duda alguna en una mayor garantía de seguridad en cualquier intervención del hombre en el sistema.
Figura 1. Incidencia de la función mantenimiento en diversos ámbitos, en particular en la seguridad
La Figura 2 muestra la estructura básica de un plan de mantenimiento, en el que se contempla la seguridad como objetivo fundamental.
![]() |
Figura 2. Estructura de un plan de mantenimiento |
El grado de mantenibilidad de cualquier máquina o equipo industrial tiene que ver con que la técnica de mantenimiento que se le aplique sea la más apropiada [2-3], pero también depende directamente de otros factores como el diseño. Por ello, insistimos de nuevo en la importancia de un buen diseño. En la medida en que la máquina pueda devolverse al estado de funcionamiento con cierta facilidad, estará disponible para realizar las operaciones de modo fiable (dentro de los estándares de calidad) y con garantías de seguridad, tanto para el propio sistema como para el trabajador o cualquier persona que eventualmente interaccione con la misma (Figura 3).
![]() |
Figura 3. Relaciones entre mantenibilidad-disponibilidad-fiabilidad-seguridad [4] |
LA ASOCIACIÓN “PREDICTIVO-SEGURIDAD”
El mantenimiento predictivo o condicional permite evaluar externamente las condiciones de trabajo de la maquinaria mediante el control y la evolución de ciertos parámetros como pueden ser: presiones de engrase, vibraciones, temperaturas, etc.
Se realiza sin necesidad de recurrir a desmontajes y revisiones periódicas y tiene por objeto asegurar el correcto funcionamiento de la máquina mediante la inspección de su estado, tomando como referencia unos niveles de aceptabilidad conocidos de antemano.
Este tipo de mantenimiento supone la monitorización de la instalación, maquina o equipo para, mediante la instalación de sensores, captar alguna señal premonitoria que nos indique el estado en ese momento. Esto requiere instalaciones tecnológicas avanzadas y costosas, así como personal altamente cualificado, lo que hace que este tipo de mantenimiento no este muy generalizado aún, a excepción de las grandes plantas industriales con equipos de producción críticos (turbinas, molinos, grandes ventiladores, etc.).
Implantar un programa de mantenimiento predictivo en una planta industrial no es tarea fácil ya que requiere, por una parte, de un cambio cultural en las prácticas de mantenimiento y, por otra, de inversiones considerables tanto en equipamiento como en formación de personal. Los costes de personal, derivados en parte de la necesidad de formación específica de alto nivel, hacen que en muchos casos las empresas decidan externalizar el mantenimiento predictivo a empresas especializadas.
El esquema siguiente (Figura 4) recoge las principales técnicas de mantenimiento predictivo. De ellas, la más desarrollada y utilizada hasta ahora es el análisis de vibraciones, que permite extraer una información amplia del estado de funcionamiento del equipo, de forma continua o a intervalos preestablecidos, de manera que se establezcan patrones de referencia para analizar el estado de la máquina con el tiempo.
Figura 4. Principales técnicas utilizadas en mantenimiento predictivo
La mayor o menor inversión en equipos de monitorización de vibraciones dependerá del tipo de instalación a controlar y del nivel de fiabilidad buscado. Lo que no deja lugar a dudas es que, tras la inversión inicial, las ventajas que aporta un sistema de predictivo son enormes y permite a la empresa ahorrar importantes costes, derivados de:
- fallos inesperados en las máquinas
- paradas de producción no programadas
- consumo de repuestos
- necesidad de reparaciones
- pérdida de imagen de confianza ante los clientes y la competencia, a causa de la reducción de la calidad de procesos y productos
- accidentes de trabajo
- necesidad de reponer equipos e instalaciones, que ven reducida su vida útil
- disminución de la productividad
El plan de implantación de un programa de mantenimiento predictivo contempla varias fases [4]:
- Diseño:
- localización de los puntos de medida
- establecimiento de alarmas
- configuración de parámetros Instalación:
- placas de localización de puntos
- sensores fijos
- sistemas online Operación:
- descripción de las acciones específicas que deben desarrollarse
- definición de una lista de responsabilidades
El mantenimiento predictivo es una política de mantenimiento en la cual seseleccionan diferentes parámetros físicos asociados al funcionamiento de la máquina para ser sensorizados, medidos y registrados intermitentemente o deforma continua con el propósito de reducir, analizar y comparar los datos y la información obtenida para que pueda servir como soporte de ciertas decisiones que afecten a la operación o al propio mantenimiento de la máquina. Esto permite anticiparse a los fallos, programar las paradas e intervenciones sobre los equipos, aspectos sumamente importantes.
Sabida es la importancia de velar por que el funcionamiento y la operación de las máquinas tengan lugar en condiciones seguras, tanto para la integridad de la propia máquina y del proceso que se esté desarrollando como, de manera especial, para quienes desempeñan su trabajo con las mismas. Sin olvidar la directa relación entre seguridad y calidad y medio ambiente, tal y como se ha puesto de manifiesto con anterioridad, queremos destacar el binomio mantenimiento-seguridad. En realidad, se trata de una relación de causa-efecto, esto es, en la medida en que se garantice un correcto estado de la máquina a través del mantenimiento, se habrán sentado bases importantes para que el manejo de la máquina sea más seguro. Obviamente, sobre el estado final de “seguridad” influirán otros factores, relativos al propio diseño, a la tecnología utilizada, a la formación del trabajador, etc.; ahora bien, podemos aseverar que sin un buen mantenimiento la máquina no será nunca segura, pese a todo lo demás. Y si hablamos de un plan de mantenimiento adecuado, debemos referirnos a la aplicación de técnicas de diagnóstico y predicción de fallos, como acciones preferentes, además de las inspecciones rutinarias o de las clásicas tareas de preventivo.
PERSPECTIVAS
Abogamos por una gestión integrada global, que incluya, como ya viene siendo habitual últimamente, prevención, medio ambiente y calidad, pero considerando también el mantenimiento, como función transversal imbricada en las anteriores (Figura 5), además de otras cuestiones también importantes como la responsabilidad social corporativa.
Figura 5. Los cuatro pilares de un sistema de gestión integral
Por tanto, ponemos el énfasis en ello, entendemos que las actuaciones de mantenimiento deben formar parte de las políticas de prevención de la empresa. En otras palabras, el mantenimiento debe estar al servicio de la prevención.
Los beneficios que aporta una adecuada planificación de las operaciones de mantenimiento se pueden cifrar en términos de:
- Disminución del riesgo, al reducir la probabilidad de ocurrencia de fallos indeseables o no visualizados.
- Mejora o recuperación de los niveles de eficiencia de la instalación o equipo
- Aumento de la vida operativa
- Cumplimiento de los requerimientos de seguridad y medioambientales
- Contribución a la mejora continua (calidad)
El mantenimiento condiciona la seguridad, como objetivo último de la legislación preventiva. La ligazón íntima entre mantenimiento y seguridad debe ser tenida en cuenta por todos aquellos que dedican sus esfuerzos al establecimiento de políticas preventivas en las organizaciones industriales, buscando reducir la siniestralidad laboral y velando en todo caso por mejorar las condiciones de trabajo. Integrar lafunción mantenimiento, tradicionalmente considerada como un apéndice de la producción, en las actuaciones preventivas, es un paso muy importante, dado que permitirá abordar el problema de una forma más global y no se dejarán cabos sueltos que finalmente puedan dar al traste con una planificación preventiva modelo. Y en este proceso de toma de decisiones, pensamos que, pese al mayor coste inicial, resulta muy conveniente apostar por las técnicas predictivas, por las ventajas que hemos comentado más arriba. De tal suerte que podamos abiertamente hablar no ya de mantenimiento predictivo, sino de un concepto más amplio que nos permita también diagnosticar y predecir la seguridad de uso de las máquinas.
REFERENCIAS
- 1. Kelly, A.; Harris, M.J. (1998). Gestión del mantenimiento industrial, Fundación REPSOL YPF, ISBN: 8492350601
- 2. Boucly, F. (1999). Gestión del mantenimiento, AENOR, ISBN: 8481431605
- 3. Botín, J.A. (2003). Gestión del mantenimiento, Fundación GómezPardo, ISBN: 849506331X
- 4. Mata, F. (2006). Apuntes de ingeniería del mantenimiento, AE, ISBN: 84611 43280
Papers relacionados
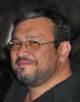




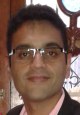