Adri C.P. Frijters
Arbouw
P.O. Box 8114, 1000 AC AMSTERDAM. Tel. 31 20 580 5515, fax
31 20 580 5555 frijters@arbouw.nl
INTRODUCTION
Safety studies in the Dutch construction industry reveal that 23% of all accidents involve tools or machinery. Better risk management for such equipment is therefore likely to decrease the number of occupational accidents. A risk management system has been developed, along with a Handbook for Risk Management of Tools and Machinery to facilitate its implementation in companies working in the construction industry. Successful implementation requires that the recommendations in the Handbook be easy to apply in practice.
This paper describes a study of the implementation of the Handbook for Risk Management of Tools and Machinery in the construction industry. The Handbook concerns the entire life cycle of the equipment used, from acquisition to disposal.
The system is set up in cooperation with employers’ organizations, as well as with the manufacturers and owners of the equipment. The risk management system aims first to provide practical support for construction companies in the maintenance and management of equipment as required by law. Second, the users – the experts and the Labour Inspectorate – must accept the system.
Organizations involved in the risk management system want to know whether its objectives have been realized. The practicability, impact and user satisfaction of the system is therefore of great interest.
The system is meant for construction companies of all sizes and of all kinds (e.g., road construction. painting, plastering and house construction). Implementation must also be possible in all companies, regardless of whether they have certified management systems (e.g., for quality, safety or environmental affairs).
There are about 14,600 construction companies in the Netherlands, 18.6% of which work in infrastructure construction trade. The Handbook is mainly intended for small and mid- sized enterprises (between 10 and 100 employees). In that category, 21.08% (3078) of the companies work in the residential/non-residential construction trade and 6.27% (915) work in the infrastructure construction trade.
The Handbook
The life cycle in the Handbook begins once a request for a price quotation has been filed. The request may involve purchasing, hiring or leasing a piece of equipment. The 1999 Working Conditions Act does not make distinctions among these types of requests. The cycle ends with the disposal of the work equipment.
The Handbook uses measurable, perceptible quality criteria to express the safety demands for the work equipment. These criteria are based on regulations and legislation, the prevailing standards and the known manuals for average equipment. The description of the quality criteria must be suitable for the process, the user and the procedure applied at a given stage in the process. The Handbook provides tests for these stages, in the form of checklists. The checklists provide a description of the optimal situation at the start of the problem-solving cycle. The figure illustrates the principle in the work
equipment manual.
![]() |
||
N e e d f o r W o r k e qu i pm e n t t q uot at i o n |
dr a f t qu ot at i o n
dr af
dr af t q uot at i o n
quo t a t i o n f o r w o r kq uo tea qt iuo inp mf o er n tw o r k
qu ot a tei oqnu ifpomr en t w o r ke qu i p m ent
p l a c e or de ri f qu ot at i o n i s s e l e c t ed
r e c e pt i o n l i s t
d e liv e r yse nd b a ck i n t h e ev en t of de f e ct s
in s p e c t i o n li s t s
i n s p ec t i on
ye s / n oif it f a ils t h e in s p e c t i o n ,t he w o r k e qu i pm e n t s h o u l d• b e r e pa i r ed o r
• re j e c t e d
m a i n t e n anc e
i f i t pa ss e s t h e i n sp ect i on ,a u t hor i s e i t f o r p r o d u c t i o nac t i v i t i es pr od uc t i on /'u s e ' p h a s e
c hec k l i s t s
The first stage involves drafting specifications for the contractor’s price quotation. In the request stage, the contractor should be aware of the criteria to be used by the client to test the work equipment required. To that end, criteria are marked as particular points of interest on the purchase lists. These points of interest are used when submitting the request to potential contractors for price quotations.
The second stage occurs when the company receives the work equipment. The company must inspect the work equipment upon delivery to ensure that it complies with requirements. The employee in charge of receiving the equipment uses lists to inspect the equipment.
The third stage involves maintenance and periodic inspections and the use. At the end of the maintenance phase, or at regular intervals, inspection lists should be used to determine whether the work equipment still fulfils all of the requirements. Article 7(4)(a) of the 1999 Decree states that the owner of the equipment is legally required to carry out such inspections. Under Article 7(6) of the 1999 Decree, an employer must designate a specific employee to make use of the list. In accordance with the work equipment manual, workers are trained to perform these inspections with the help of lists.
Beginning the use phase with an inspection, guarantees that the equipment is delivered in a safe condition.
The intervals between inspections depend on such factors as the intensity of use and the degree of wear. In some cases (e.g., VCA certification), contractors may specifyparticular intervals. All repair or maintenance work should be followed by inspections.
The inspection lists or results of inspections must be archived in order to ensure they can be demonstrated. Following the inspection, the work equipment can be put to use, starting a new phase.
During the use (production activities), the employee must decide, using checklists, whether the work equipment is safe to work with (Article 7(5)(1) of the 1999 Decree). The checklists should reveal the degree of risk to health and safety when working with the equipment.
Under Article 7(11)(a) of the 1999 Decree, the employer is responsible for the health and safety of his or her employees and is required to point out potential risks. The inspections help to identify unsafe equipment or unsafe workstations. By carrying out inspections, allstaff members are trained to identify defects.
The employee using the work equipment must complete the checklist. The intervals between completing the checklist depend on how frequently the equipment is used and the manner in which work equipment is handled in the company. The items on the list should be immediately obvious to all users. They should also be directly related to the safe functioning of the work equipment in the workstation. In the event of a negative score, the equipment should be withdrawn from use and sent for maintenance. If the problem involves a defect in the workstation, the problem must be resolved.
Using the purchase-, reception-, inspection- and checklists, staff members and other employees involved in the various phases can verify the safety of the work equipment while carrying out their tasks.
The company itself should be able and permitted to carry out all inspections for the equipment listed in the Handbook. As the work equipment is divided into risk classes, not all inspections must be carried out by the companies themselves (Goed Keuren? SZW op zoek naar een samenhangend keuringsbeleid [‘The Ministry of Social Affairs and Employment seeks a coherent inspection policy’], 1996). The company may make its own inspections of equipment up to Risk Class 2. As a result, work equipment with a risk class higher than 2 is not included in the Handbook.
OBJECTIVES OF THE STUDY
The objectives of this study were to determine:
- Whether the recommendations in the Handbook can be readily applied in practice in all sort of companies,
- The degree to which the recommendations have been applied,
- Whether, in the opinion of the companies concerned, the recommendations have indeed enhanced safety,
- Whether the recommendations have resulted in demonstrable change in management.
Conclusions from the research will provide input for further optimization of the system.
METHOD
A number of methodological options were appropriate for this type of research, including:
D Expert assessment on site,
D Expert assessment on site based on a questionnaire,
D Questionnaires without answer categories,
D Questionnaires with answer categories,
D Telephonic poll.
For this study, we distributed a questionnaire with answer categories by mail. This choice was based on experiences reported in other studies and on financial feasibility.
The questions were grouped into four clusters. The first cluster of questions concerned the company, the second concerned the system that had been implemented, the third cluster concerned chances, and the fourth concerned the quality of the Handbook.
It was necessary for all of the items on the questionnaire to be easy to understand, with answers that were readily accessible in the company.
A questionnaire-based survey was conducted among a sample group (N= 325) selected at random from the total number of users of the Handbook (N = 1500). The sample group was asked to complete a first questionnaire shortly after receipt of the Handbook, followed by a second questionnaire six months later. A non-response survey was conducted among the sample group that did not return the second questionnaire.
The survey was intended to determine system quality and the overall opinion of the system from the perspective of the user.
RESULTS
Fifty-six companies responded to both questionnaires, 75 responded only to the first questionnaire and 65 companies responded only to the second questionnaire.
The response rates were 40.3% (131 completed forms) for the first questionnaire and 37.2% (121 completed forms) for the second.
Respondents were classified according to sector. In both questionnaires, 45% of the respondents were in public works (infrastructure construction trade) and 55% were in the residential/non-residential construction trade.
Companies that were certified in any form were as follows:
61.9 % residential/non-residential construction trade,79.4 % infrastructure construction trade
The survey revealed that 53% of companies reported changes in the way that tools and equipment were managed following the introduction of the Handbook.
Those companies can be classified as follows:
Residential/non-residential construction trade ....50.0% Infrastructure construction trade......................61.8% Specialized companies ....................................46.9%
0 - 20 employees ...........................................59.1%21 - 100 employees .......................................56.0%101 and more employees ................................47.2%
Non-certified companies .................................48.5%
Certified companies........................................55.8%
All changes intended to enhance safety were directly related to the recommendations of the Handbook.
% refers to columntotal |
More critical purchase |
Higher frequency of assessments |
Higher frequency of better assessments |
Higher frequency of control by employees |
Higher frequency of preventive maintenance |
Other |
||||||||||||||
Number of answers |
All |
27.6% |
29.3% |
41.4% |
29.3% |
36.2% |
13.8% |
|||||||||||||
Certified |
14.5% |
18.4% |
22.4% |
13.2% |
17.1% |
9.2% |
||||||||||||||
Branch |
Residential/non- residential construction trade |
9.5% |
11.9% |
28.6% |
11.9% |
14.3% |
7.1% |
|||||||||||||
Infrastructure construction trade |
17.6% |
20.6% |
20.6% |
11.8% |
23.5% |
5.9% |
||||||||||||||
Specialized |
18.8% |
15.6% |
12.5% |
21.9% |
18.8% |
9.4% |
||||||||||||||
Number of employees |
0 - 20 |
13.6% |
13.6% |
18.2% |
22.7% |
31.8% |
0% |
|||||||||||||
21-100 |
22.0% |
22.0% |
24.0% |
14.0% |
20.0% |
8.0% |
||||||||||||||
|
Papers relacionados

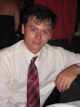

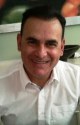
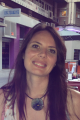
